Wear-resistant fireproof abrasive brushing wire and preparation method thereof
A technology of abrasive brushes and abrasives, which is applied in the manufacture of fire-resistant and flame-retardant filaments, rayon, and brushes. It can solve the problems of low tensile strength of abrasive brush wires, rough friction on the working material surface, and poor wear resistance of 610. , to achieve the effect of good molding process, high processing precision and long service life
- Summary
- Abstract
- Description
- Claims
- Application Information
AI Technical Summary
Problems solved by technology
Method used
Examples
Embodiment 1
[0021] Embodiment 1: A wear-resistant and fire-resistant abrasive brush filament, comprising the following components in terms of mass percentage: base material: nylon 625-35 parts, nylon 101015-19 parts, nylon MXD6-13 parts, glass fiber 2- 3 parts, 1.5-3.8 parts of carbon fiber and 8-19 parts of polyethylene resin;
[0022] Abrasives: 3-5 parts of ceramic particles and 5-8 parts of diamond;
[0023] Additives: 1-2.5 parts of anti-wear agent, 2-3.5 parts of wetting agent, 0.8-1.5 parts of anti-aging agent, 1-2 parts of halogen-free flame retardant, 0.1-0.3 parts of catalyst, 1.5-3 parts of temperature-resistant agent And ethanol 0.1-0.5 parts.
[0024] Further, the following components are included: base material: 635 parts of nylon, 101015 parts of nylon, 10 parts of nylon MXD, 2 parts of glass fiber, 3 parts of carbon fiber and 15 parts of polyethylene resin;
[0025] Abrasives: 3 parts of ceramic particles and 8 parts of diamond;
[0026] Additives: 2 parts of antiwear a...
Embodiment 2
[0035] Embodiment 2: A wear-resistant and fire-resistant abrasive brush filament, which includes the following components in terms of mass percentage: base material: nylon 625-35 parts, nylon 101015-19 parts, nylon MXD6-13 parts, glass fiber 2- 3 parts, 1.5-3.8 parts of carbon fiber and 8-19 parts of polyethylene resin;
[0036] Abrasives: 3-5 parts of ceramic particles and 5-8 parts of diamond;
[0037] Additives: 1-2.5 parts of anti-wear agent, 2-3.5 parts of wetting agent, 0.8-1.5 parts of anti-aging agent, 1-2 parts of halogen-free flame retardant, 0.1-0.3 parts of catalyst, 1.5-3 parts of temperature-resistant agent And ethanol 0.1-0.5 parts.
[0038] Further, the content of the following components is included: base material: 631 parts of nylon, 101019 parts of nylon, 10 parts of nylon MXD, 2 parts of glass fiber, 3 parts of carbon fiber and 15 parts of polyethylene resin;
[0039] Abrasives: 3 parts of ceramic particles and 8 parts of diamond;
[0040] Additives: 1.6...
Embodiment 3
[0042] Embodiment 3: A wear-resistant and fire-resistant abrasive brush filament, which includes the following components in terms of mass percentage: base material: nylon 625-35 parts, nylon 101015-19 parts, nylon MXD6-13 parts, glass fiber 2- 3 parts, 1.5-3.8 parts of carbon fiber and 8-19 parts of polyethylene resin;
[0043] Abrasives: 3-5 parts of ceramic particles and 5-8 parts of diamond;
[0044] Additives: 1-2.5 parts of anti-wear agent, 2-3.5 parts of wetting agent, 0.8-1.5 parts of anti-aging agent, 1-2 parts of halogen-free flame retardant, 0.1-0.3 parts of catalyst, 1.5-3 parts of temperature-resistant agent And ethanol 0.1-0.5 parts.
[0045] Further, the following components are included: base material: 635 parts of nylon, 101019 parts of nylon, 6 parts of nylon MXD, 3 parts of glass fiber, 2 parts of carbon fiber and 15 parts of polyethylene resin;
[0046] Abrasives: 3 parts of ceramic particles and 8 parts of diamond;
[0047] Additives: 1.5 parts of antiwea...
PUM
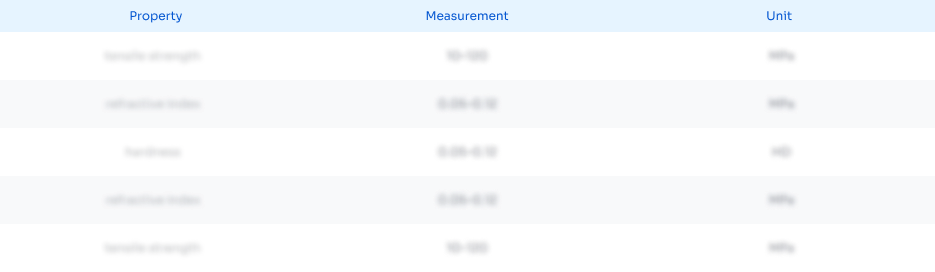
Abstract
Description
Claims
Application Information

- R&D
- Intellectual Property
- Life Sciences
- Materials
- Tech Scout
- Unparalleled Data Quality
- Higher Quality Content
- 60% Fewer Hallucinations
Browse by: Latest US Patents, China's latest patents, Technical Efficacy Thesaurus, Application Domain, Technology Topic, Popular Technical Reports.
© 2025 PatSnap. All rights reserved.Legal|Privacy policy|Modern Slavery Act Transparency Statement|Sitemap|About US| Contact US: help@patsnap.com