Fluorine and silicon-containing polyurethane material with high biostability and preparation method thereof
A polyurethane material and bio-stability technology, which is applied in the field of fluorine-containing silicon-containing polyurethane materials and their preparation, can solve the problems that the bio-stability and mechanical properties cannot be improved at the same time, the mechanical properties of polyurethane are reduced, and the preparation cost is expensive, so as to improve the body and surface properties, the effect of improving biological stability
- Summary
- Abstract
- Description
- Claims
- Application Information
AI Technical Summary
Problems solved by technology
Method used
Image
Examples
Embodiment 1
[0036] The first step, the preparation of fluorosilicone polyether polyurethane prepolymer, add 90g of polytetrahydrofuran ether diol and 22g of hydroxyalkyl-terminated polydimethylsiloxane into a three-necked bottle with mechanical stirring at 100-105°C Vacuum dehydration for 2 hours until the water content in the raw material is less than 0.01%; then blow in N 2And cool down to 60-65°C, add 3.06g FDO (fluorine-containing dihydric alcohol), stir evenly and continue to cool down to 40-42°C, add 51g of molten completely transparent liquid MDI (methylene diphenyl diisocyanate) and 0.1% organic bismuth catalyst, stir rapidly until the temperature rises to 68-70°C, and maintain the temperature for 50 minutes until the NCO (isocyanate group) content reaches the designed theoretical value, that is, the fluorosilicon polyether polyurethane prepolymer is obtained.
[0037] The second step is the post-chain extension reaction. Cool the prepolymer prepared in the first step to 58-60°C, ...
Embodiment 2
[0040] The first step, the preparation of fluorosilicon polyether polyurethane prepolymer, add 0.095mol polyhexamethylene ether glycol and 0.005mol hydroxyethoxyl hydrocarbon group-terminated polydimethylsiloxane into three Vacuum dehydrate the bottle at 100-105°C for 2 hours until the water content in the raw material is less than 0.01%; then blow N 2 And lower the temperature to 60-65°C, add 0.01molHEPFOA (N-(1,1-Dihydroxymethylethyl) perfluorooctylamide, see patent: fluorine-containing diol CN1435410A), stir well and continue to cool down to 40- 42°C, add 0.25mol HDI (hexamethylene 1,6-diisocyanate) and 0.05% stannous octoate, stir rapidly until the temperature rises to 75-80°C, and maintain the reaction at this temperature for 50min until the NCO content reaches Design the theoretical value to obtain the fluorosilicone polyether polyurethane prepolymer.
[0041] The second step is the post-chain extension reaction. Cool the prepolymer prepared in the first step to 58-60 °...
Embodiment 3
[0044] The first step, the preparation of fluorosilicone polycarbonate polyurethane prepolymer, add 0.005mol poly 1,6-hexyl carbonate diol and 0.095mol hydroxyalkyl terminated polydimethylsiloxane into three Vacuum dehydrate the bottle at 100-105°C for 2 hours until the water content in the raw material is less than 0.01%; then blow N 2 And cool down to 60-65°C, add 0.001mol FDO, stir evenly and continue to cool down to 40-42°C, add 0.204mol molten and completely transparent liquid MDI and 0.1% organic bismuth, stir rapidly until the temperature rises to 50-55°C , and maintain the temperature at this temperature for 50 minutes until the NCO content reaches the design theoretical value, that is, the fluorosilicon polycarbonate polyurethane prepolymer is obtained.
[0045] The second step is the post-chain extension reaction. Add 0.099mol BDO to the prepolymer prepared in the first step, stir evenly at a high speed and raise the temperature to about 100°C. When the viscosity of ...
PUM
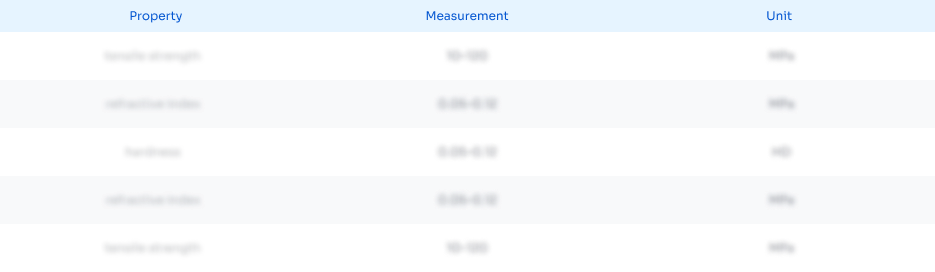
Abstract
Description
Claims
Application Information

- R&D Engineer
- R&D Manager
- IP Professional
- Industry Leading Data Capabilities
- Powerful AI technology
- Patent DNA Extraction
Browse by: Latest US Patents, China's latest patents, Technical Efficacy Thesaurus, Application Domain, Technology Topic, Popular Technical Reports.
© 2024 PatSnap. All rights reserved.Legal|Privacy policy|Modern Slavery Act Transparency Statement|Sitemap|About US| Contact US: help@patsnap.com