Method for recycling zinc, copper and cadmium from zinc hydrometallurgy copper-cadmium residues
A technology for hydrometallurgical smelting of zinc and copper-cadmium slag, applied in the fields of copper, zinc and cadmium recovery, can solve the problems of cumbersome pyrometallurgical recovery process, reduced recovery rate of metal zinc and cadmium, unfavorable copper smelting stability, etc. Value, improve the efficiency of electrolysis, the effect of low production cost
- Summary
- Abstract
- Description
- Claims
- Application Information
AI Technical Summary
Problems solved by technology
Method used
Examples
Embodiment 1
[0026] Under the conditions of 100g / L sulfuric acid, 5% hydrogen peroxide, liquid / solid=4, and 80°C, the copper-cadmium slag containing 25% zinc, 5% cadmium, and 0.3% copper was leached once to obtain a leach solution containing 82.5g / L zinc, cadmium 15.2g / L, copper 750mg / L, sulfuric acid 52.1g / L, Fe 3+ 1.2g / L, neutralize with milk of lime until the pH value is 4.5 and filter to obtain a neutralized solution containing 80.7g / L zinc, 14.5g / L cadmium, 720mg / L copper, and Fe2 , 25°C, electrolysis of zinc-copper-cadmium alloy under the conditions of electrolyte circulation rate 1.5L / h; electrolysis time 24 hours, current efficiency 81.3%, electrolytic raffinate contains zinc 43.5g / L, cadmium 0.2g / L, copper trace , sulfuric acid 120g / L; the alloy obtained by electrolysis contains 92.5% of zinc, 7.1% of cadmium, 0.25% of copper, 0.15% of lead, iron, arsenic and antimony in total.
Embodiment 2
[0028] Carry out pressure with the copper cadmium slag of example 1 in sulfuric acid 150g / L, liquid / solid=3, 150 DEG C of conditions and be 7.5kg grade high-pressure oxygen leaching, obtain the first grade leach solution containing zinc 95.3g / L, cadmium 16.5g / L, Copper 872mg / L, Fe 3+ 1.5g / L, neutralized with lime to pH 4, and obtained a neutralized solution containing zinc 92.1g / L, cadmium 15.8g / L, copper 850mg / L, Fe<100mg / L, filtered and pressed at a tank pressure of 3.5 V, current density 500A / m2, 35°C, electrolysis of zinc-copper-cadmium alloy under the conditions of electrolyte circulation speed 2L / hour, to obtain zinc-copper-cadmium alloy containing 90.5% zinc, 8.2% cadmium, 0.3% copper, lead, iron, The total of arsenic and antimony is 1%.
Embodiment 3
[0030] Oxidative leaching is carried out according to the conditions of Example 1, and the secondary leaching solution is returned to the primary leaching to obtain a leaching solution containing 102g / L of zinc, 18.2g / L of cadmium, 970mg / L of copper, and 970mg / L of Fe. 3+ 1.8g / L; Lime milk is neutralized and electrolyzed to obtain a zinc-copper-cadmium alloy containing 93.5% zinc, 5.2% cadmium, 0.42% copper, and a total of 0.78% lead, iron, arsenic, and antimony.
PUM
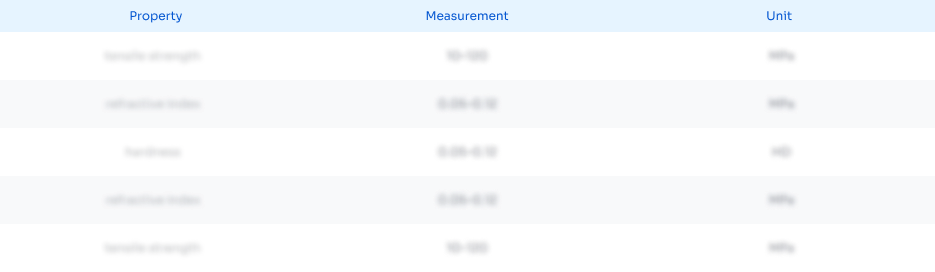
Abstract
Description
Claims
Application Information

- R&D
- Intellectual Property
- Life Sciences
- Materials
- Tech Scout
- Unparalleled Data Quality
- Higher Quality Content
- 60% Fewer Hallucinations
Browse by: Latest US Patents, China's latest patents, Technical Efficacy Thesaurus, Application Domain, Technology Topic, Popular Technical Reports.
© 2025 PatSnap. All rights reserved.Legal|Privacy policy|Modern Slavery Act Transparency Statement|Sitemap|About US| Contact US: help@patsnap.com