A kind of method for preparing high coercive force samarium iron nitrogen magnet from nitrogen rare earth complex
A technology of rare earth complexes and high coercive force, applied in the fields of magnetic objects, magnetic materials, inductors/transformers/magnets, etc., can solve the problems of difficult industrial production, grain growth, and low efficiency, and achieve the goal of improving nitrogen effect, enhance the effect of magnetocrystalline anisotropy
- Summary
- Abstract
- Description
- Claims
- Application Information
AI Technical Summary
Problems solved by technology
Method used
Examples
Embodiment 1
[0016] 1) Sm and Fe alloys with a purity of 99.99% or more, according to the nominal composition of the alloy Sm 2 Fe 17 Weigh the raw materials of each element and carry out vacuum melting. The alloy is repeatedly smelted 5 times to obtain a master alloy ingot with uniform composition, and then made into a thin strip in a rapid quenching furnace. The cavity pressure of the rapid quenching furnace is 0.05MPa. is 0.09MPa, and the linear speed of the roller is 35m / s;
[0017] 2) Sm prepared in step (1) 2 Fe 17 The thin strip is subjected to crystallization heat treatment at 650°C under the protection of argon to obtain the corresponding nanocrystalline alloy;
[0018] 3) Sm prepared in step (2) 2 Fe 17 Nanocrystalline thin ribbons in high-purity N 2 Nitriding treatment was carried out in the air, the nitriding temperature was 450°C, and the nitriding time was 8 hours to obtain Sm 2 Fe 17 N x nanocrystalline alloys;
[0019] 4) Sm prepared in step (3) 2 Fe 17 N x Nan...
Embodiment 2
[0024] 1) Sm and Fe alloys with a purity of 99.99% or more, according to the nominal composition of the alloy Sm 2 Fe 17 Weigh the raw materials of each element and carry out vacuum melting. The alloy is repeatedly smelted 5 times to obtain a master alloy ingot with uniform composition, and then made into a thin strip in a rapid quenching furnace. The cavity pressure of the rapid quenching furnace is 0.05MPa. is 0.09MPa, and the linear speed of the roller is 40m / s;
[0025] 2) Sm prepared in step (1) 2 Fe 17 The thin strip is subjected to crystallization heat treatment at 700°C under the protection of argon to obtain the corresponding nanocrystalline alloy;
[0026] 3) Sm prepared in step (2) 2 Fe 17 Nanocrystalline thin ribbons in high-purity N 2 Nitriding treatment was carried out in the air, the nitriding temperature was 450°C, and the nitriding time was 10 hours to obtain Sm 2 Fe 17 N x nanocrystalline alloys;
[0027] 4) Sm prepared in step (3) 2 Fe 17 N x Na...
Embodiment 3
[0032] 1) Sm and Fe alloys with a purity of 99.99% or more, according to the nominal composition of the alloy Sm 2 Fe 17 Weigh the raw materials of each element and carry out vacuum melting. The alloy is repeatedly smelted 5 times to obtain a master alloy ingot with uniform composition, and then made into a thin strip in a rapid quenching furnace. The cavity pressure of the rapid quenching furnace is 0.05MPa. is 0.09MPa, and the linear speed of the roller is 45m / s;
[0033] 2) Sm prepared in step (1) 2 Fe 17 The thin ribbon is subjected to crystallization heat treatment at 750°C under the protection of argon to obtain the corresponding nanocrystalline alloy;
[0034] 3) Sm prepared in step (2) 2 Fe 17 Nanocrystalline ribbons in high-purity NH 3 Nitriding treatment was carried out in the air, the nitriding temperature was 500°C, and the nitriding time was 10 hours to obtain Sm 2 Fe 17 N x nanocrystalline alloys;
[0035] 4) Sm prepared in step (3) 2 Fe 17 N x Nanoc...
PUM
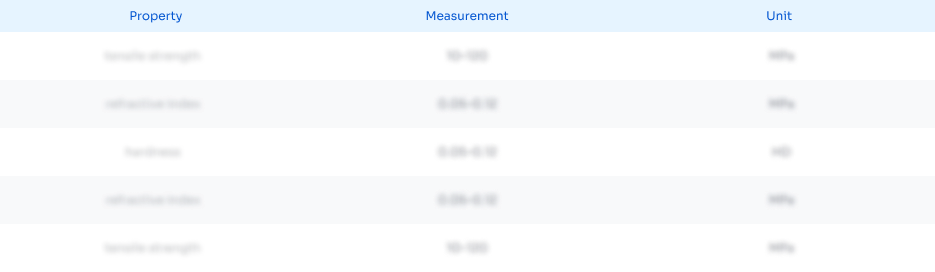
Abstract
Description
Claims
Application Information

- R&D
- Intellectual Property
- Life Sciences
- Materials
- Tech Scout
- Unparalleled Data Quality
- Higher Quality Content
- 60% Fewer Hallucinations
Browse by: Latest US Patents, China's latest patents, Technical Efficacy Thesaurus, Application Domain, Technology Topic, Popular Technical Reports.
© 2025 PatSnap. All rights reserved.Legal|Privacy policy|Modern Slavery Act Transparency Statement|Sitemap|About US| Contact US: help@patsnap.com