Special anti-corrosive coating for transmission tower and preparation method of anti-corrosive coating
A technology for anti-corrosion coatings and transmission towers, applied in anti-corrosion coatings, epoxy resin coatings, coatings, etc., can solve problems such as high content of polyphenylene sulfide resin, low surface tension of pure fluorine coatings, and uneven coating thickness. Achieve the effects of good adhesion, good controllability of coating thickness, and simple spraying
- Summary
- Abstract
- Description
- Claims
- Application Information
AI Technical Summary
Problems solved by technology
Method used
Image
Examples
Embodiment 1
[0033] A special anti-corrosion coating for transmission towers: primer formula: 58 parts of epoxy resin, 12 parts of n-butyl titanate, 8 parts of chromium acetylacetonate, 12 parts of polyvinyl formal, and 70 parts of zinc powder;
[0034] The preparation method is as follows:
[0035] (1) Add 240 parts of n-butanol to chromium acetylacetonate, then add n-butyl titanate dropwise under stirring, add 0.065 part of mercaptopropyl triethoxysilane after the dropwise addition, stir evenly, and add to the reaction kettle , firstly heated to 70-80°C at a heating rate of 1°C / min, and then heated to 110-120°C at a heating rate of 5°C / min, holding the reaction for 12h
[0036] , and the reaction mixture is obtained after the end of the reaction;
[0037] (2) Heat the epoxy resin to 100-120°C, then slowly add the above mixture, and keep stirring for 2 hours to obtain the modified epoxy resin;
[0038] (3) Mix the modified epoxy resin, polybutene pure formal, zinc powder and mixed solut...
Embodiment 2
[0044] A special anti-corrosion coating for power transmission towers: primer formula: 50 parts of epoxy resin, 11 parts of n-butyl titanate, 5 parts of chromium acetylacetonate, 12-15 parts of polyvinyl formal, and 75 parts of zinc powder;
[0045] The preparation method is as follows:
[0046] (1) Add 220 parts of n-butanol to chromium acetylacetonate, then add n-butyl titanate dropwise under stirring, add 0.059 parts of mercaptopropyl triethoxysilane after the dropwise addition, stir evenly, and add to the reaction kettle , firstly, the temperature was raised to 70-80°C at a heating rate of 1°C / min, then to 110-120°C at a heating rate of 5°C / min, and the reaction was kept for 12 hours, and a mixed solution was obtained after the reaction;
[0047] (2) Heat the epoxy resin to 100-120°C, then slowly add the above mixture, and keep stirring for 2 hours to obtain the modified epoxy resin;
[0048] (3) Mix the modified epoxy resin, polybutene pure formal, zinc powder and mixed so...
Embodiment 3
[0052] A special anti-corrosion coating for power transmission towers: primer formula: 60 parts of epoxy resin, 15 parts of n-butyl titanate, 8 parts of chromium acetylacetonate, 12-15 parts of polyvinyl formal, and 80 parts of zinc powder;
[0053] The preparation method is as follows:
[0054] (1) Add 300 parts of n-butanol to chromium acetylacetonate, then add n-butyl titanate dropwise under stirring, add 0.081 part of mercaptopropyl triethoxysilane after the dropwise addition, stir evenly, and add to the reaction kettle , first heat up to 70-80°C at a heating rate of 1°C / min, then heat up to 110-120°C at a heating rate of 5°C / min, and keep the reaction for 12h,
[0055] After the reaction finishes, a mixed solution is obtained;
[0056] (2) Heat the epoxy resin to 100-120°C, then slowly add the above mixture, and keep stirring for 2 hours to obtain the modified epoxy resin;
[0057] (3) Mix the modified epoxy resin, polybutene pure formal, zinc powder and mixed solution ...
PUM
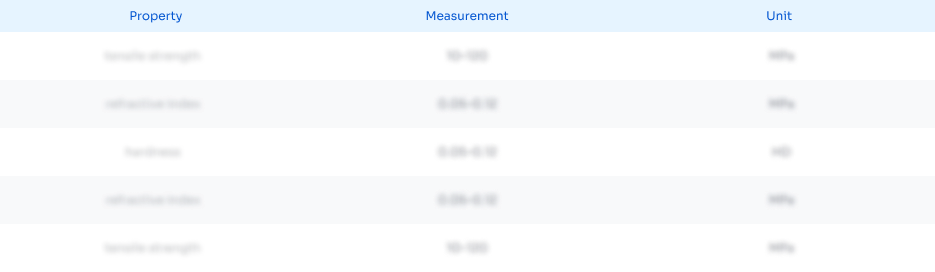
Abstract
Description
Claims
Application Information

- R&D Engineer
- R&D Manager
- IP Professional
- Industry Leading Data Capabilities
- Powerful AI technology
- Patent DNA Extraction
Browse by: Latest US Patents, China's latest patents, Technical Efficacy Thesaurus, Application Domain, Technology Topic, Popular Technical Reports.
© 2024 PatSnap. All rights reserved.Legal|Privacy policy|Modern Slavery Act Transparency Statement|Sitemap|About US| Contact US: help@patsnap.com