Method for regulating stress of multi-component laser cladding layer
A laser cladding and multi-component technology, which is applied in coating, metal material coating process, etc., can solve the problems of cladding layer cracking, brittleness, and cladding layer stress, etc., and achieve the effect of preventing cracks
- Summary
- Abstract
- Description
- Claims
- Application Information
AI Technical Summary
Problems solved by technology
Method used
Image
Examples
Embodiment 1
[0033] (1) Put the high-purity metal elemental powder Fe, Cr, Ni, Al, Co and Ti in the smelting furnace for arc melting to obtain the original ingot, and put the original ingot into the gas atomization powder making equipment Melting, while passing argon gas to form an impact on the melt, the melt is impacted and dispersed to form small droplets, and after cooling, the required FeCrNiAlCoTi pre-alloyed powder is formed, and the powder particle size is 58-130μm.
[0034] (2) Add Cr with a particle size of 58-130 μm to the FeCrNiAlCoTi pre-alloyed powder 3 C 2 Ceramic powder, mechanically mixed evenly and then dried, put into the coaxial synchronous powder feeder for use, wherein, Cr in the mixed alloy powder 3 C 2 The mass percentage of ceramic powder is 10%;
[0035] (3) Aim the laser head of the laser at the surface of the 42CrMo alloy steel;
[0036] (4) Through the coaxial synchronous powder feeder of step (1), the alloy powder is evenly and continuously sent to the sur...
Embodiment 2
[0042] The difference between embodiment 2 and embodiment 1 is only: Cr in the mixed alloy powder of embodiment 2 3 C 2 The mass percentage of ceramic powder is 12%; the laser coating process parameters are: laser power 1600W, scanning speed 7mm / s, spot diameter 4.5mm, argon gas flow rate 18L / min, powder feeding rate 8g / min, the overlap rate is 35%.
[0043] Figure 5 Be the metallographic diagram of embodiment 2 cladding layer, from Figure 5 It can be seen that there are no microcracks in the cladding layer, and the TiC particles generated by the in-situ reaction are evenly distributed.
Embodiment 3
[0045] The difference between embodiment 3 and embodiment 1 is only: Cr in the mixed alloy powder of embodiment 3 3 C 2 The mass percentage of ceramic powder is 14%. The laser coating process parameters are as follows: laser power is 2000W, scanning rate is 9mm / s, spot diameter is 4.5mm, argon gas flow rate is 20L / min, powder feeding rate is 12g / min, the overlap rate is 40%.
PUM
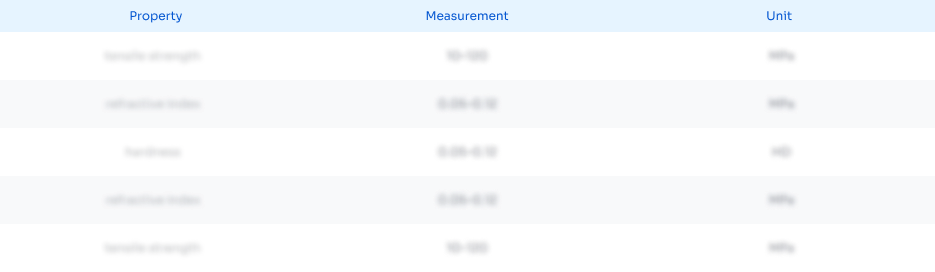
Abstract
Description
Claims
Application Information

- R&D
- Intellectual Property
- Life Sciences
- Materials
- Tech Scout
- Unparalleled Data Quality
- Higher Quality Content
- 60% Fewer Hallucinations
Browse by: Latest US Patents, China's latest patents, Technical Efficacy Thesaurus, Application Domain, Technology Topic, Popular Technical Reports.
© 2025 PatSnap. All rights reserved.Legal|Privacy policy|Modern Slavery Act Transparency Statement|Sitemap|About US| Contact US: help@patsnap.com