Cavity type bulk acoustic wave resonator without preparing sacrificial layer and preparation method of cavity type bulk acoustic wave resonator
A bulk acoustic wave resonator and sacrificial layer technology, applied in electrical components, impedance networks, etc., can solve the problems of cavity corrosion residues and low film quality, and achieve the effects of high yield, less damage, and reduced clutter.
- Summary
- Abstract
- Description
- Claims
- Application Information
AI Technical Summary
Problems solved by technology
Method used
Image
Examples
Embodiment 1
[0055] The method for preparing a cavity-type BAW resonator without preparing a sacrificial layer in this embodiment includes the following steps:
[0056] (a) Take a piezoelectric single crystal wafer, the piezoelectric single crystal wafer is a lithium tantalate wafer, perform ion implantation on the piezoelectric single crystal wafer to form an ion damage layer, and the implanted ions are H ions , the energy of implanted ions is 195KeV, and the implantation dose is 6×10 16 / cm 2 , the ion beam current is 1μm / cm- 2 , the implantation depth is 6 μm to obtain a pyroelectric material, and then photolithography forms a pattern to be grown on the injection surface of the obtained pyroelectric material, and then utilizes magnetron sputtering to grow electrodes, the electrode material is Au, and finally passes through acetone Wash off the excess part to obtain a piezoelectric single crystal wafer with ion implantation and a bottom electrode, the thickness of the bottom electrode ...
Embodiment 2
[0070] The method for preparing a cavity-type BAW resonator without preparing a sacrificial layer in this embodiment includes the following steps:
[0071] (a) Take a piezoelectric single crystal wafer, the piezoelectric single crystal wafer is a lithium tantalate wafer, perform ion implantation on the piezoelectric single crystal wafer, the implanted ions are As ions, the energy of the implanted ions It is 150KeV-1000KeV; the implantation depth is 0.5-1.8μm to obtain a pyroelectric material, and then grow an electrode on the injection surface of the obtained pyroelectric material by magnetron sputtering, the electrode material is Au, and then prepare a mask , and finally etch off the excess part to obtain a piezoelectric single crystal wafer that has undergone ion implantation and has a bottom electrode, and the thickness of the bottom electrode is 100 nm;
[0072] (b) Take the piezoelectric single crystal wafer having the bottom electrode through ion implantation, and form a...
Embodiment 3
[0077] The preparation method of the cavity-type bulk acoustic wave resonator in this embodiment without preparing a sacrificial layer is prepared by the same method as that of Embodiment 1, except that the upper surface area of the bottom electrode is larger than the upper surface area of the cavity.
[0078] Such as Figure 8 Shown is a structural schematic diagram of the ion-implanted piezoelectric single crystal wafer obtained in step (b) and having a bottom electrode.
[0079] Figure 9 It is a schematic structural diagram of the piezoelectric single crystal wafer described in step (c) of the method for preparing a cavity-type bulk acoustic resonator without preparing a sacrificial layer in Example 3 of the present invention after growing a supporting layer;
[0080] Figure 10 It is a schematic structural diagram of a cavity-type bulk acoustic resonator that does not need to prepare a sacrificial layer in step (d) of the method for preparing a cavity-type bulk acou...
PUM
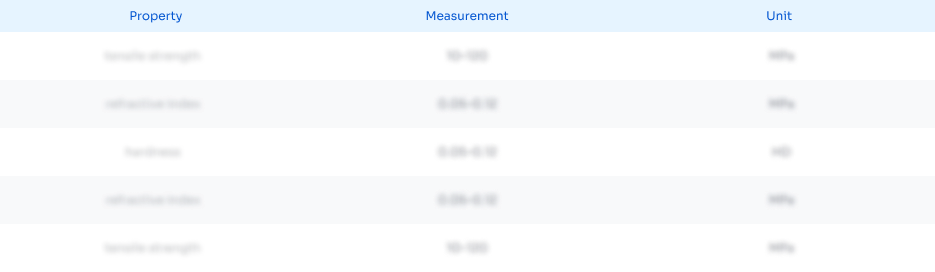
Abstract
Description
Claims
Application Information

- R&D
- Intellectual Property
- Life Sciences
- Materials
- Tech Scout
- Unparalleled Data Quality
- Higher Quality Content
- 60% Fewer Hallucinations
Browse by: Latest US Patents, China's latest patents, Technical Efficacy Thesaurus, Application Domain, Technology Topic, Popular Technical Reports.
© 2025 PatSnap. All rights reserved.Legal|Privacy policy|Modern Slavery Act Transparency Statement|Sitemap|About US| Contact US: help@patsnap.com