Salt-contamination-resistant cable material and preparation method thereof
A cable and salt-resistant technology, which is applied in the field of salt-corrosion-resistant cable materials and its preparation, can solve problems such as prone to failure, shortened service life, and shelving, and achieve the effect of excellent salt-corrosion resistance and long service life
- Summary
- Abstract
- Description
- Claims
- Application Information
AI Technical Summary
Problems solved by technology
Method used
Image
Examples
Embodiment 1
[0019] Embodiment 1: the preparation of cable material
[0020] Raw material weight ratio:
[0021] EPDM rubber, 57 parts; Butadiene rubber, 12 parts; Nitrile rubber, 8 parts; Dialkyl diphenylamine, 4 parts; Methacrylamide, 6 parts; Di-tert-butyl p-cresol, 4 parts Sodium hexametaphosphate, 3 parts; Mercaptoethanol, 4 parts; Tricresyl phosphate, 5 parts; Methyl salicylate, 3 parts; Tricresyl phosphate, 5 times of the weight part of methyl salicylate.
[0022] Preparation:
[0023] Step S1, uniformly mixing EPDM rubber, butadiene rubber, and nitrile rubber to obtain main ingredients, placing the main ingredients in a single-screw extruder for blending, and granulating to obtain a base resin;
[0024] Step S2, open the internal mixer and preheat it to 60°C, then add the base resin obtained in step S1 for banburying, the banburying time is 5min, and the mixture is obtained;
[0025] Step S3, add dialkyl diphenylamine, methacrylamide, di-tert-butyl p-cresol, sodium hexametaphosp...
Embodiment 2
[0027] Embodiment 2: the preparation of cable material
[0028] Raw material weight ratio:
[0029] EPDM rubber, 52 parts; Butadiene rubber, 8 parts; Nitrile rubber, 6 parts; Dialkyldiphenylamine, 3 parts; Methacrylamide, 5 parts; Sodium hexametaphosphate, 2 parts; Mercaptoethanol, 3 parts; Tricresyl phosphate, 4 parts; Methyl salicylate, 2 parts; Tricresyl phosphate, 4 times of the weight part of methyl salicylate.
[0030] Preparation:
[0031] Step S1, uniformly mixing EPDM rubber, butadiene rubber, and nitrile rubber to obtain main ingredients, placing the main ingredients in a single-screw extruder for blending, and granulating to obtain a base resin;
[0032] Step S2, open the internal mixer and preheat it to 60°C, then add the base resin obtained in step S1 for banburying, the banburying time is 5min, and the mixture is obtained;
[0033] Step S3, add dialkyl diphenylamine, methacrylamide, di-tert-butyl p-cresol, sodium hexametaphosphate, mercaptoethanol, tricresyl p...
Embodiment 3
[0035] Embodiment 3: the preparation of cable material
[0036] Raw material weight ratio:
[0037] EPDM rubber, 62 parts; Butadiene rubber, 16 parts; Nitrile rubber, 10 parts; Dialkyl diphenylamine, 5 parts; Methacrylamide, 7 parts; Sodium hexametaphosphate, 4 parts; Mercaptoethanol, 5 parts; Tricresyl phosphate, 6 parts; Methyl salicylate, 4 parts; Tricresyl phosphate, 6 times of the weight part of methyl salicylate.
[0038] Preparation:
[0039] Step S1, uniformly mixing EPDM rubber, butadiene rubber, and nitrile rubber to obtain main ingredients, placing the main ingredients in a single-screw extruder for blending, and granulating to obtain a base resin;
[0040] Step S2, open the internal mixer and preheat it to 60°C, then add the base resin obtained in step S1 for banburying, the banburying time is 5min, and the mixture is obtained;
[0041] Step S3, add dialkyl diphenylamine, methacrylamide, di-tert-butyl p-cresol, sodium hexametaphosphate, mercaptoethanol, tricresy...
PUM
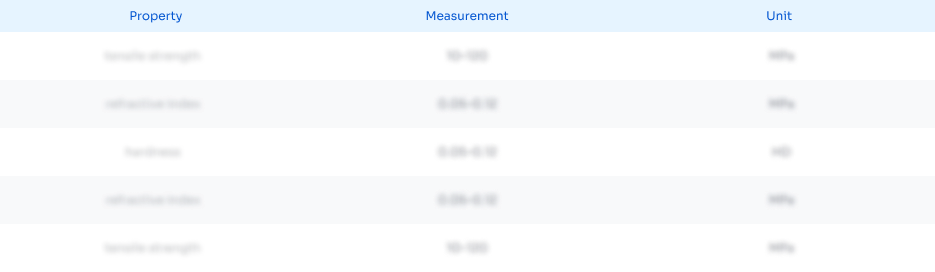
Abstract
Description
Claims
Application Information

- Generate Ideas
- Intellectual Property
- Life Sciences
- Materials
- Tech Scout
- Unparalleled Data Quality
- Higher Quality Content
- 60% Fewer Hallucinations
Browse by: Latest US Patents, China's latest patents, Technical Efficacy Thesaurus, Application Domain, Technology Topic, Popular Technical Reports.
© 2025 PatSnap. All rights reserved.Legal|Privacy policy|Modern Slavery Act Transparency Statement|Sitemap|About US| Contact US: help@patsnap.com