Preparation methods for copper calcium titanate based ceramic material and ceramic capacitor with giant dielectric constant
A copper-calcium titanate-based, ceramic capacitor technology is applied in the field of dielectric ceramic materials and giant dielectric ceramic dielectric capacitor technology development, which can solve the problems of complex process, fail to improve the overall performance of CCTO materials, etc. Short laser action time and good compactness
- Summary
- Abstract
- Description
- Claims
- Application Information
AI Technical Summary
Problems solved by technology
Method used
Image
Examples
Embodiment 1
[0037] Copper oxide (CuO), calcium oxide (CaO), titanium oxide (TiO 2 ), copper powder as raw material, according to Cu:CuO:CaO:TiO 2 = 2:1:1:4 ratio (molar ratio), high-energy ball milling with absolute ethanol as the ball milling medium, then drying, grinding evenly, adding PVA binder with a mass fraction of 5% for granulation and compaction , in a muffle furnace at 550°C for debonding, the heating rate is controlled at 1°C / min, the holding time is 10 hours, and the laser sintering is carried out by adjusting the appropriate laser power. The laser wavelength is 980nm, the laser power is 80W, and the spot diameter is 12mm. It is advisable to cover the molded sample, and the sintering time is 5s. Finally, a large dielectric constant CCTO ceramic dielectric material with fine particles and better compactness is obtained, and its dielectric constant can reach 10 4 As mentioned above, the obtained CCTO-based ceramic material is ground and polished to form a specific shape whose...
Embodiment 2
[0039] Copper oxide (CuO), calcium oxide (CaO), titanium oxide (TiO 2 ) as raw material, according to CuO:CaO:TiO 2 =3:1:4 proportioning (molar ratio), carry out high-energy ball milling with absolute ethanol as the ball milling medium, then dry, grind evenly, add the PVA binder that mass fraction is 7% to carry out granulation, compaction, adopt Laser irradiation is used for debonding, the laser power is 10W, the irradiation time is 30min, and then the appropriate laser power is adjusted for laser sintering. The laser wavelength is 980nm, the laser power is 80W, and the spot diameter is 12mm, which is suitable for covering the molded sample , the sintering time is 5s. Finally, a large dielectric constant CCTO ceramic dielectric material with fine particles and better compactness is obtained, and its dielectric constant can reach 10 4 As mentioned above, the obtained CCTO-based ceramic material is ground and polished to form a specific shape whose upper and lower sides are p...
Embodiment 3
[0041] Copper oxide (CuO), calcium oxide (CaO), titanium oxide (TiO 2 ), copper powder as raw material, according to Cu:CuO:CaO:TiO2 = 2:1:1:4 ratio (molar ratio), high-energy ball milling with absolute ethanol as the ball milling medium, then drying, grinding evenly, adding PVA binder with a mass fraction of 8% for granulation and compaction , in a muffle furnace at 550°C for debonding, the heating rate is controlled at 1°C / min, the holding time is 12 hours, and the laser sintering is carried out by adjusting the appropriate laser power. The laser wavelength is 980nm, the laser power is 90W, and the spot diameter is 12mm. It is advisable to cover the molded sample, and the sintering time is 5s. Finally, a large dielectric constant CCTO ceramic dielectric material with fine particles and better compactness is obtained, and its dielectric constant can reach 10 4 As mentioned above, the obtained CCTO-based ceramic material is ground and polished to form a specific shape with th...
PUM
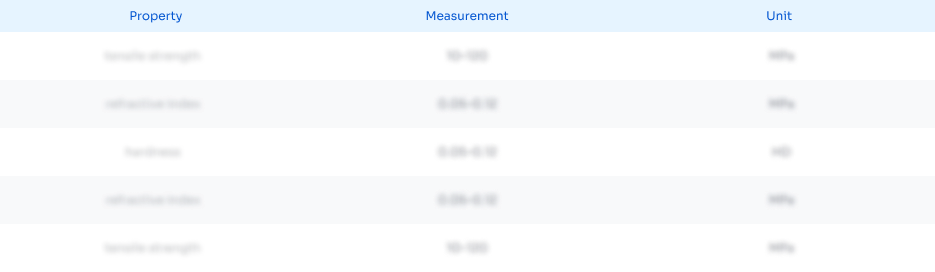
Abstract
Description
Claims
Application Information

- R&D
- Intellectual Property
- Life Sciences
- Materials
- Tech Scout
- Unparalleled Data Quality
- Higher Quality Content
- 60% Fewer Hallucinations
Browse by: Latest US Patents, China's latest patents, Technical Efficacy Thesaurus, Application Domain, Technology Topic, Popular Technical Reports.
© 2025 PatSnap. All rights reserved.Legal|Privacy policy|Modern Slavery Act Transparency Statement|Sitemap|About US| Contact US: help@patsnap.com