A metal ceramic preparing method
A cermet, high-temperature sintering technology, applied in the field of ceramics, can solve the problems of low tensile strength and flexural strength, achieve high flexural strength and tensile strength, simple production process, and overcome the effect of poor flexibility of ceramics
- Summary
- Abstract
- Description
- Claims
- Application Information
AI Technical Summary
Problems solved by technology
Method used
Examples
Embodiment 1
[0019] The preparation method of the cermet of the present invention comprises the following steps:
[0020] The raw materials weighed according to parts by weight are respectively sent into a ball mill for ball milling, the rotating speed of the ball mill is 300rpm, and the ball milling time is 4h;
[0021] Send into high-speed mixer and carry out high-speed mixing, and the rotating speed of high-speed mixer is 250rpm;
[0022] Send it into a high-temperature sintering furnace for vacuum high-temperature sintering, the temperature of high-temperature sintering is 800°C, and the sintering time is 4h;
[0023] Cooling made cermet.
[0024] Among them, the raw materials are: 55 parts of ceramic powder, 10 parts of cobalt oxide, 10 parts of aluminum carbide, 5 parts of magnesium silicate, 5 parts of siliconized cobalt, 5 parts of ferrochrome oxide, 5 parts of chromium dioxide, 1 part of manganese silicide, nitrogen 7 parts of silicon oxide, 20 parts of shale, 15 parts of flux a...
Embodiment 2
[0027] The preparation method of the cermet described in the present embodiment comprises the following steps:
[0028] The raw materials weighed according to parts by weight are respectively sent into a ball mill for ball milling, the rotating speed of the ball mill is 400rpm, and the ball milling time is 3h;
[0029] Send into high-speed mixer and carry out high-speed mixing, and the rotating speed of high-speed mixer is 280rpm;
[0030] Send it into a high-temperature sintering furnace for vacuum high-temperature sintering, the temperature of high-temperature sintering is 900°C, and the sintering time is 3.5h;
[0031] Cooling made cermet.
[0032] Among them, the raw materials are: 65 parts of ceramic powder, 15 parts of cobalt oxide, 15 parts of aluminum carbide, 10 parts of magnesium silicate, 8 parts of siliconized cobalt, 8 parts of ferrochromium oxide, 8 parts of chromium dioxide, 5 parts of manganese silicide, nitrogen 10 parts of silicon dioxide, 30 parts of shale...
PUM
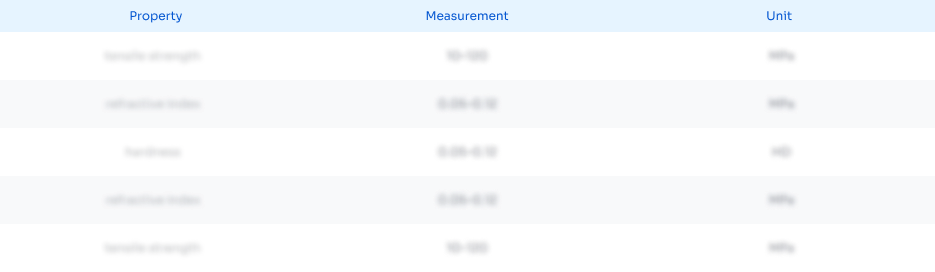
Abstract
Description
Claims
Application Information

- Generate Ideas
- Intellectual Property
- Life Sciences
- Materials
- Tech Scout
- Unparalleled Data Quality
- Higher Quality Content
- 60% Fewer Hallucinations
Browse by: Latest US Patents, China's latest patents, Technical Efficacy Thesaurus, Application Domain, Technology Topic, Popular Technical Reports.
© 2025 PatSnap. All rights reserved.Legal|Privacy policy|Modern Slavery Act Transparency Statement|Sitemap|About US| Contact US: help@patsnap.com