Preparation method capable of remarkably overcoming surface defect of copper alloy material for lead frame
A copper alloy and lead frame technology, which is applied in the field of significantly improving the preparation of copper alloy material surface defects for lead frames, can solve the problems of few varieties and specifications, small production scale, etc., and achieve the goal of improving surface properties, avoiding component segregation, and promoting migration Effect
- Summary
- Abstract
- Description
- Claims
- Application Information
AI Technical Summary
Problems solved by technology
Method used
Image
Examples
Embodiment 1
[0022] A preparation method for significantly improving surface defects of copper alloy materials for lead frames, comprising the steps of:
[0023] S1, adding high-purity copper and copper-iron alloy into a vacuum arc melting furnace for arc melting to obtain a copper-iron alloy with an iron content of 7%, wherein the high-purity copper is a copper block with blind holes, and the copper-iron alloy is put into copper before smelting in the blind hole of the block;
[0024] S2. Add high-purity copper and charcoal into the high-frequency induction melting furnace, heat up to complete melting to obtain copper liquid, continue to heat up to 1250°C, add S1 to obtain copper-iron alloy, copper-zinc alloy, and copper-phosphorus with an iron content of 7%. Alloys, copper-tin alloys, copper-titanium alloys, and mixed rare earths are stirred and smelted to obtain copper alloy solutions;
[0025] S3, detect the component of copper alloy solution, it comprises by weight percentage: Fe: 0....
Embodiment 2
[0029] A preparation method for significantly improving surface defects of copper alloy materials for lead frames, comprising the steps of:
[0030] S1, high-purity copper and iron content are that 25% copper-iron alloy is added in the vacuum electric arc melting furnace and carry out electric arc melting 4 times, and single smelting time is 15min, obtains the copper-iron alloy that iron content is 7%, wherein, high-purity copper is designed For copper blocks with blind holes, put the copper-iron alloy into the blind holes of the copper blocks before smelting;
[0031] S2. Add high-purity copper and charcoal into the high-frequency induction melting furnace, heat up to complete melting to obtain copper liquid, continue to heat up to 1300°C, add S1 to obtain copper-iron alloy, copper-zinc alloy, and copper-phosphorus with an iron content of 7%. Alloy, copper-tin alloy, copper-titanium alloy, Ce, Rd, stirring and melting to obtain copper alloy solution;
[0032] S3, detect the ...
Embodiment 3
[0036] A preparation method for significantly improving surface defects of copper alloy materials for lead frames, comprising the steps of:
[0037] S1, adding high-purity copper and iron content to 40% copper-iron alloy in a vacuum arc melting furnace for arc melting 5 times, a single smelting time is 10min, to obtain a copper-iron alloy with an iron content of 7%, wherein the high-purity copper is designed For copper blocks with blind holes, put the copper-iron alloy into the blind holes of the copper blocks before smelting;
[0038] S2. Add high-purity copper and charcoal into the high-frequency induction melting furnace, heat up to complete melting to obtain copper liquid, continue to heat up to 1270°C, add S1 to obtain copper-iron alloy, copper-zinc alloy, and copper-phosphorus with an iron content of 7%. Alloy, copper-tin alloy, copper-titanium alloy, Ce, Y, stirring and smelting to obtain copper alloy solution;
[0039] S3, detect the component of copper alloy solution...
PUM
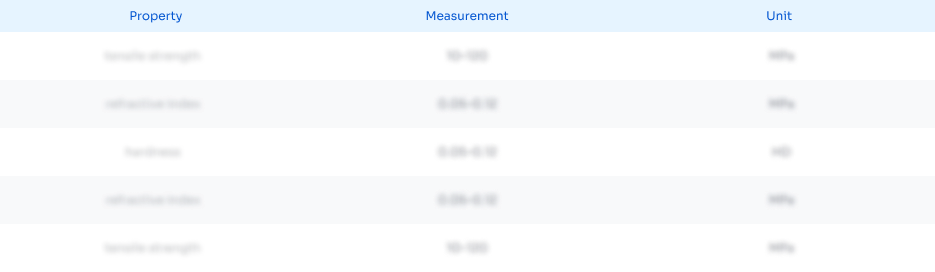
Abstract
Description
Claims
Application Information

- R&D
- Intellectual Property
- Life Sciences
- Materials
- Tech Scout
- Unparalleled Data Quality
- Higher Quality Content
- 60% Fewer Hallucinations
Browse by: Latest US Patents, China's latest patents, Technical Efficacy Thesaurus, Application Domain, Technology Topic, Popular Technical Reports.
© 2025 PatSnap. All rights reserved.Legal|Privacy policy|Modern Slavery Act Transparency Statement|Sitemap|About US| Contact US: help@patsnap.com