High-performance environment-friendly flame-retardant communication cable sheathing compound and preparation method thereof
A communication cable, a high-performance technology, applied in the direction of circuits, electrical components, plastic/resin/wax insulators, etc., to achieve the effect of broad market application prospects, controllable response, and long service life
- Summary
- Abstract
- Description
- Claims
- Application Information
AI Technical Summary
Problems solved by technology
Method used
Image
Examples
Embodiment 1
[0022] Example 1: The preparation ratio of each raw material in the high-performance environment-friendly flame-retardant communication cable sheath material
[0023] The raw materials in the high-performance, environment-friendly, flame-retardant communication cable sheathing material were mixed according to the mass fractions described in Table 1, and three groups of high-performance, environment-friendly, flame-retardant communication cable sheathing materials I to III with different mixing ratios were obtained.
[0024] Table 1 High-performance environment-friendly flame-retardant communication cable sheathing materials I-III with different mixing ratios (mass parts)
[0025]
Embodiment 2
[0026] Embodiment 2: the preparation method of high-performance environment-friendly flame-retardant communication cable sheathing material I
[0027] Step 1. Preparation of epoxy-modified polyurethane: Put 30 parts of polyether polyol into the reaction kettle, heat to 120°C for reflux dehydration for 1 hour while stirring, then add 35 parts of toluene diisocyanate when the temperature is lowered to 50°C, and slowly heat up to Stir at 80°C for 4-6 hours to obtain a polyurethane prepolymer; dehydrate 15 parts of diglycidyl tetrahydrophthalate at 80°C for 1-3 hours in vacuum, cool down to 60°C, and then add the Polyurethane prepolymer, 8 parts of 1,4-butanediol, 15 parts of trimethylolpropane, 16 parts of methyl tetrahydrophthalic anhydride and 2,3,6-tris(dimethylaminomethyl ) 1 part of phenol, heated up to 70-90°C, stirred and reacted for 6-8 hours, to obtain the epoxy-modified polyurethane;
[0028] Preparation of active flame retardant: under the protection of nitrogen, add ...
Embodiment 3
[0030] Embodiment 3: the preparation method of high-performance environment-friendly flame-retardant communication cable sheath material II
[0031] Step 1. Preparation of epoxy-modified polyurethane: Put 45 parts of polyether polyol into the reaction kettle, heat to 120°C for reflux dehydration for 1 hour while stirring, then add 55 parts of toluene diisocyanate when the temperature is lowered to 50°C, and slowly heat up to Stir at 80°C for 4-6 hours to obtain a polyurethane prepolymer; dehydrate 25 parts of diglycidyl tetrahydrophthalate at 80°C for 1-3 hours in vacuum, cool down to 60°C, and then add the Polyurethane prepolymer, 12 parts of 1,4-butanediol, 23 parts of trimethylolpropane, 24 parts of methyl tetrahydrophthalic anhydride and 2,3,6-tris(dimethylaminomethyl ) 5 parts of phenol, heated up to 70-90°C, stirred and reacted for 6-8 hours, to obtain the epoxy-modified polyurethane;
[0032] Preparation of active flame retardant: under the protection of nitrogen, add di...
PUM
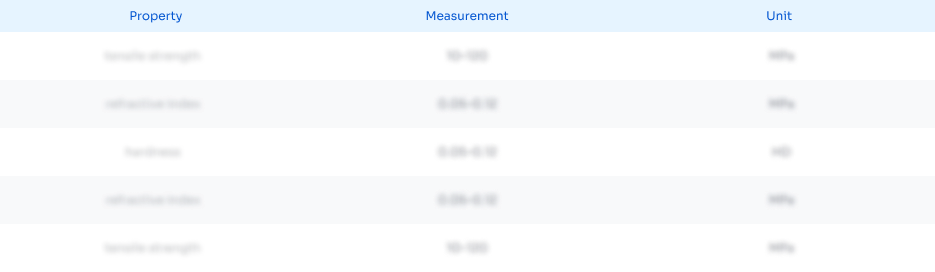
Abstract
Description
Claims
Application Information

- R&D
- Intellectual Property
- Life Sciences
- Materials
- Tech Scout
- Unparalleled Data Quality
- Higher Quality Content
- 60% Fewer Hallucinations
Browse by: Latest US Patents, China's latest patents, Technical Efficacy Thesaurus, Application Domain, Technology Topic, Popular Technical Reports.
© 2025 PatSnap. All rights reserved.Legal|Privacy policy|Modern Slavery Act Transparency Statement|Sitemap|About US| Contact US: help@patsnap.com