Preparation method of ceramic-based conductive coating
A conductive coating, ceramic-based technology, applied in conductive coatings, epoxy resin coatings, coatings, etc., can solve the problems of difficult conductivity, decrease in conductivity, increase in coating resistivity, etc., and achieve excellent salt corrosion resistance. Effect
- Summary
- Abstract
- Description
- Claims
- Application Information
AI Technical Summary
Problems solved by technology
Method used
Examples
Embodiment 1
[0015] A preparation method of ceramic-based conductive paint, comprising the following steps:
[0016] S1. adding lanthanum nitrate to deionized water, the configuration concentration is 5wt%, to obtain an aqueous solution of lanthanum nitrate;
[0017] S2. Dissolving tetrabutyl titanate in ethanol containing citric acid and stirring until transparent to obtain a tetrabutyl titanate solution with a concentration of 2 wt %;
[0018] S3. dissolving barium carbonate in citric acid solution, stirring evenly to obtain a barium carbonate solution with a concentration of 2-6%, wherein the molar ratio of lanthanum nitrate, tetrabutyl titanate and barium carbonate is 0.2:0.5:1;
[0019] S4. Add lanthanum nitrate and tetrabutyl titanate solution dropwise to the barium carbonate solution, adjust the pH of the solution to 6, stir in a water bath at 75°C to obtain a sol, and then place the sol in a muffle furnace at 800°C Calcined for 6h to obtain lanthanum-modified barium titanate;
[...
Embodiment 2
[0023] A preparation method of ceramic-based conductive paint, comprising the following steps:
[0024] S1. adding lanthanum nitrate to deionized water, the configuration concentration is 12wt%, to obtain an aqueous solution of lanthanum nitrate;
[0025] S2. Dissolving tetrabutyl titanate in ethanol containing citric acid and stirring until transparent to obtain a tetrabutyl titanate solution with a concentration of 6 wt %;
[0026] S3. dissolving barium carbonate in citric acid solution, stirring evenly to obtain a barium carbonate solution with a concentration of 2-6%, wherein the molar ratio of lanthanum nitrate, tetrabutyl titanate and barium carbonate is 0.5:0.8:1;
[0027] S4. Add lanthanum nitrate and tetrabutyl titanate solution dropwise to the barium carbonate solution, adjust the pH of the solution to 8, stir in a water bath at 90°C to obtain a sol, and then place the sol in a muffle furnace at 1000°C Calcined for 4h to obtain lanthanum-modified barium titanate;
...
Embodiment 3
[0031] A preparation method of ceramic-based conductive paint, comprising the following steps:
[0032] S1. adding lanthanum nitrate to deionized water, the configuration concentration is 9wt%, to obtain an aqueous solution of lanthanum nitrate;
[0033] S2. Dissolving tetrabutyl titanate in ethanol containing citric acid and stirring until transparent to obtain a tetrabutyl titanate solution with a concentration of 4wt%;
[0034] S3. dissolving barium carbonate in citric acid solution, stirring evenly to obtain a barium carbonate solution with a concentration of 4%, wherein the molar ratio of lanthanum nitrate, tetrabutyl titanate and barium carbonate is 0.4:0.7:1;
[0035] S4. Add lanthanum nitrate and tetrabutyl titanate solution dropwise to the barium carbonate solution, adjust the pH of the solution to 7, stir in a water bath at 85°C to obtain a sol, and then place the sol in a muffle furnace at 900°C Calcined for 5h to obtain lanthanum-modified barium titanate;
[0036...
PUM
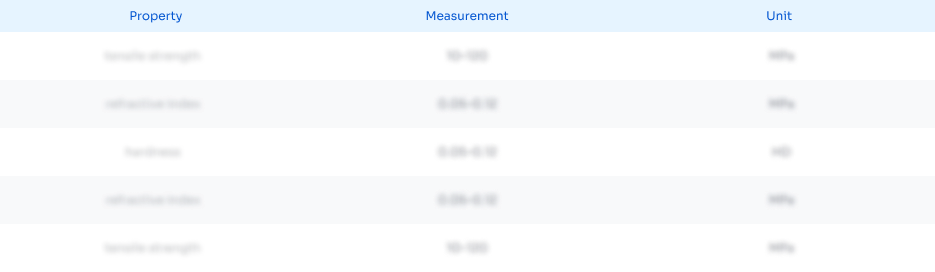
Abstract
Description
Claims
Application Information

- R&D Engineer
- R&D Manager
- IP Professional
- Industry Leading Data Capabilities
- Powerful AI technology
- Patent DNA Extraction
Browse by: Latest US Patents, China's latest patents, Technical Efficacy Thesaurus, Application Domain, Technology Topic, Popular Technical Reports.
© 2024 PatSnap. All rights reserved.Legal|Privacy policy|Modern Slavery Act Transparency Statement|Sitemap|About US| Contact US: help@patsnap.com