Casting tundish composite dry material as well as preparation method thereof
A dry material and tundish technology, applied in the field of iron and steel metallurgy, can solve the problems of high cost of tundish working lining, high residual carbon content, and inability to meet the production needs of ultra-low carbon steel and clean steel, etc. The effect of simple production and process
- Summary
- Abstract
- Description
- Claims
- Application Information
AI Technical Summary
Problems solved by technology
Method used
Image
Examples
Embodiment 1
[0027] Casting tundish composite dry material, in parts by mass, includes the following components: 20 parts of forsterite, 5 parts of hydroxymethyl cellulose, 4 parts of industrial glucose, 3 parts of high alumina bauxite, 1 part of chromium oxide powder , 2 parts of sodium hexametaphosphate.
[0028] The preparation method of the smelting and casting tundish composite dry material comprises the following steps:
[0029] (1) Stir the above-mentioned raw materials uniformly in a blender to obtain a mixed material;
[0030] (2) Placing the mixed material in a mould, pounding and vibrating to form a molded green body;
[0031] (3) Put the mold and the forming body together in an oven at 260 degrees Celsius and bake for 0.5h, and demould after cooling to obtain a dry material intermediate;
[0032] (4) Heat the dry material intermediate at 1050 degrees Celsius and 1450 degrees Celsius for 1 hour in turn to obtain the online finished compound dry material for refining and castin...
Embodiment 2
[0034] Casting tundish composite dry material, in parts by mass, includes the following components: 30 parts of forsterite, 10 parts of hydroxymethyl cellulose, 7 parts of industrial glucose, 8 parts of high alumina bauxite, and 5 parts of chromium oxide powder , 4 parts of sodium hexametaphosphate.
[0035] The preparation method of the smelting and casting tundish composite dry material comprises the following steps:
[0036] (1) Stir the above-mentioned raw materials uniformly in a blender to obtain a mixed material;
[0037] (2) Placing the mixed material in a mould, pounding and vibrating to form a molded green body;
[0038] (3) put the mold and the forming body together in an oven at 330 degrees Celsius and bake for 0.6h, and demould after cooling to obtain a dry material intermediate;
[0039] (4) Heat the dry material intermediate at 1150 degrees Celsius and 1550 degrees Celsius for 3 hours in turn to obtain the online finished compound dry material for refining and...
Embodiment 3
[0041] Casting tundish composite dry material, in parts by mass, composite dry material includes the following components: 26 parts of forsterite, 8 parts of hydroxymethyl cellulose, 5 parts of industrial glucose, 5 parts of high alumina bauxite, oxidized 3 parts of chromium powder, 3 parts of sodium hexametaphosphate.
[0042] The preparation method of the smelting and casting tundish composite dry material comprises the following steps:
[0043] (1) Stir the above-mentioned raw materials uniformly in a blender to obtain a mixed material;
[0044] (2) Placing the mixed material in a mould, pounding and vibrating to form a molded green body;
[0045] (3) Put the mold and the formed body together in an oven at 280 degrees Celsius and bake for 0.7h, and demould after cooling to obtain a dry material intermediate;
[0046] (4) Heat the dry material intermediate at 1080 degrees Celsius and 1490 degrees Celsius for 2 hours in turn to obtain the online finished compound dry materi...
PUM
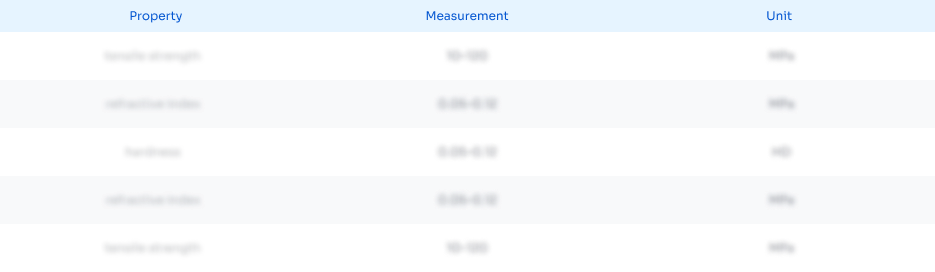
Abstract
Description
Claims
Application Information

- R&D Engineer
- R&D Manager
- IP Professional
- Industry Leading Data Capabilities
- Powerful AI technology
- Patent DNA Extraction
Browse by: Latest US Patents, China's latest patents, Technical Efficacy Thesaurus, Application Domain, Technology Topic, Popular Technical Reports.
© 2024 PatSnap. All rights reserved.Legal|Privacy policy|Modern Slavery Act Transparency Statement|Sitemap|About US| Contact US: help@patsnap.com