Precise heat treatment and quenching technology of precision part of high-purity hot-work die steel
A technology for hot work die steel and precision parts, which is applied in the field of precision heat treatment and quenching technology, which can solve the problem that it is difficult to accurately and reliably control the change of the crystal phase structure of the material, the best working state of the working performance mold cannot be achieved, and it is difficult to accurately and reliably control the quenching hardness. and other problems, to achieve high engineering application value, significant social and economic benefits, and the effect of grain refinement
- Summary
- Abstract
- Description
- Claims
- Application Information
AI Technical Summary
Problems solved by technology
Method used
Image
Examples
Embodiment 1
[0020] Example 1 ``Hot work die steel precision parts with a thickness of less than 5mm, the hardness requirement is HRC33
[0021] (1) Put a batch of workpieces with a thickness of less than 5mm into the quenching furnace and preheat to 150°C at a heating rate of less than 75°C / hour;
[0022] (2) The workpiece is heated to 850℃ in the quenching furnace and kept for 15min, and then heated to the quenching temperature of 1020℃ and kept for 10min;
[0023] (3) Take the workpiece out of the furnace and place it on the support, turn on the blower, and cool the workpiece to 50-70℃;
[0024] (4) When the workpiece is air-cooled to 50 ℃-70 ℃, immediately enter the tempering furnace to heat to 650 ℃ for tempering and keep it for 90 minutes, then take it out of the furnace for natural air cooling;
[0025] (5) When the workpiece is air-cooled to 50 ℃-70 ℃, immediately enter the tempering furnace for the second time and heat it to 650 ℃ for tempering and keep it for 90 minutes, then take it out o...
Embodiment 2
[0027] Example 2 The hardness of precision parts of hot work die steel with a thickness of 6-10mm is required to be HRC38
[0028] (1) Put a batch of 6-10mm thick workpieces into the quenching furnace and preheat to 150°C at a heating rate of less than 75°C / hour;
[0029] (2) The workpiece is heated to 850 in the quenching furnace 0 C and keep for 20min, then continue to heat to quenching temperature 1020 0 C and keep for 15min;
[0030] (3) Take the workpiece out of the furnace and place it on the support, turn on the blower, and cool the workpiece to 50-70℃;
[0031] (4) When the workpiece is air-cooled to 50 0 C-70 0 At C, immediately heat into the tempering furnace to 630 0 C is tempered and kept for 90 minutes, and is naturally air-cooled after being discharged;
[0032] (5) When the workpiece is air-cooled to 50 0 C-70 0 At C, immediately enter the tempering furnace for the second time and heat to 630 0 C is tempered and kept for 90 minutes, and it is naturally air-cooled to roo...
Embodiment 3
[0034] Example 3 Hot work die steel precision parts with thickness of 11-15mm, hardness requirement is HRC42
[0035] 1. Put a batch of 11-15mm thick workpieces into the quenching furnace and preheat to 150°C at a heating rate of less than 75°C / hour;
[0036] 2. The workpiece is heated to 850 in the quenching furnace 0 C and keep for 30min, then continue to heat to quenching temperature 1020 0 C and keep for 22min;
[0037] 3. Put the workpiece out of the furnace and place it on the support, turn on the blower, and cool the workpiece to 50-70℃;
[0038] 4. When the workpiece is air-cooled to 50 0 C-70 0 At C, immediately heat it into the tempering furnace to 610 0 C is tempered and kept for 120 minutes, and it is naturally air-cooled from the furnace;
[0039] 5. When the workpiece is air-cooled to 50 0 C-70 0 At C, immediately enter the tempering furnace for the second time and heat to 610 0 C is tempered and kept for 120min, and it is naturally cooled to room temperature after being d...
PUM
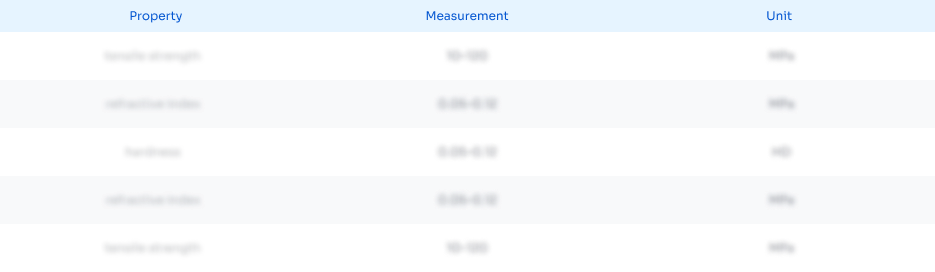
Abstract
Description
Claims
Application Information

- Generate Ideas
- Intellectual Property
- Life Sciences
- Materials
- Tech Scout
- Unparalleled Data Quality
- Higher Quality Content
- 60% Fewer Hallucinations
Browse by: Latest US Patents, China's latest patents, Technical Efficacy Thesaurus, Application Domain, Technology Topic, Popular Technical Reports.
© 2025 PatSnap. All rights reserved.Legal|Privacy policy|Modern Slavery Act Transparency Statement|Sitemap|About US| Contact US: help@patsnap.com