Special alkali texturing additive for diamond wire cutting single crystal silicon wafers, and using method of additive
A technology of diamond wire cutting and monocrystalline silicon wafers, which is applied in the direction of single crystal growth, single crystal growth, chemical instruments and methods, etc. It can solve the problems of large amount of isopropanol, poor repeatability of texturing, long time of texturing, etc. , to achieve the effects of improving stability and consistency, shortening the time of making texture, and improving the residual line marks
- Summary
- Abstract
- Description
- Claims
- Application Information
AI Technical Summary
Problems solved by technology
Method used
Image
Examples
Embodiment 1
[0022] In the present embodiment, a method for making texturing of a monocrystalline silicon wafer is provided, and the following process steps are taken:
[0023] 1) Prepare additives: under stirring, dissolve 2.0g polyol, 1.0g polyvinyl alcohol, 0.1g anionic surfactant, 0.1g silicon-based defoamer and 1g sodium silicate in 95.8 g deionized water ( That is: in the prepared additives, the weight percentage of the polyhydric alcohol is 2%, the weight percentage of the polyvinyl alcohol is 1%, the anionic surfactant is 0.1%, the silicon-based 0.1% by weight of defoamer and 1% by weight of sodium silicate);
[0024] 2) Prepare alkaline texturing solution: under stirring, mix 2500g of sodium hydroxide and 100L of deionized water evenly, then add 1000ml of the above-mentioned additives, and stir evenly;
[0025] 3) Texturing: immerse the diamond wire-cut monocrystalline silicon wafer in the above alkali texturing solution for texturing, the texturing temperature is 82°C, and the t...
Embodiment 2
[0027] In the embodiment of the present invention, a method for making texturing of a monocrystalline silicon wafer is provided, and the following process steps are taken:
[0028] 1) Prepare additives: under stirring, dissolve 5.0g polyol, 0.5g polyvinyl alcohol, 0.05g anionic surfactant, 0.05g silicon-based defoamer and 3.0g sodium silicate in 91.4 g deionized water (That is: in the prepared additives, the weight percentage of the polyol is 5%, the weight percentage of the polyvinyl alcohol is 0.5%, the anionic surfactant is 0.05%, the silicon Base defoamer weight percentage content is 0.05% and sodium silicate weight percentage content is 3%);
[0029] 2) Prepare alkaline texturing solution: under stirring, mix 2500g of sodium hydroxide and 100 L of deionized water evenly, then add 1000ml of the above-mentioned additives, and stir evenly;
[0030] 3) Texturing: immerse the diamond wire-cut monocrystalline silicon wafer in the above alkali texturing solution for texturing, ...
Embodiment 3
[0032] In the embodiment of the present invention, a method for making texturing of a monocrystalline silicon wafer is provided, and the following process steps are taken:
[0033] 1) Prepare additives: under stirring, dissolve 3.0g polyol, 1.5g polyvinyl alcohol, 0.1g anionic surfactant, 0.1g silicon-based defoamer and 2.0g sodium silicate in 93.3 g deionized water (That is: in the prepared additives, the weight percentage of the polyhydric alcohol is 3%, the weight percentage of the polyvinyl alcohol is 1.5%, the anionic surfactant is 0.1%, the silicon Base defoamer weight percentage is 0.1% and sodium silicate weight percentage is 2%);
[0034] 2) Prepare alkaline texturing solution: under stirring, mix 2500g of sodium hydroxide and 100 L of deionized water evenly, then add 1000ml of the above-mentioned additives, and stir evenly;
[0035] 3) Texturing: immerse the diamond wire-cut monocrystalline silicon wafer in the above alkali texturing solution for texturing, the text...
PUM
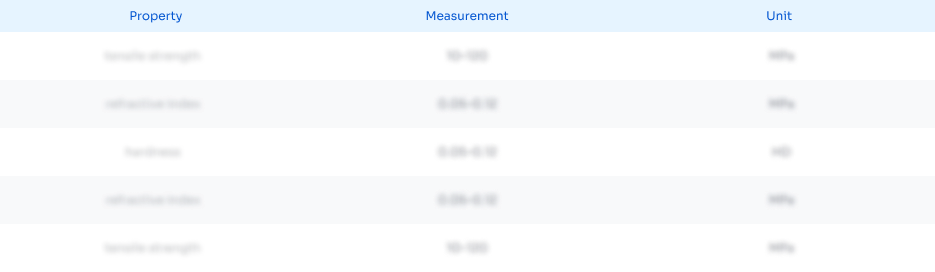
Abstract
Description
Claims
Application Information

- R&D
- Intellectual Property
- Life Sciences
- Materials
- Tech Scout
- Unparalleled Data Quality
- Higher Quality Content
- 60% Fewer Hallucinations
Browse by: Latest US Patents, China's latest patents, Technical Efficacy Thesaurus, Application Domain, Technology Topic, Popular Technical Reports.
© 2025 PatSnap. All rights reserved.Legal|Privacy policy|Modern Slavery Act Transparency Statement|Sitemap|About US| Contact US: help@patsnap.com