High-temperature wear-resistant surfacing alloy material based on ultralow-carbon high-boron and preparation method and application thereof
An alloy material, high-temperature wear-resistant technology, applied in welding/cutting media/materials, welding equipment, welding equipment, etc., to achieve wide application prospects, good high-temperature oxidation resistance, and enhanced high-temperature wear performance
- Summary
- Abstract
- Description
- Claims
- Application Information
AI Technical Summary
Problems solved by technology
Method used
Image
Examples
preparation example Construction
[0034] The present invention also provides a method for preparing a high-temperature wear-resistant surfacing alloy material based on ultra-low carbon and high boron, comprising the following steps:
[0035]Step 1. Weigh the alloy powder according to the above chemical composition requirements, use an electronic balance with an accuracy of 0.01mg to weigh the alloy powder with the corresponding content, mix it evenly, dry it in an environment of 150°C, then put it into a 304L stainless steel strip, and draw it It is a welding wire with a diameter of 2.8mm, which forms an ultra-low-carbon, high-boron, high-temperature wear-resistant metal powder-cored welding wire;
[0036] Step 2: Carry out derusting and degreasing cleaning on the surface of the base material, and put the base material into the workbench of the surfacing welding machine;
[0037] Step 3: Use coupled arc hot wire TIG welding, 99.7% argon as shielding gas, gas flow rate 15L / min, main arc voltage 20-24V, main arc...
Embodiment 1
[0043] Preparation of high-temperature wear-resistant surfacing alloy materials based on ultra-low carbon and high boron, including:
[0044] Step 1. Weigh the alloy powder according to the above chemical composition requirements, use an electronic balance with an accuracy of 0.01mg to weigh the alloy powder with the corresponding content, mix it evenly, dry it in an environment of 150°C, then put it into a 304L stainless steel strip, and draw it It is a welding wire with a diameter of 2.8mm, which forms an ultra-low-carbon, high-boron, high-temperature wear-resistant metal powder-cored welding wire;
[0045] Step 2: Carry out derusting and degreasing cleaning on the surface of the base material, and put the base material into the workbench of the surfacing welding machine;
[0046] Step 3. Use coupled arc hot wire TIG welding with high deposition efficiency, low dilution rate, and small heat loss to prepare surfacing alloy materials. By adjusting the wire feeding speed, send ...
Embodiment 2
[0050] Preparation of high-temperature wear-resistant surfacing alloy materials based on ultra-low carbon and high boron, including:
[0051] Step 1. Weigh the alloy powder according to the above chemical composition requirements, use an electronic balance with an accuracy of 0.01mg to weigh the alloy powder with the corresponding content, mix it evenly, dry it in an environment of 150°C, then put it into a 304L stainless steel strip, and draw it It is a welding wire with a diameter of 2.8mm, which forms an ultra-low-carbon, high-boron, high-temperature wear-resistant metal powder-cored welding wire;
[0052] Step 2: Carry out derusting and degreasing cleaning on the surface of the base material, and put the base material into the workbench of the surfacing welding machine;
[0053] Step 3. Use coupled arc hot wire TIG welding with high deposition efficiency, low dilution rate, and small heat loss to prepare surfacing alloy materials. By adjusting the wire feeding speed, send ...
PUM
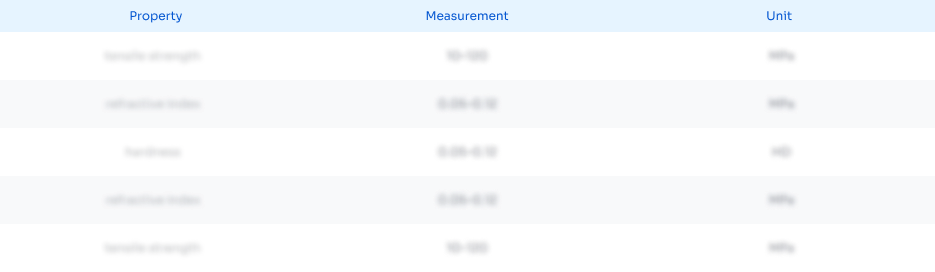
Abstract
Description
Claims
Application Information

- R&D
- Intellectual Property
- Life Sciences
- Materials
- Tech Scout
- Unparalleled Data Quality
- Higher Quality Content
- 60% Fewer Hallucinations
Browse by: Latest US Patents, China's latest patents, Technical Efficacy Thesaurus, Application Domain, Technology Topic, Popular Technical Reports.
© 2025 PatSnap. All rights reserved.Legal|Privacy policy|Modern Slavery Act Transparency Statement|Sitemap|About US| Contact US: help@patsnap.com