Aluminum nitride powder and preparation method thereof
A technology of aluminum nitride and powder, which is applied in the field of aluminum nitride powder and its preparation, can solve the problems of uneven size distribution, high equipment requirements, complex process, etc., and achieve uniform size distribution, low equipment requirements, and simple process Effect
- Summary
- Abstract
- Description
- Claims
- Application Information
AI Technical Summary
Problems solved by technology
Method used
Image
Examples
preparation example Construction
[0029] See figure 1 , the preparation method of aluminum nitride powder shown in the present invention comprises the following steps:
[0030] S1. Provide alumina precursors and carbon and nitrogen compounds, wherein the alumina precursors undergo a coordination reaction between aluminum alkoxide and a chelating agent at 50 to 95°C under reflux conditions, followed by hydrolysis and polycondensation at 60 to 100°C reaction, and finally remove the solvent, wherein the chelating agent is preferably acetylacetone, and the solvent is selected from the group consisting of toluene, xylene, ethanol, n-propanol, isopropanol, ethylene glycol methyl ether or ethylene glycol ether any of
[0031] S2. Blend the alumina precursor and carbon and nitrogen compounds to form a uniform mixed solution, and then remove the solvent in the mixed solution by vacuum drying, spray drying or direct drying at 30°C to 150°C, A viscous solution or colloidal solid is obtained, and then the obtained visco...
Embodiment 1
[0037] ① Precursor cured product preparation:
[0038] (1) The aluminum oxide precursor and the phenolic resin are blended into an ethanol solution with a solid content of 15% according to the ratio of aluminum element to carbon element mass ratio of 1:0.7;
[0039] (2) The solvent in the above solution is removed by vacuum drying at 70° C. to obtain a colloidal solid;
[0040] (3) The obtained solid is cured and debinding in a debinding furnace at 600° C., and the selected atmosphere is nitrogen to obtain a cured precursor.
[0041] ② Preparation of aluminum nitride powder
[0042] After grinding the cured precursor obtained above through an 80-mesh sieve, carry out high-temperature sintering treatment at 1600°C, a nitrogen atmosphere of 700mL / min, and a heating rate of 10°C / min, and keep it warm for 4 hours to obtain aluminum nitride. Ultrafine powder.
[0043] ③Purification of aluminum nitride powder
[0044] Purify and sinter the above-mentioned aluminum nitride ultraf...
Embodiment 2
[0047] ① Precursor cured product preparation:
[0048] (1) The aluminum oxide precursor and the allyl phenolic resin are blended into a 15% n-propanol solution with a solid content of 15% according to the ratio of aluminum element and carbon element mass ratio of 1:5;
[0049] (2) The solvent in the above solution is removed by vacuum drying at 50° C. to obtain a viscous solution;
[0050] (3) The obtained viscous liquid is cured and deglued in a debinding furnace at 250°C, the heating rate is 10°C / min, and maintained at 250°C for 4 hours, the selected atmosphere is air, and a cured precursor is obtained .
[0051] ② Preparation of aluminum nitride powder
[0052] Grind the cured precursor obtained above through a 40-mesh sieve, then carry out high-temperature sintering treatment at 1700°C, 2L / min nitrogen atmosphere, and a heating rate of 15°C / min, and keep it warm for 4 hours to obtain super aluminum nitride. fine powder.
[0053] ③Purification of aluminum nitride powder...
PUM
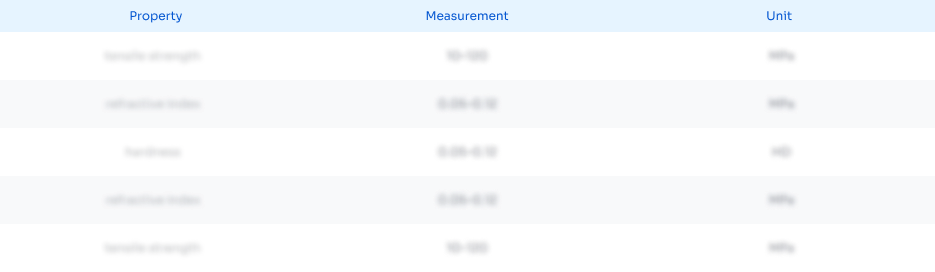
Abstract
Description
Claims
Application Information

- R&D Engineer
- R&D Manager
- IP Professional
- Industry Leading Data Capabilities
- Powerful AI technology
- Patent DNA Extraction
Browse by: Latest US Patents, China's latest patents, Technical Efficacy Thesaurus, Application Domain, Technology Topic, Popular Technical Reports.
© 2024 PatSnap. All rights reserved.Legal|Privacy policy|Modern Slavery Act Transparency Statement|Sitemap|About US| Contact US: help@patsnap.com