A continuous production process of azo disperse dyes with ester groups
A production process and technology of disperse dyes, applied in the direction of azo dyes, monoazo dyes, organic dyes, etc., can solve the problems of prone to hydrolysis reaction, increase the cost of wastewater treatment, increase the difficulty of recycling dye washing water and mother liquor water, etc. , to achieve the effect of reducing hydrolysis and diazo decomposition, reducing the cost of production equipment and site use, and avoiding material decomposition and hydrolysis
- Summary
- Abstract
- Description
- Claims
- Application Information
AI Technical Summary
Problems solved by technology
Method used
Image
Examples
Embodiment 1
[0043] (1) Material ultrasonic pipeline mixing
[0044] Coupling component intermediate 3-(N,N-diacetoxyethyl)amino-4-methoxyacetanilide Flow rate control 201~211g / min, 2,4-bis The flow rate of the nitro-6-chloroaniline diazonium salt solution is controlled at 400g / min, and the water flow rate is adjusted at 3000-3500g / min. The above-mentioned three strands of materials are continuously pumped into the ultrasonic pipeline mixer through the metering pump, and the frequency of the ultrasonic generator is 25kHz- 100kHz, power density 0.5-1W / cm 2 , The residence time of the material during the mixing process is 1 to 2 minutes, and the temperature of the mixer is controlled at -2 to 5 °C.
[0045] (2) Coupling reaction
[0046] The above (1) materials are directly transported into the rotating bed of the high-gravity reactor after being mixed by the mixer, and the mass transfer effect is enhanced through the high-gravity equipment to strengthen the coupling reaction to obtain the...
Embodiment 2
[0050] (1) Material ultrasonic pipeline mixing
[0051] Coupling component intermediate 4-(N,N-diacetoxyethyl)-2-acetamidoaniline flow rate control 217~227g / min, use 28% content of nitrosyl sulfuric acid to prepare o-chloro-p-nitroaniline weight The nitrogen salt solution flow rate is controlled at 400g / min, and the water flow rate is controlled at 3000-3500g / min. The above-mentioned three streams of materials are continuously pumped into the ultrasonic pipeline mixer through the metering pump. The frequency of the ultrasonic generator is 25kHz-100kHz, and the power density is 0.5-1W. / cm 2 , The residence time of the material during the mixing process is 1 to 2 minutes, and the temperature of the mixer is controlled at -2 to 5 °C.
[0052] (2) Coupling reaction
[0053] The above (1) materials are directly transported into the rotating bed of the high-gravity reactor after being mixed by the mixer, and the mass transfer effect is enhanced through the high-gravity equipment ...
Embodiment 3
[0057] (1) Material ultrasonic pipeline mixing
[0058] Coupling component intermediate 4-(N-cyanoethyl-N-acetoxyethyl)aniline flow control 150~155g / min, 2,6-dichloro-4-nitrosylsulfuric acid prepared with 28% content The flow rate of phenylaniline diazonium salt solution is controlled at 400g / min, and the water flow rate is adjusted at 3000-3500g / min. The above-mentioned three strands of materials are continuously pumped into the ultrasonic pipeline mixer through the metering pump. The frequency of the ultrasonic generator is 25kHz-100kHz, and the power density is 0.5-1W / cm 2 , The residence time of the material during the mixing process is 1-2min, and the temperature of the mixer is controlled at 0-5°C.
[0059] (2) Coupling reaction
[0060] The above (1) materials are directly transported into the rotating bed of the high-gravity reactor after being mixed by the mixer, and the mass transfer effect is enhanced through the high-gravity equipment to strengthen the coupling r...
PUM
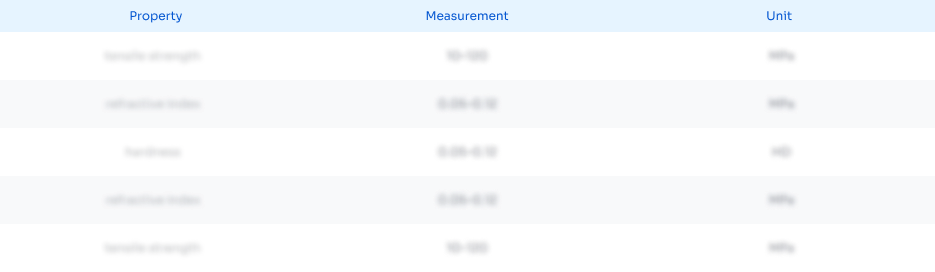
Abstract
Description
Claims
Application Information

- R&D
- Intellectual Property
- Life Sciences
- Materials
- Tech Scout
- Unparalleled Data Quality
- Higher Quality Content
- 60% Fewer Hallucinations
Browse by: Latest US Patents, China's latest patents, Technical Efficacy Thesaurus, Application Domain, Technology Topic, Popular Technical Reports.
© 2025 PatSnap. All rights reserved.Legal|Privacy policy|Modern Slavery Act Transparency Statement|Sitemap|About US| Contact US: help@patsnap.com