A method for efficiently separating and recovering zinc and cobalt from purified cobalt slag
A cobalt slag and high-efficiency technology, applied in the field of comprehensive recovery of hydrometallurgy, can solve the problems of comprehensive recovery and treatment of difficult metal resources, difficult recovery and regeneration of pharmaceuticals, and few metal resource processes, and achieves low cost, easy operation and high recovery efficiency. Effect
- Summary
- Abstract
- Description
- Claims
- Application Information
AI Technical Summary
Problems solved by technology
Method used
Image
Examples
Embodiment 1
[0030] A method for efficiently separating and recovering zinc and cobalt from purified cobalt slag, the specific steps are as follows:
[0031] Step 1, sulfuric acid leaching process:
[0032] Use sulfuric acid with a concentration of 1mol / L to leaching cobalt slag with a cobalt content of 0.5% in wet zinc smelting. The leaching temperature is 40°C, the leaching time is 40min, and the solid-to-liquid ratio is 5:1. After the reaction is completed, use a filter to filter to obtain zinc-rich , cobalt leaching solution and leaching slag containing copper, zinc, and cadmium. The leaching rate of zinc and cobalt is determined to be over 90% by atomic absorption spectrometry, and the leaching slag is used to recover zinc through the wet zinc smelting process;
[0033] Step 2, leachate neutralization and precipitation process:
[0034] A sodium hydroxide solution with a mass fraction of 45% is used to neutralize the leaching solution, the pH of the solution is adjusted to be 11, the...
Embodiment 2
[0040] Use sulfuric acid with a concentration of 1mol / L to leaching cobalt slag with a cobalt content of 1% by hydro-method zinc smelting. The leaching temperature is 70°C, the leaching time is 20 minutes, and the solid-to-liquid ratio is 5:1. After the reaction is completed, use a filter to filter to obtain zinc-rich , cobalt leaching solution and leaching slag containing copper, zinc, and cadmium. The leaching rate of zinc and cobalt is determined to be over 90% by atomic absorption spectrometry, and the leaching slag is used to recover zinc through the wet zinc smelting process;
[0041] Step 2, leachate neutralization and precipitation process:
[0042] The leaching solution is neutralized with an ammonia solution with a mass fraction of 55%, the pH of the solution is adjusted to be 13, the reaction temperature is 60° C., and the reaction time is 30 minutes. After the reaction is completed, filter with a filter to obtain a zincate solution and high-cobalt slag. Realize the...
Embodiment 3
[0048] Use a concentration of 1.5mol / L sulfuric acid to leaching the cobalt smelting cobalt slag with a cobalt content of 1.5%. The leaching temperature is 55°C, the leaching time is 30min, and the solid-to-liquid ratio is 7:1. After the reaction is completed, filter it with a filter to obtain Zinc and cobalt leaching solution and leaching slag containing copper, zinc and cadmium, the leaching rate of zinc and cobalt is determined to be over 90% by atomic absorption spectrometry, and the leaching slag is used to recover zinc through the wet zinc smelting process;
[0049] Step 2, leachate neutralization and precipitation process:
[0050] A sodium hydroxide solution with a mass fraction of 65% is used to neutralize the leaching solution, the pH of the solution is adjusted to be 15, the reaction temperature is 70° C., and the reaction time is 60 minutes. After the reaction is completed, filter with a filter to obtain zincate solution and high cobalt slag, realize efficient sepa...
PUM
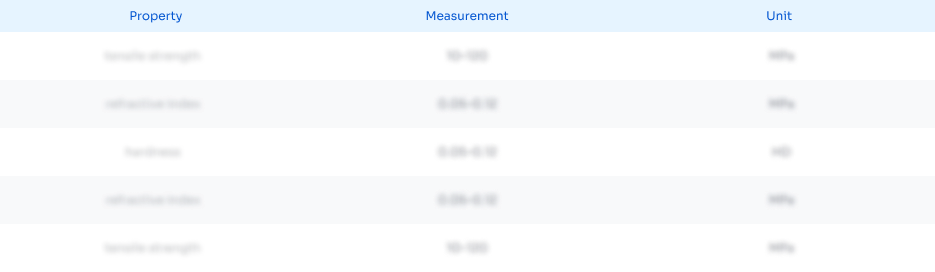
Abstract
Description
Claims
Application Information

- R&D
- Intellectual Property
- Life Sciences
- Materials
- Tech Scout
- Unparalleled Data Quality
- Higher Quality Content
- 60% Fewer Hallucinations
Browse by: Latest US Patents, China's latest patents, Technical Efficacy Thesaurus, Application Domain, Technology Topic, Popular Technical Reports.
© 2025 PatSnap. All rights reserved.Legal|Privacy policy|Modern Slavery Act Transparency Statement|Sitemap|About US| Contact US: help@patsnap.com