Determining method of designed shrinkage of hollow turbine blade investment casting mold
A turbine blade and mold design technology, applied in the direction of calculation, special data processing applications, instruments, etc., can solve the problems of long cycle, low precision, low efficiency, etc., to avoid blade forming accuracy, reduce cycle and times, and improve yield Effect
- Summary
- Abstract
- Description
- Claims
- Application Information
AI Technical Summary
Problems solved by technology
Method used
Image
Examples
Embodiment Construction
[0043] The following embodiments will further illustrate the present invention in conjunction with the accompanying drawings.
[0044] step 1:
[0045] A certain type of hollow turbine blade casting system model 1 includes a module with two blades, which are distributed axisymmetrically. Among them, the main geometric parameters of the blade are blade body length 101mm, maximum chord length 59.21mm, maximum inscribed circle radius 5.67mm, and trailing edge radius 1.27mm. The blade includes a blade profile 2, a rafter plate 3, and a tenon 4 that meet aerodynamic requirements. According to the casting feeding theory and actual production experience, in order to ensure the stability of the alloy, the pouring method is adopted from the pouring riser 7 with the tenon 4 downward, and the cold copper 6 is quenched to form directional solidification, and the spiral type is adopted according to the actual pouring situation of the factory. Crystal selector 5, the pouring system can re...
PUM
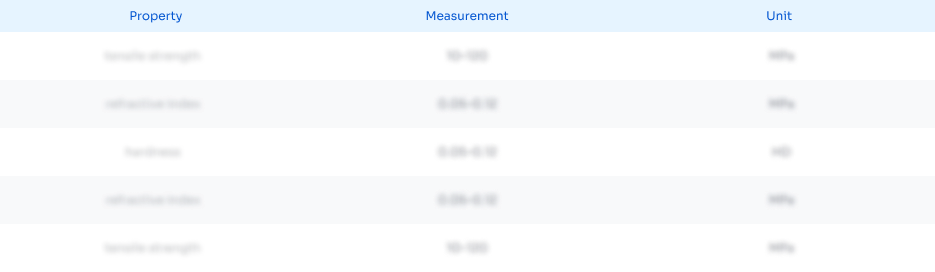
Abstract
Description
Claims
Application Information

- R&D
- Intellectual Property
- Life Sciences
- Materials
- Tech Scout
- Unparalleled Data Quality
- Higher Quality Content
- 60% Fewer Hallucinations
Browse by: Latest US Patents, China's latest patents, Technical Efficacy Thesaurus, Application Domain, Technology Topic, Popular Technical Reports.
© 2025 PatSnap. All rights reserved.Legal|Privacy policy|Modern Slavery Act Transparency Statement|Sitemap|About US| Contact US: help@patsnap.com