Salt corrosion resisting cable insulation rubber for oceanic tidal power generation and preparation method thereof
A cable insulation and tidal technology, applied to rubber insulators, organic insulators, etc., can solve problems such as prone to failure, shortened service life, and increased engineering costs, and achieves excellent salt corrosion resistance, low equipment requirements, and simple and feasible preparation methods Effect
- Summary
- Abstract
- Description
- Claims
- Application Information
AI Technical Summary
Problems solved by technology
Method used
Image
Examples
Embodiment 1
[0022] Example 1: Preparation of Salt Corrosion Resistant Cable Insulation Rubber
[0023] Raw material weight ratio:
[0024] EPDM rubber, 55 parts; butadiene rubber, 15 parts; polysulfide rubber, 10 parts; alkylphenol ethoxylates, 5 parts; pentaerythritol tetralaurate, 8 parts; methyl benzotriazole , 3 parts; sodium hexametaphosphate, 2 parts; polydimethylsiloxane, 2 parts; triallyl isocyanurate, 3 parts; 2-mercaptobenzimidazole, 1 part; A total of 4 parts of ester and propylparaben, the ratio of ethyl paraben and propylparaben by weight is 3:1.
[0025] Preparation:
[0026] Step S1, uniformly mixing EPDM rubber, butadiene rubber, and polysulfide rubber to obtain a main material, placing the main material in a single-screw extruder for blending, and granulating to obtain a base resin;
[0027] Step S2, open the internal mixer and preheat it to 50-55°C, then add the base resin obtained in step S1 for banburying, the banburying time is 4-6 minutes, and the mixture 1 is obt...
Embodiment 2
[0030] Example 2: Preparation of Salt Corrosion Resistant Cable Insulation Rubber
[0031] Raw material weight ratio:
[0032] EPDM rubber, 50 parts; Butadiene rubber, 10 parts; Polysulfide rubber, 5 parts; Alkylphenol ethoxylates, 4 parts; Pentaerythritol tetralaurate, 6 parts; , 2 parts; sodium hexametaphosphate, 1 part; polydimethylsiloxane, 1 part; triallyl isocyanurate, 2 parts; 2-mercaptobenzimidazole, 0.8 parts; There are 3 parts in total of ester and propylparaben, and the ratio by weight of ethylparaben and propylparaben is 2:1.
[0033] Preparation:
[0034] Step S1, uniformly mixing EPDM rubber, butadiene rubber, and polysulfide rubber to obtain a main material, placing the main material in a single-screw extruder for blending, and granulating to obtain a base resin;
[0035] Step S2, open the internal mixer and preheat it to 50-55°C, then add the base resin obtained in step S1 for banburying, the banburying time is 4-6 minutes, and the mixture 1 is obtained;
...
Embodiment 3
[0038] Example 3: Preparation of Salt Corrosion Resistant Cable Insulation Rubber
[0039] Raw material weight ratio:
[0040] EPDM rubber, 60 parts; butadiene rubber, 20 parts; polysulfide rubber, 15 parts; alkylphenol ethoxylates, 6 parts; pentaerythritol tetralaurate, 10 parts; methyl benzotriazole , 4 parts; sodium hexametaphosphate, 3 parts; polydimethylsiloxane, 3 parts; triallyl isocyanurate, 4 parts; 2-mercaptobenzimidazole, 1.2 parts; There are 5 parts in total of ester and propylparaben, and the ratio by weight of ethylparaben and propylparaben is 4:1.
[0041] Preparation:
[0042]Step S1, uniformly mixing EPDM rubber, butadiene rubber, and polysulfide rubber to obtain a main material, placing the main material in a single-screw extruder for blending, and granulating to obtain a base resin;
[0043] Step S2, open the internal mixer and preheat it to 50-55°C, then add the base resin obtained in step S1 for banburying, the banburying time is 4-6 minutes, and the mi...
PUM
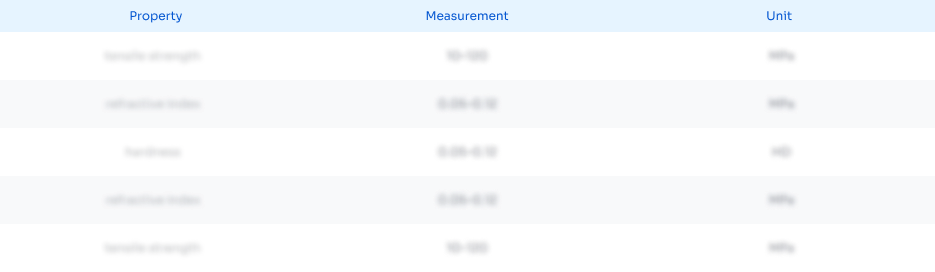
Abstract
Description
Claims
Application Information

- Generate Ideas
- Intellectual Property
- Life Sciences
- Materials
- Tech Scout
- Unparalleled Data Quality
- Higher Quality Content
- 60% Fewer Hallucinations
Browse by: Latest US Patents, China's latest patents, Technical Efficacy Thesaurus, Application Domain, Technology Topic, Popular Technical Reports.
© 2025 PatSnap. All rights reserved.Legal|Privacy policy|Modern Slavery Act Transparency Statement|Sitemap|About US| Contact US: help@patsnap.com