Damping coating with interpenetrating network (IPN) structure, and preparation method of damping coating
An interpenetrating network structure and damping coating technology, applied in epoxy resin coatings, polyurea/polyurethane coatings, coatings, etc., can solve the problems of short drying time, complicated laying, inapplicability, etc., and achieve short drying time and construction. Simple and good film-forming effect
- Summary
- Abstract
- Description
- Claims
- Application Information
AI Technical Summary
Problems solved by technology
Method used
Image
Examples
preparation example Construction
[0035] A method for preparing a damping coating with an interpenetrating network structure, comprising the following steps: step 1, weighing each raw material according to the weight percentage of the raw material, then adding the weighed polyurethane resin and epoxy resin to a mixer to mix evenly, and adding Auxiliary agent, be mixed with polyurethane / epoxy resin base material solution; Step 2, pigment is joined in the polyurethane / epoxy resin base material solution that step 1 makes, stir 30min with the rotating speed of 3000r / min, control material temperature at 50 Below ℃, make a uniformly dispersed color paste solution; step 3, add damping filler and sound insulation filler to the color paste solution prepared in step 2 in turn, stir at a speed of 1500r / min for 30min, and then transfer to a sand mill , grinding to a slurry-like homogeneous liquid with a fineness not greater than 40 μm; step 4, adding the curing agent to the slurry-like homogeneous liquid prepared in step 3...
Embodiment 1
[0041] Polyether polyurethane resin 70g;
[0042] E12 epoxy resin 70g;
[0043] Toluene diisocyanate 70g;
[0045] Barite powder 48g;
[0046] Carbon black 1g;
[0047] Additives 6g (composed of BYK530, BYK320, BYK110 with a weight ratio of 1:1:1); the mass ratio of polyurethane resin / epoxy resin is 1:1.
[0048] A method for preparing a damping coating with an interpenetrating network structure, comprising the following steps: step 1, weighing each raw material according to the above weight percentage, then adding the weighed polyurethane resin and epoxy resin into a mixer to mix evenly, and adding Additives, formulated into polyurethane / epoxy resin binder solution;
[0049] Step 2. Add the pigment to the polyurethane / epoxy resin base material solution prepared in step 1, stir for 30 minutes at a speed of 3000r / min, and control the temperature of the material below 50°C to make a uniformly dispersed color paste solution;
[0050] Step 3: Add th...
Embodiment 2
[0055] 70g of hydroxyl-terminated polyurethane resin;
[0056] E20 epoxy resin 46g;
[0057] Diphenylmethane diisocyanate 52g;
[0059] Barite powder 51g;
[0060] Carbon black 1g;
[0061] Additive 6g; the mass ratio of polyurethane resin / epoxy resin is 1.5:1.
[0062] The operation steps of the preparation method are the same as in Example 1.
[0063] The supporting adhesion strength of the interpenetrating network damping coating reaches 8.3MPa, and the sound insulation of the coating is 28dB at f=2100Hz, and the damping performance is as follows: figure 2 As shown, the damping factor can reach up to 0.83.
PUM
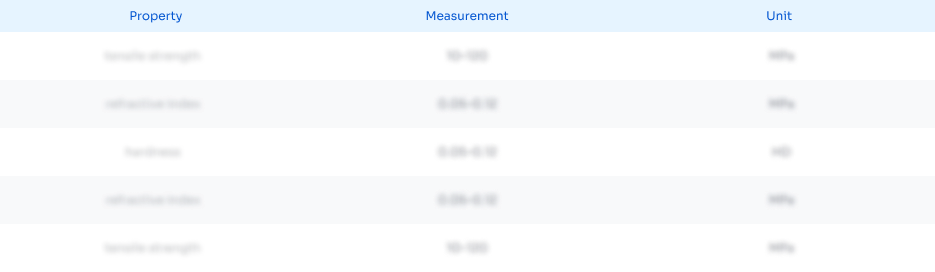
Abstract
Description
Claims
Application Information

- Generate Ideas
- Intellectual Property
- Life Sciences
- Materials
- Tech Scout
- Unparalleled Data Quality
- Higher Quality Content
- 60% Fewer Hallucinations
Browse by: Latest US Patents, China's latest patents, Technical Efficacy Thesaurus, Application Domain, Technology Topic, Popular Technical Reports.
© 2025 PatSnap. All rights reserved.Legal|Privacy policy|Modern Slavery Act Transparency Statement|Sitemap|About US| Contact US: help@patsnap.com