A multi-process milling processing system for aluminum alloy anti-melting welding
A processing system and multi-process technology, applied in the direction of metal processing equipment, metal processing machinery parts, workpieces, etc., can solve problems affecting work efficiency, operator injury, scratching the operator, etc., to improve cleaning efficiency and work efficiency , the effect of reducing the amount of cleaning
- Summary
- Abstract
- Description
- Claims
- Application Information
AI Technical Summary
Problems solved by technology
Method used
Image
Examples
Embodiment approach
[0026] As an embodiment of the present invention, the chip blocking module 3 includes a box body 31, a chip blocking plate 32, a spring 33, a second cam 34, a vibration motor 35 and a guide plate 36; the box body 31 is fastened by bolts On the milling machine table 6, it is located on one side of the chip platform 4; the side of the box body 31 is slidably installed with a chip blocking plate 32; the lower end of the chip blocking plate 32 is provided with a spring 33; the upper end of the chip blocking plate 32 contacts The second cam 34 is connected; the second cam 34 is fixedly installed on the rotating shaft of the vibration motor 35; the vibration motor 35 is fixedly installed on the upper part of the box body 31; The chip blocking plate 32 vibrates to clean up the chips attached to the surface; the guide plate 36 is fixedly installed at the bottom of the box body 31 .
[0027] As an embodiment of the present invention, the surface of the chip blocking plate 32 is covered...
PUM
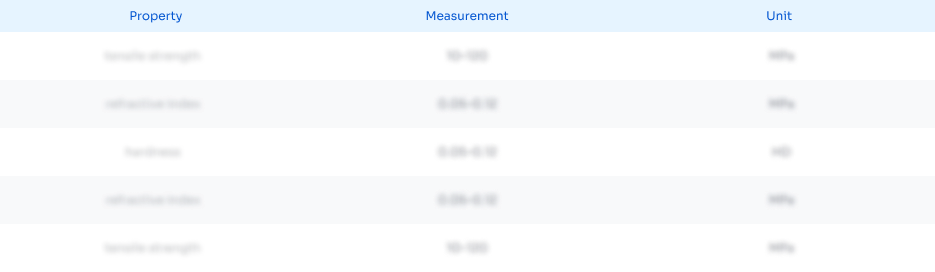
Abstract
Description
Claims
Application Information

- R&D
- Intellectual Property
- Life Sciences
- Materials
- Tech Scout
- Unparalleled Data Quality
- Higher Quality Content
- 60% Fewer Hallucinations
Browse by: Latest US Patents, China's latest patents, Technical Efficacy Thesaurus, Application Domain, Technology Topic, Popular Technical Reports.
© 2025 PatSnap. All rights reserved.Legal|Privacy policy|Modern Slavery Act Transparency Statement|Sitemap|About US| Contact US: help@patsnap.com