In-situ preparation method of HfC-based ternary carbide gradient coating on surface of carbon material
A ternary carbide and gradient coating technology, applied in the field of high temperature materials, can solve the problems of low bonding strength between the coating and the carbon material matrix, complex preparation process and high equipment requirements, achieve good physical properties, simple preparation method, The effect of uniform composition
- Summary
- Abstract
- Description
- Claims
- Application Information
AI Technical Summary
Problems solved by technology
Method used
Image
Examples
preparation example Construction
[0035] A kind of preparation method of HfC base ternary carbide gradient coating on carbon material surface of the present invention, comprises steps as follows:
[0036] (1) Hafnium (Hf) powder or Hf powder and hafnium oxide (HfO 2 ) powder mixture as hafnium source, with graphite or carbon / carbon composite as matrix, with TiO 2 and ZrO 2 They are respectively the second metal principal element titanium source, zirconium source, and ammonium chloride (NH 4 Cl) powder is the active agent, and the hafnium source, the active agent are uniformly mixed with one of the titanium source and the zirconium source to obtain the penetrating agent;
[0037] (2) placing the infiltrating agent in a reaction vessel, and horizontally suspending the carbon material matrix directly above the infiltrating agent;
[0038] (3) Place the reaction vessel with the mixed powder and carbon material matrix in a vacuum furnace, repeat the vacuuming-filling inert gas operation, and finally inject the i...
Embodiment 1
[0054] A (Hf, Ti)C coating on the graphite substrate surface of the present invention, the (Hf, Ti)C coating is formed by in-situ gas phase reaction on the graphite substrate, and (Hf, Ti)C is filled on the graphite substrate surface And in the pores inside the graphite matrix, the (Hf, Ti)C coating not only covers the surface of the graphite matrix, but also penetrates into the interior of the graphite matrix, forming a gradient (Hf, Ti)C coating that changes from the surface of the matrix to the interior.
[0055] In this embodiment, the (Hf, Ti)C has a composition gradient from the surface of the graphite matrix to the interior of the graphite matrix, and the depth of (Hf, Ti)C penetrating into the interior of the graphite matrix is about 180 μm, that is, the (Hf, Ti)C gradient layer The thickness is 180 μm.
[0056] A kind of preparation method of the (Hf, Ti) C gradient coating on the graphite substrate surface of the present embodiment, comprises the following steps: ...
Embodiment 2
[0064] A (Hf, Zr) C coating on the graphite substrate surface of the present invention, the (Hf, Zr) C coating is formed by in-situ gas phase reaction on the graphite substrate, and the (Hf, Zr) C is filled in the graphite substrate In the surface and internal pores, the (Hf, Zr)C coating not only covers the surface of the graphite substrate, but also penetrates into the interior of the graphite substrate, forming a gradient (Hf, Zr)C coating that changes from the surface of the substrate to the interior.
[0065] In this embodiment, the (Hf, Zr)C has a composition gradient from the surface of the graphite matrix to the interior of the graphite matrix, and the depth of (Hf, Zr)C penetrating into the interior of the graphite matrix is about 350 μm, that is, the (Hf, Zr)C gradient layer The thickness is 350 μm.
[0066] A kind of preparation method of the (Hf, Zr) C gradient coating on the graphite substrate surface of the present embodiment, comprises the following steps:
...
PUM
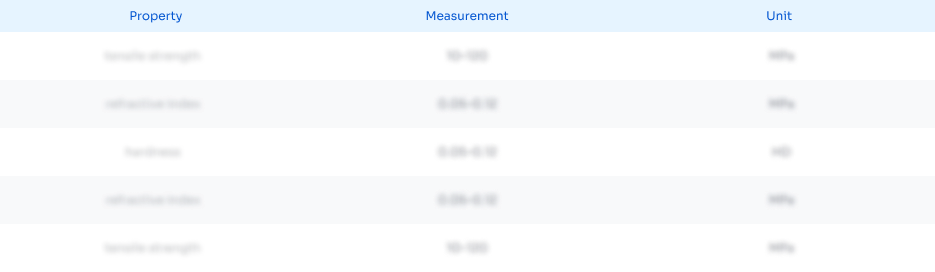
Abstract
Description
Claims
Application Information

- Generate Ideas
- Intellectual Property
- Life Sciences
- Materials
- Tech Scout
- Unparalleled Data Quality
- Higher Quality Content
- 60% Fewer Hallucinations
Browse by: Latest US Patents, China's latest patents, Technical Efficacy Thesaurus, Application Domain, Technology Topic, Popular Technical Reports.
© 2025 PatSnap. All rights reserved.Legal|Privacy policy|Modern Slavery Act Transparency Statement|Sitemap|About US| Contact US: help@patsnap.com