A method of intermediate frequency resistance diffusion welding of graphite electrodes with controllable deformation
A graphite electrode and deformation technology, which is applied in resistance welding equipment, welding equipment, metal processing equipment, etc., can solve the problems of affecting the mechanical and mechanical bearing capacity of welding fin parts, welding voids and welding, and serious deformation of collapsed edges. The effect of large deformation, excellent electrical conductivity, and simple clamping method
- Summary
- Abstract
- Description
- Claims
- Application Information
AI Technical Summary
Problems solved by technology
Method used
Image
Examples
Embodiment 1
[0033] A method of intermediate frequency resistance diffusion welding of graphite electrodes with controllable deformation according to Figure 1-2 As shown in the installation results, the following steps are included:
[0034] S1: Grinding the surfaces to be welded of the thick weldment 5, the thin weldment 3 and the high-temperature solder 4, and cleaning and drying;
[0035] S2: Install copper anode 1 and copper cathode 7 facing up and down, then install graphite anode 2 and graphite cathode 6 on the inside of copper anode 1 and copper cathode 7, respectively, and adjust the positions of graphite anode 2 and graphite cathode 6 , so that the up and down are aligned, and then the graphite anode 2 and the graphite cathode 6 are respectively connected to the positive and negative electrodes of the heating pulse power supply, and the power is turned on to check whether the thermal radiation is normal;
[0036] S3: Turn off the power after detecting that the heat radiation is ...
Embodiment 2
[0047] A method of intermediate frequency resistance diffusion welding of graphite electrodes with controllable deformation according to Figure 1-2 As shown in the installation results, the following steps are included:
[0048] S1: Grinding the surfaces to be welded of the thick weldment 5, the thin weldment 3 and the high-temperature solder 4, and cleaning and drying;
[0049] S2: Install copper anode 1 and copper cathode 7 facing up and down, then install graphite anode 2 and graphite cathode 6 on the inside of copper anode 1 and copper cathode 7, respectively, and adjust the positions of graphite anode 2 and graphite cathode 6 , so that the up and down are aligned, and then the graphite anode 2 and the graphite cathode 6 are respectively connected to the positive and negative electrodes of the heating pulse power supply, and the power is turned on to check whether the thermal radiation is normal;
[0050] S3: Turn off the power after detecting that the heat radiation is ...
Embodiment 3
[0061] A method of intermediate frequency resistance diffusion welding of graphite electrodes with controllable deformation according to Figure 1-2 As shown in the installation results, the following steps are included:
[0062] S1: Grinding the surfaces to be welded of the thick weldment 5, the thin weldment 3 and the high-temperature solder 4, and cleaning and drying;
[0063] S2: Install copper anode 1 and copper cathode 7 facing up and down, then install graphite anode 2 and graphite cathode 6 on the inside of copper anode 1 and copper cathode 7, respectively, and adjust the positions of graphite anode 2 and graphite cathode 6 , so that the up and down are aligned, and then the graphite anode 2 and the graphite cathode 6 are respectively connected to the positive and negative electrodes of the heating pulse power supply, and the power is turned on to check whether the thermal radiation is normal;
[0064] S3: Turn off the power after detecting that the heat radiation is ...
PUM
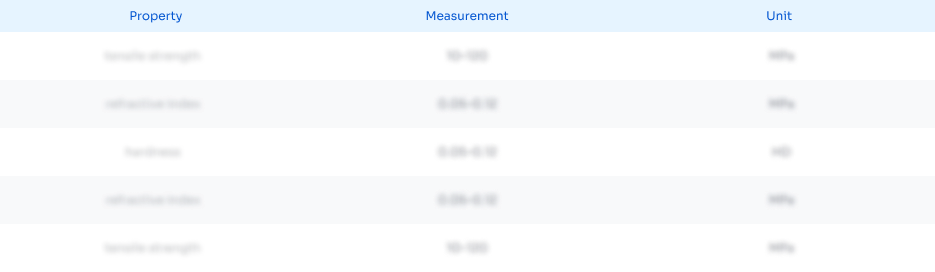
Abstract
Description
Claims
Application Information

- R&D
- Intellectual Property
- Life Sciences
- Materials
- Tech Scout
- Unparalleled Data Quality
- Higher Quality Content
- 60% Fewer Hallucinations
Browse by: Latest US Patents, China's latest patents, Technical Efficacy Thesaurus, Application Domain, Technology Topic, Popular Technical Reports.
© 2025 PatSnap. All rights reserved.Legal|Privacy policy|Modern Slavery Act Transparency Statement|Sitemap|About US| Contact US: help@patsnap.com