Polycrystal black silicon texturing process
A technology of black silicon and process, which is applied in the field of polycrystalline black silicon texturing process, can solve the problems of complex texturing process and lack of silicon wafers, etc., and achieve the effect of uniform holes, blurred appearance and good appearance
- Summary
- Abstract
- Description
- Claims
- Application Information
AI Technical Summary
Problems solved by technology
Method used
Image
Examples
Embodiment 1
[0036] A polycrystalline black silicon texturing process, comprising the steps of:
[0037] 1) Polysilicon wafers are polished with polishing liquid;
[0038] The polishing liquid is composed of 5% to 15% potassium hydroxide or sodium hydroxide, 0.3% to 0.8% polishing auxiliary agent and the balance of deionized water;
[0039] The polishing aid is composed of 1.0% to 3.0% sodium benzoate, 1.0% to 2.0% sodium acetate, 0.5% to 2.0% glycerol, 0.2% to 1.0% polyethylene glycol, 5.0% to 10.0% sodium silicate and The remainder is composed of deionized water;
[0040] The temperature of the polishing treatment is 70-80°C, and the time is 200-250s;
[0041] 2) Dig holes on the polished silicon wafers with a hole-digging treatment solution, and prepare nano-holes on the surface of the silicon wafers;
[0042] The hole-digging treatment liquid is composed of 0.2%-0.5% hydrogen peroxide, 2%-5% hydrofluoric acid, 0.4%-1.2% hole-digging auxiliary agent and the balance of deionized water...
Embodiment 2
[0051] On the basis of embodiment 1, the difference is:
[0052] The polishing liquid is composed of 8% to 12% potassium hydroxide or sodium hydroxide, 0.4% to 0.7% polishing auxiliary agent and the balance of deionized water;
[0053] The polishing aid consists of 1.5% to 2.0% sodium benzoate, 1.5% to 2.0% sodium acetate, 1.0% to 2.0% glycerol, 0.5% to 0.8% polyethylene glycol, 5.0% to 8.0% sodium silicate and The remainder is composed of deionized water;
[0054] Wherein, each percentage is volume percentage.
Embodiment 3
[0056] On the basis of embodiment 1, the difference is:
[0057]The hole-digging treatment liquid is composed of 0.2%-0.4% hydrogen peroxide, 2%-4% hydrofluoric acid, 0.5%-1.0% hole-digging auxiliary agent and the balance of deionized water;
[0058] The hole-digging auxiliary agent consists of 1.0%-2.0% citric acid, 1.0%-2.0% butanediol, 0.05%-0.1% silver nitrate, 0.2%-0.5% hydroxyethyl cellulose, 1.5%-3.0% tartaric acid, 0.5%~0.8% polyethylene glycol, 0.5%~0.8% silane coupling agent, 0.8%~1.0% triethanolamine, 0.5%~0.8% polyaspartic acid, 0.5%~1.0% polyvinyl alcohol, 0.5% ~1.0% polyoxyethylene lauryl ether and the balance of deionized water;
[0059] Wherein, each percentage is volume percentage.
PUM
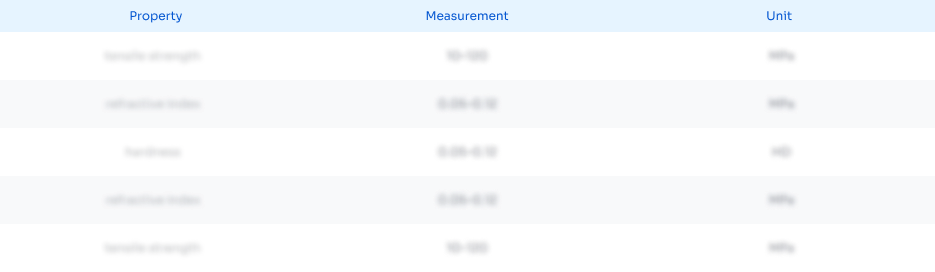
Abstract
Description
Claims
Application Information

- Generate Ideas
- Intellectual Property
- Life Sciences
- Materials
- Tech Scout
- Unparalleled Data Quality
- Higher Quality Content
- 60% Fewer Hallucinations
Browse by: Latest US Patents, China's latest patents, Technical Efficacy Thesaurus, Application Domain, Technology Topic, Popular Technical Reports.
© 2025 PatSnap. All rights reserved.Legal|Privacy policy|Modern Slavery Act Transparency Statement|Sitemap|About US| Contact US: help@patsnap.com