Method for preparing high-strength heat-preservation wallboard
A thermal insulation wall panel, high-strength technology, used in building components, building materials, buildings, etc., can solve the problems of insufficient thermal insulation and low strength, and achieve good thermal insulation effect, less environmental pollution, and light weight.
- Summary
- Abstract
- Description
- Claims
- Application Information
AI Technical Summary
Problems solved by technology
Method used
Examples
Embodiment 1
[0018] A preparation method for a high-strength thermal insulation wallboard, comprising the steps of:
[0019] S1, mix 5kg xanthan gum, 30kg expanded perlite, 50kg concentration of 6wt% hydrogen peroxide solution, filter, adjust the system to be neutral, add 0.1kg ammonium persulfate, 0.09kg sodium bisulfite and stir for 10min under nitrogen protection, Add 2 kg of acrylamide and stir for 2 hours, precipitate with acetone, and dry to obtain the prefabricated material;
[0020] S2. Stir 100kg of cement, 20kg of prefabricated materials, 40kg of polyurethane emulsion, 10kg of nylon fiber, 23kg of coal gangue, and 2kg of glutinous rice flour for 6 minutes at a stirring speed of 100r / min, pressing for 40s at a pressing pressure of 2MPa, and pressing again for 2 minutes after shaking, then Steam curing for 10 hours, the temperature of steam curing is 100°C, and natural drying for 40 hours to obtain high-strength thermal insulation wallboard.
Embodiment 2
[0022] A preparation method for a high-strength thermal insulation wallboard, comprising the steps of:
[0023] S1, mix 10kg xanthan gum, 20kg expanded perlite, and 100kg concentration of 2wt% hydrogen peroxide solution evenly, filter, adjust the system to be neutral, add 0.2kg ammonium persulfate and 0.05kg sodium bisulfite under nitrogen protection and stir for 20min, Add 1 kg of acrylamide and stir for 4 hours, precipitate with acetone, and dry to obtain the prefabricated material;
[0024] S2. Stir 50kg of cement, 40kg of prefabricated materials, 20kg of polyurethane emulsion, 20kg of nylon fiber, 15kg of coal gangue, and 10kg of glutinous rice flour for 2 minutes at a stirring speed of 150 r / min, pressing for 20 seconds at a pressing pressure of 5 MPa, pressing again for 1 minute after shaking, and then Steam curing for 20 hours at a temperature of 90°C, and natural drying for 100 hours to obtain high-strength thermal insulation wallboards.
Embodiment 3
[0026] A preparation method for a high-strength thermal insulation wallboard, comprising the steps of:
[0027] S1, mix 6kg xanthan gum, 28kg expanded perlite, and 60kg concentration of 5wt% hydrogen peroxide solution evenly, filter, adjust the system to be neutral, add 0.12kg ammonium persulfate and 0.08kg sodium bisulfite under nitrogen protection and stir for 12min, Add 1.7 kg of acrylamide and stir for 2.5 hours, precipitate with acetone, and dry to obtain the prefabricated material;
[0028] S2. Stir 80kg of cement, 25kg of prefabricated materials, 35kg of polyurethane emulsion, 12kg of nylon fiber, 20kg of coal gangue, and 4kg of glutinous rice flour for 5 minutes at a stirring speed of 120r / min, press for 35s, and press at a pressure of 3MPa, and press again for 1.8min after shaking. Then steam curing for 12 hours, the temperature of steam curing is 98°C, and it is naturally dried for 60 hours to obtain a high-strength thermal insulation wallboard.
PUM
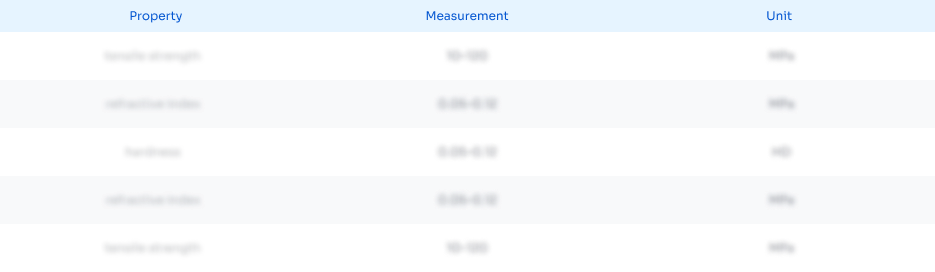
Abstract
Description
Claims
Application Information

- R&D
- Intellectual Property
- Life Sciences
- Materials
- Tech Scout
- Unparalleled Data Quality
- Higher Quality Content
- 60% Fewer Hallucinations
Browse by: Latest US Patents, China's latest patents, Technical Efficacy Thesaurus, Application Domain, Technology Topic, Popular Technical Reports.
© 2025 PatSnap. All rights reserved.Legal|Privacy policy|Modern Slavery Act Transparency Statement|Sitemap|About US| Contact US: help@patsnap.com