Technology for hot-dip galvanizing of steel tube
A technology of hot-dip galvanizing and steel pipe, applied in hot-dip plating process, metal material coating process, coating and other directions, can solve the problems of easy chromatic aberration on the surface of the workpiece, high qualification rate of the workpiece, and difficulty in meeting the thickness of the zinc layer. Improve corrosion resistance, uniform galvanized surface, and meet the needs of galvanizing
- Summary
- Abstract
- Description
- Claims
- Application Information
AI Technical Summary
Problems solved by technology
Method used
Examples
Embodiment 1
[0025] A process for hot-dip galvanizing of steel pipes, comprising the following steps:
[0026] (1) Degreasing: soak the steel pipe in the degreasing solution for 30-40 minutes, then rinse with water; the degreasing solution includes the following raw materials in parts by weight: 1 part of activated carbon, 1 part of rock wool, 6 parts of fruit acid, ethylene glycol 15 parts of distearate, 20 parts of phospholipids, 20 parts of fatty acid glycerides and 10 parts of acrylic resin. The degreasing liquid is obtained through the following steps: acrylic resin is placed in ultrasound, phospholipids, fatty acid glycerides and activated carbon are added in sequence, the ultrasound is turned off, fruit acid is added after full stirring, and then ethylene glycol distearate and Rock wool, fully stirred to obtain degreasing liquid;
[0027] (2) Pickling: The degreased steel pipes are pickled with hydrochloric acid solutions with hydrochloric acid mass fractions of 30%, 22% and 15%, r...
Embodiment 2
[0031] A process for hot-dip galvanizing of steel pipes, comprising the following steps:
[0032] (1) Degreasing: soak the steel pipe in the degreasing solution for 30-40 minutes, then rinse with water; the degreasing solution includes the following raw materials in parts by weight: 3 parts of activated carbon, 3 parts of rock wool, 2 parts of fruit acid, ethylene glycol 20 parts of distearate, 15 parts of phospholipid, 15 parts of fatty acid glyceride and 15 parts of acrylic resin. The degreasing liquid is obtained through the following steps: acrylic resin is placed in ultrasound, phospholipids, fatty acid glycerides and activated carbon are added in sequence, the ultrasound is turned off, fruit acid is added after full stirring, and then ethylene glycol distearate and Rock wool, fully stirred to obtain degreasing liquid;
[0033] (2) Pickling: The degreased steel pipes are pickled with hydrochloric acid solutions with hydrochloric acid mass fractions of 28%, 19% and 10%, r...
Embodiment 3
[0037] A process for hot-dip galvanizing of steel pipes, comprising the following steps:
[0038] (1) Degreasing: soak the steel pipe in the degreasing solution for 30-40 minutes, then rinse with water; the degreasing solution includes the following raw materials in parts by weight: 2 parts of activated carbon, 2 parts of rock wool, 4 parts of fruit acid, ethylene glycol 18 parts of distearate, 16 parts of phospholipid, 16 parts of fatty acid glyceride and 12 parts of acrylic resin. The degreasing liquid is obtained through the following steps: acrylic resin is placed in ultrasound, phospholipids, fatty acid glycerides and activated carbon are added in sequence, the ultrasound is turned off, fruit acid is added after full stirring, and then ethylene glycol distearate and Rock wool, fully stirred to obtain degreasing liquid;
[0039] (2) Pickling: The degreased steel pipes are pickled with hydrochloric acid solutions with hydrochloric acid mass fractions of 30%, 20% and 10%, r...
PUM
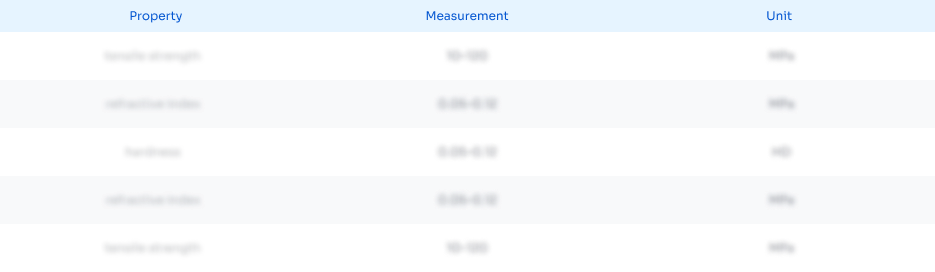
Abstract
Description
Claims
Application Information

- R&D
- Intellectual Property
- Life Sciences
- Materials
- Tech Scout
- Unparalleled Data Quality
- Higher Quality Content
- 60% Fewer Hallucinations
Browse by: Latest US Patents, China's latest patents, Technical Efficacy Thesaurus, Application Domain, Technology Topic, Popular Technical Reports.
© 2025 PatSnap. All rights reserved.Legal|Privacy policy|Modern Slavery Act Transparency Statement|Sitemap|About US| Contact US: help@patsnap.com