Intermetallic compound and carbonitride co-hardened powder metallurgy high-speed steel and preparation method thereof
A technology of intermetallic compounds and carbonitrides, applied in the field of machining tools, can solve the problems of excessive grain size, hindering grain growth, low hardness and wear resistance, etc.
- Summary
- Abstract
- Description
- Claims
- Application Information
AI Technical Summary
Problems solved by technology
Method used
Image
Examples
Embodiment 1
[0040] The mass fractions are: Co: 25%, Mo: 12%, W: 4%, TiC: 2%, Ti(C, N): 2%, the balance is Fe, and the powder is prepared. Mix the prepared raw material powder, 4wt% forming agent paraffin, and 0.5wt% carbon black, and place them in a planetary ball mill ball mill tank for wet ball milling. During the ball milling process, the ball milling medium is alcohol, the protective gas is nitrogen, and the ball-to-battery ratio is 5: 1. The speed is 260r / min, and the ball milling time is 48h. After the ball milling is completed, it is dried in a vacuum drying oven, dried and sieved to granulate, and the mixed powder is subjected to unidirectional molding under a pressure of 180 MPa to obtain a compact. The compact is placed in a vacuum sintering furnace for sintering, the final sintering temperature is 1340°C, the highest temperature stage is kept for 2 hours, and the sintered compact is obtained after cooling with the furnace. The sintered billet was preheated at 1120°C in a nitrog...
Embodiment 2
[0042] The mass fractions are: Co: 20%, Mo: 11%, W: 5%, TiN: 4%, Ti(C, N): 4%, the balance is Fe, and the powder is prepared. Mix the prepared raw material powder, 3wt% forming agent paraffin, and 0.6wt% carbon black, and place them in the ball mill tank of a planetary ball mill for wet ball milling. During the ball milling process, the milling medium is alcohol, the protective gas is nitrogen, and the ball-to-battery ratio is 6: 1. The rotating speed is 240r / min, and the ball milling time is 50h. After the ball milling is completed, it is dried in a vacuum drying box, dried and sieved to granulate, and the mixed powder is subjected to unidirectional molding under a pressure of 160 MPa to obtain a compact. The compact is placed in a vacuum sintering furnace for sintering, the final sintering temperature is 1370°C, the highest temperature stage is kept for 2 hours, and the sintered compact is obtained after cooling with the furnace. The sintered billet was preheated at 1130°C i...
Embodiment 3
[0044] The mass fractions are: Co: 20%, Mo: 15%, W: 5%, NbC: 8%, the balance is Fe, and the powder is prepared. Mix the prepared raw material powder, 3wt% forming agent paraffin, and 0.6wt% carbon black, and place them in the ball mill tank of a planetary ball mill for wet ball milling. During the ball milling process, the milling medium is alcohol, the protective gas is nitrogen, and the ball-to-battery ratio is 6: 1. The speed is 220r / min, and the ball milling time is 60h. After the ball milling is completed, it is dried in a vacuum drying oven, dried and sieved to granulate, and the mixed powder is subjected to unidirectional molding under a pressure of 180 MPa to obtain a compact. The compact is placed in a vacuum sintering furnace for sintering, the final sintering temperature is 1340°C, the highest temperature stage is kept for 2 hours, and the sintered compact is obtained after cooling with the furnace. The sintered billet was preheated at 1130°C in a nitrogen-protected...
PUM
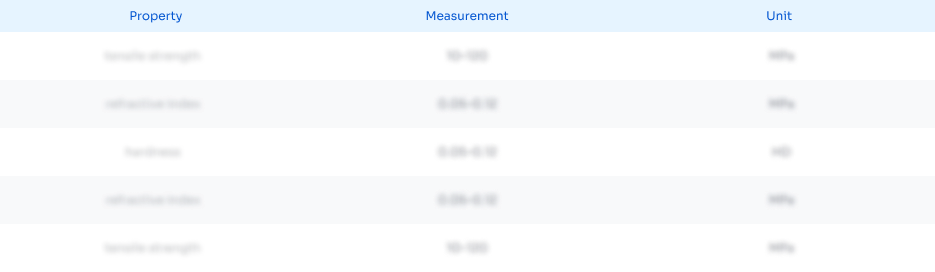
Abstract
Description
Claims
Application Information

- R&D
- Intellectual Property
- Life Sciences
- Materials
- Tech Scout
- Unparalleled Data Quality
- Higher Quality Content
- 60% Fewer Hallucinations
Browse by: Latest US Patents, China's latest patents, Technical Efficacy Thesaurus, Application Domain, Technology Topic, Popular Technical Reports.
© 2025 PatSnap. All rights reserved.Legal|Privacy policy|Modern Slavery Act Transparency Statement|Sitemap|About US| Contact US: help@patsnap.com