Preparation method of rolling bearing
A technology for rolling bearings and bearings, which is applied to bearings, bearing components, shafts and bearings, etc. It can solve the problems of non-optimal structure performance, not satisfying the shape of the bearing ring blank, and not being as good as the bearing steel blank, so as to avoid point contact fatigue damage , good comprehensive mechanical properties, the effect of improving hardness and wear resistance
- Summary
- Abstract
- Description
- Claims
- Application Information
AI Technical Summary
Problems solved by technology
Method used
Image
Examples
Embodiment Construction
[0040] Attached below Figure 1-6 Embodiments of the present invention are described.
[0041] A material preparation and processing method for a rolling bearing, comprising the steps of:
[0042] 1) Preparation of tube blank material for inner and outer rings of bearings: use medium frequency induction furnace to melt molten iron, the initial composition (%) of molten iron is: C: 3.4-3.7, Si: 1.3-1.7 (adjusted according to the required grade of ductile iron), Mn: 0.2 -0.7, Cr: 0.1-0.3, Cu≤0.8, S≤0.05, P≤0.05, Fe: balance.
[0043] 2) Inoculation and spheroidization treatment: Use ferrosilicon inoculants for ductile iron and nickel-magnesium, nickel-copper spheroidizers to make the final silicon content of molten iron reach 2.3-2.7%, and the residual magnesium content is about 0.04%; try to avoid rare earth during operation And the incorporation of titanium in order to obtain the highest spheroidization rate.
[0044] 3) Preparation of tube blank material for bearing cage: ...
PUM
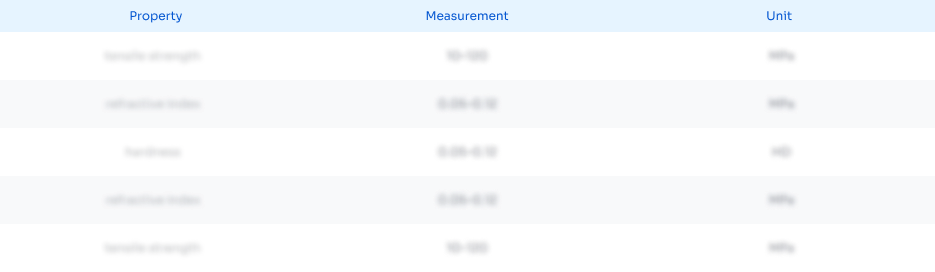
Abstract
Description
Claims
Application Information

- Generate Ideas
- Intellectual Property
- Life Sciences
- Materials
- Tech Scout
- Unparalleled Data Quality
- Higher Quality Content
- 60% Fewer Hallucinations
Browse by: Latest US Patents, China's latest patents, Technical Efficacy Thesaurus, Application Domain, Technology Topic, Popular Technical Reports.
© 2025 PatSnap. All rights reserved.Legal|Privacy policy|Modern Slavery Act Transparency Statement|Sitemap|About US| Contact US: help@patsnap.com