Catalyst for selective oxidation of methacrolein to methacrylic acid, preparation method and use thereof
A technology of methacrylic acid and methacrolein, which is used in catalyst activation/preparation, organic compound preparation, physical/chemical process catalysts, etc., can solve the problems of high separation cost, many by-products, and high production cost, and can improve Preparation efficiency, high activity, and the effect of improving activity
- Summary
- Abstract
- Description
- Claims
- Application Information
AI Technical Summary
Problems solved by technology
Method used
Image
Examples
Embodiment 1
[0059] The preparation method of catalyst comprises the following steps:
[0060] (1) Add 2643.5g of molybdenum oxide and 167.1g of vanadium oxide into 31kg of deionized water, dilute 233g of phosphoric acid (concentration is 85%) into phosphoric acid with a concentration of 15%, and slowly add the phosphoric acid solution to the solution containing molybdenum oxide In the solution of vanadium oxide and vanadium oxide, after the phosphoric acid is added, the temperature is raised to 100°C, and the stirring reaction is continued for 6 hours to obtain the first solution;
[0061] (2) Add 12.5 g of ammonium carbonate to the first solution, stir and react at 25° C. for 1 h to obtain the second solution, and then spray dry to obtain the first solid;
[0062] (3) Mix the first solid, 333.2g cesium nitrate, 4.9g sodium nitrate, 42.5g copper nitrate, 28.7g bismuth nitrate, 23.3g zirconia and 29.3g ammonium carbonate to obtain the second solid;
[0063] (4) adding the second solid int...
Embodiment 2
[0065] The difference between this embodiment and embodiment 1 is that the roasting atmosphere of step (4) is replaced by the mixed gas of air and nitrogen by air, and the concentration of oxygen in the described mixed gas is 13%, and other conditions are compared with embodiment 1 completely. same.
Embodiment 3
[0067] The difference between this embodiment and embodiment 1 is that the roasting atmosphere of step (4) is replaced by the mixed gas of air and nitrogen by air, and the concentration of oxygen in the described mixed gas is 5%, and other conditions are compared with embodiment 1 completely. same.
PUM
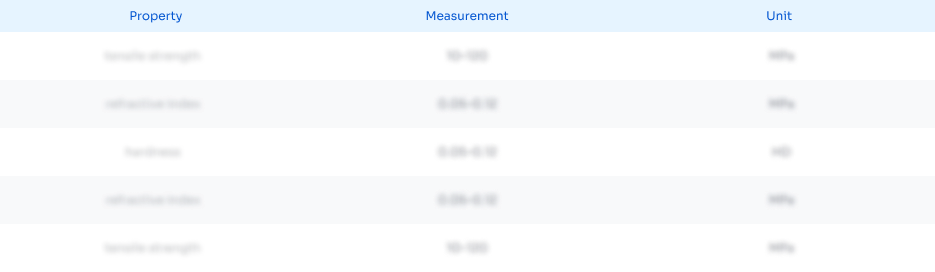
Abstract
Description
Claims
Application Information

- R&D Engineer
- R&D Manager
- IP Professional
- Industry Leading Data Capabilities
- Powerful AI technology
- Patent DNA Extraction
Browse by: Latest US Patents, China's latest patents, Technical Efficacy Thesaurus, Application Domain, Technology Topic, Popular Technical Reports.
© 2024 PatSnap. All rights reserved.Legal|Privacy policy|Modern Slavery Act Transparency Statement|Sitemap|About US| Contact US: help@patsnap.com