Device and method for jointly treating antimony-smelting arsenic soda slag through pyrogenic process and wet process
A combined treatment and arsenic-alkali slag technology, applied in the direction of improving process efficiency, can solve the problems of low content, high difficulty, large amount of calcium arsenate slag, etc., and achieve the effects of simple device structure, simple control and strong processing capacity.
- Summary
- Abstract
- Description
- Claims
- Application Information
AI Technical Summary
Problems solved by technology
Method used
Image
Examples
Embodiment 1~3
[0059] like figure 1 As shown, the device includes a pretreatment unit, arsenic pyrolysis volatilization unit and wet deep arsenic removal unit; the pretreatment unit includes sequentially connected No. 1 jaw crusher 1-1, No. 1 Raymond mill 2- 1. Concrete mixer 3 and dough making machine 4; said arsenic fire method volatilization unit includes reverberatory furnace 5, soot settling chamber 6, surface cooling device 7, bag filter 8, water foam absorption tower 9 and ion adsorber connected in sequence 10. The wet deep arsenic removal unit includes sequentially connected No. 2 jaw crusher 1-2, No. 2 Raymond mill 2-2, leaching reaction tank 11, stainless steel centrifuge 12, deep arsenic removal reaction tank 13, Box-type filter press 14; the group making machine 4 in the pretreatment unit is connected with the reverberatory furnace 5 feed port 5-1 in the arsenic fire method volatilization unit; the reverberatory furnace 5 in the arsenic fire method volatilization unit is discharg...
Embodiment 1
[0062] (1) Pretreatment: first put 50.0kg of antimony, arsenic and alkali slag 1 into No. 1 jaw crusher 1-1 and crush it to a particle size ≤ 30mm, and then use No. 1 Raymond mill 2-1 to finely grind it to pass 250 mesh Sieve, put the finely ground powder and 10.0kg of arsenic volatile agent (a mixture of 3.3kg of carbon and 6.7kg of silicon dioxide) into the concrete mixer 3 for mixing, and then put the mixture into the dough making machine 4 to compact the dough until the diameter is 20mm agglomerate, get 60.0kg arsenic-alkali slag agglomerate;
[0063] (2) Arsenic fire method volatilization: Mix 60.0kg of arsenic-alkali slag agglomerates obtained in step (1) and 12.0kg of pulverized coal into the reverberatory furnace 5, heat and volatilize at 900°C for 40 minutes, and collect the material from the reverberatory furnace 5 outlet 33.1kg of alkali slag discharged from 5-3 (mass percentage of main components: As 0.56%, Sb 0.05%, Na 2 O 62.85%) and the 4.0kg antimony-containin...
Embodiment 2
[0067] (1) Pretreatment: first put 1000.0kg of antimony, arsenic and alkali slag 2 into No. 1 jaw crusher 1-1 and crush it to a particle size ≤ 25mm, and then use No. 1 Raymond mill 2-1 to finely grind it to pass 300 mesh Sieve, put the finely ground powder and 250.0kg of arsenic volatile agent (a mixture of 62.5kg of carbon and 187.5kg of silicon dioxide) into the concrete mixer 3 for mixing, and then put the mixture into the dough making machine 4 to compact the dough until the diameter is 30mm agglomerates, 1250.0kg arsenic-alkali slag agglomerates;
[0068] (2) Arsenic fire method volatilization: mix 1250.0kg of arsenic-alkali slag agglomerates obtained in step (1) and 320.0kg of pulverized coal into the reverberatory furnace 5, heat and volatilize at 1100°C for 80 minutes, and collect the material from the reverberatory furnace 5 outlet 575.1kg of alkali slag discharged from 5-3 (mass percentage of main components: As 0.52%, Sb 0.04%, Na 2 O 83.35%) and 260.0kg of antimo...
PUM
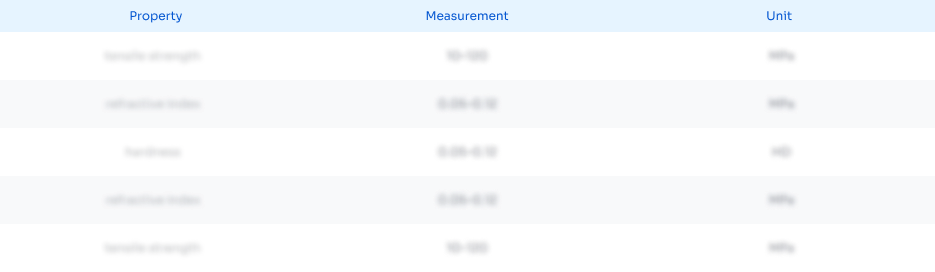
Abstract
Description
Claims
Application Information

- R&D
- Intellectual Property
- Life Sciences
- Materials
- Tech Scout
- Unparalleled Data Quality
- Higher Quality Content
- 60% Fewer Hallucinations
Browse by: Latest US Patents, China's latest patents, Technical Efficacy Thesaurus, Application Domain, Technology Topic, Popular Technical Reports.
© 2025 PatSnap. All rights reserved.Legal|Privacy policy|Modern Slavery Act Transparency Statement|Sitemap|About US| Contact US: help@patsnap.com