Preparation method of isopropylbenzene and obtained isopropylbenzene
A technology for cumene and propylbenzene catalysts, which is applied in chemical instruments and methods, catalyst activation/preparation, and hydrocarbon production from oxygen-containing organic compounds, etc., can solve the problems of acetophenone hydrogenation, low selectivity of cumene, and catalyst Poor stability and other issues
- Summary
- Abstract
- Description
- Claims
- Application Information
AI Technical Summary
Problems solved by technology
Method used
Image
Examples
Embodiment 1
[0044] Weigh 0.5gPdCl 2 and 2.5 g of glucose were dissolved in a prepared solution containing 10.0 g of concentrated hydrochloric acid, 5.0 g of citric acid and 100 g of water, and the pH value of the solution was adjusted to 3 with lye to obtain a Pd impregnation solution. Heat the impregnating solution to 80°C, weigh 25g of alumina carrier, immerse it in the Pd impregnating solution, stir it thoroughly for 10min, filter it, wash it with deionized water, dry it at 100°C for 12h, and place it in a muffle furnace (nitrogen atmosphere ) at 500°C for 4 hours to obtain catalyst A1. The main composition of catalyst A1 is shown in Table 1.
[0045] Weigh 20mL of catalyst and load it into the reactor. The catalyst is reduced at 150°C for 8h. The benzyl alcohol raw material contains 55.0wt.% α,α-dimethylbenzyl alcohol, 1.3wt.% acetophenone and 42.8wt.% iso Propylbenzene, reaction pressure 2.0MPa, inlet temperature 160°C, H 2 / benzyl alcohol molar ratio is 6.0, liquid space velocity ...
Embodiment 2
[0047] Weigh 0.5gPdCl 2 and 5.0 g of glucose were dissolved in a prepared solution containing 10.0 g of concentrated hydrochloric acid, 5.0 g of citric acid and 100 g of water, and the pH value of the solution was adjusted to 3 with lye to obtain a Pd impregnation solution. Heat the impregnating solution to 80°C, weigh 25g of alumina carrier, immerse it in the Pd impregnating solution, stir it thoroughly for 10min, filter it, wash it with deionized water, dry it at 100°C for 12h, and place it in a muffle furnace (nitrogen atmosphere ) at 500°C for 4 hours to obtain catalyst A2. The main composition of catalyst A2 is shown in Table 1.
[0048] Weigh 20mL of catalyst and load it into the reactor. The catalyst is reduced at 150°C for 8h. The benzyl alcohol raw material contains 55.0wt.% α,α-dimethylbenzyl alcohol, 1.3wt.% acetophenone and 42.8wt.% iso Propylbenzene, reaction pressure 2.0MPa, inlet temperature 160°C, H 2 / benzyl alcohol molar ratio is 6.0, liquid space velocity ...
Embodiment 3
[0050] Weigh 0.5gPdCl 2 Dissolve in a prepared solution containing 10.0 g of concentrated hydrochloric acid, 5.0 g of citric acid and 100 g of water, and adjust the pH value of the solution to 3 with lye to obtain a Pd impregnation solution. Heat the impregnating solution to 80°C, weigh 25g of alumina carrier and immerse it in the Pd impregnating solution, fully stir for 10min, filter and wash with deionized water, dry at 100°C for 12h, and then bake in a muffle furnace at 500°C for 4h , the vested intermediate A'3.
[0051] Weigh 5.0g of glucose and dissolve it in 20g of water, soak the intermediate A'3 in the aqueous glucose solution, let it stand for 6h, dry it at 100°C for 12h, and then bake it in a muffle furnace (nitrogen atmosphere) at 500°C for 4h to obtain the catalyst A3. The main composition of catalyst A3 is shown in Table 1.
[0052] Weigh 20mL of catalyst and load it into the reactor. The catalyst is reduced at 150°C for 8h. The benzyl alcohol raw material cont...
PUM
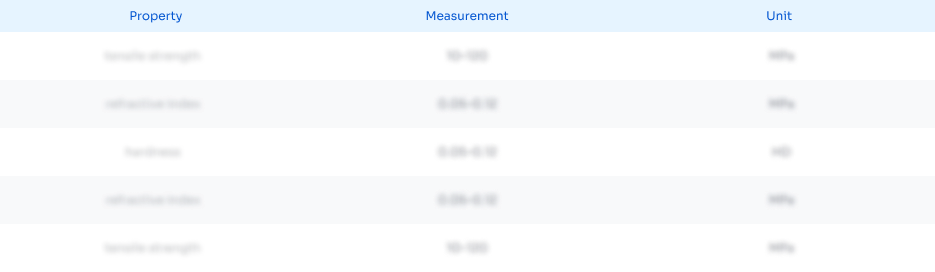
Abstract
Description
Claims
Application Information

- Generate Ideas
- Intellectual Property
- Life Sciences
- Materials
- Tech Scout
- Unparalleled Data Quality
- Higher Quality Content
- 60% Fewer Hallucinations
Browse by: Latest US Patents, China's latest patents, Technical Efficacy Thesaurus, Application Domain, Technology Topic, Popular Technical Reports.
© 2025 PatSnap. All rights reserved.Legal|Privacy policy|Modern Slavery Act Transparency Statement|Sitemap|About US| Contact US: help@patsnap.com