Steel bridge deck U rib butt joint fatigue strengthening structure and method based on bonding
A technology for butt joints and steel bridge decks, used in bridge reinforcement, bridges, bridge parts, etc., can solve the problems of difficulty in preventing further expansion of fatigue cracks, weakening of structural section damage, and high construction quality requirements, reducing the risk of fatigue damage and optimizing Stress distribution, effect of suppressing crack growth
- Summary
- Abstract
- Description
- Claims
- Application Information
AI Technical Summary
Problems solved by technology
Method used
Image
Examples
Embodiment 1
[0038] Such as figure 1As shown, the U-rib butt joint 12 includes a first U-rib 3, a second U-rib 4, and a U-rib embedding section 5 arranged between the end of the first U-rib 3 and the end of the second U-rib 4, and the U-rib U-rib butt welds 6 are provided between one end of the interlocking section 5 and the end of the first U-rib 3 , and between the other end of the U-rib interpolation section 5 and the end of the second U-rib 4 , and fiber-reinforced composite materials Layer 1 covers the outside of the U-rib butt weld 6 .
[0039] Such as figure 2 , image 3 , Figure 4 The shown bonded steel bridge deck U-rib butt joint fatigue strengthening structure includes the fiber reinforced composite material layer 1 wrapped at the U-rib butt joint 12 and the fiber-reinforced composite material layer 1 and the U-rib butt joint 12 Adhesive layer 2 between.
[0040] Wherein, the covering range of the fiber-reinforced composite material layer 1 includes the areas on the first...
Embodiment 2
[0048] In this embodiment, the fiber reinforced composite material layer 1 is made of carbon fiber reinforced composite material.
[0049] The reinforced structure includes 10 layers of fiber-reinforced composite material layers 1 superimposed and coated at the U-rib butt joint 12, the U-rib butt joint 12 and the fiber-reinforced composite material layer 1, and between adjacent fiber-reinforced composite material layers 1 An adhesive layer 2 is provided.
[0050] All the other are with embodiment 1.
Embodiment 3
[0052] In this embodiment, the fiber reinforced composite material layer 1 is made of aramid fiber reinforced composite material.
[0053] The reinforced structure includes 7 layers of fiber-reinforced composite material layers 1 that are superimposed and coated at the U-rib butt joint 12. An adhesive layer 2 is provided.
[0054] All the other are with embodiment 1.
PUM
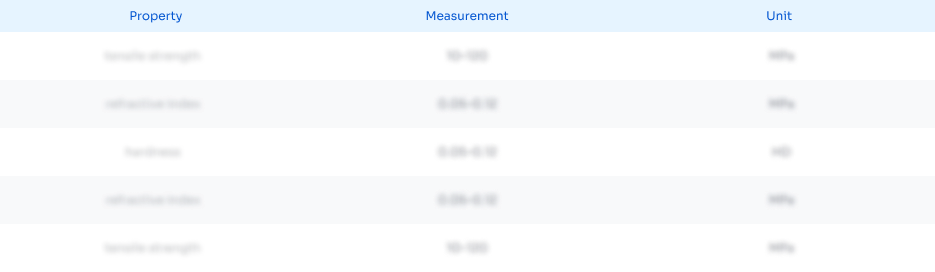
Abstract
Description
Claims
Application Information

- R&D
- Intellectual Property
- Life Sciences
- Materials
- Tech Scout
- Unparalleled Data Quality
- Higher Quality Content
- 60% Fewer Hallucinations
Browse by: Latest US Patents, China's latest patents, Technical Efficacy Thesaurus, Application Domain, Technology Topic, Popular Technical Reports.
© 2025 PatSnap. All rights reserved.Legal|Privacy policy|Modern Slavery Act Transparency Statement|Sitemap|About US| Contact US: help@patsnap.com