Copper slag resource treatment method in nickel refining system
A treatment method and nickel refining technology, which is applied in the field of copper slag resource treatment in nickel refining system, can solve the problems of high treatment cost, increased treatment cost, high power consumption, etc., to reduce purification treatment cost, eliminate pollution problems, and shorten the process flow Effect
- Summary
- Abstract
- Description
- Claims
- Application Information
AI Technical Summary
Problems solved by technology
Method used
Image
Examples
Embodiment 1
[0039] Weigh 1kg of copper slag from the nickel refining system to wash it with water, and the washed liquid is incorporated into the nickel refining system. The conditions for cleaning the copper slag with water are: the liquid-solid mass ratio of water to copper slag is 2:1, normal temperature cleaning, and stirring time 1.5h, stirring speed is 150r / min; after cleaning, adopt vacuum filtration to carry out liquid-solid separation, filter residue is dried, adopt flame atomic absorption spectrometry to detect the mass percentage content of chlorine element from 9.8% before cleaning to 4.8% after washing. The copper slag washed with water is leached with normal pressure air, and the air flow rate is 4Nm 3 / h, add 5g / L Cu for the first leaching 2+ , Subsequent use of pressurized oxygen leaching leaching solution for pulping and then normal pressure air leaching, the leaching solution after normal pressure air leaching is incorporated into the nickel refining system, the conditi...
PUM
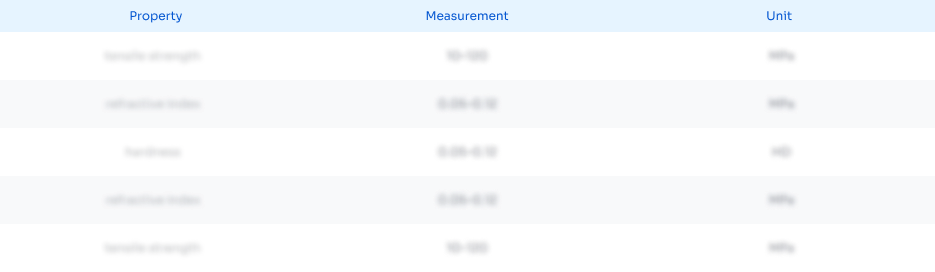
Abstract
Description
Claims
Application Information

- R&D
- Intellectual Property
- Life Sciences
- Materials
- Tech Scout
- Unparalleled Data Quality
- Higher Quality Content
- 60% Fewer Hallucinations
Browse by: Latest US Patents, China's latest patents, Technical Efficacy Thesaurus, Application Domain, Technology Topic, Popular Technical Reports.
© 2025 PatSnap. All rights reserved.Legal|Privacy policy|Modern Slavery Act Transparency Statement|Sitemap|About US| Contact US: help@patsnap.com