Leadless high-heat resistance glue solution for producing copper-clad plates
A high heat-resistant, copper-clad laminate technology, applied in the direction of layered products, lamination, lamination equipment, etc., can solve the problems of high production cost, insufficient toughness, low peel strength, etc., to achieve good product performance and reduce energy consumption , the effect of good machinability
- Summary
- Abstract
- Description
- Claims
- Application Information
AI Technical Summary
Problems solved by technology
Method used
Image
Examples
Embodiment 1
[0036] A preparation method of 4-(N-maleimide)phenol glycidyl ether containing imide ring epoxy monomer, the steps of which include:
[0037] a) Add 5.39 parts of maleic anhydride dissolved in acetone to a flask equipped with a constant pressure dropping funnel; add 8.6 parts by mass of p-bromoaniline dissolved in an appropriate amount of acetone into the constant pressure dropping funnel, and drip into the bottle at the temperature of ice water bath After the addition is complete, react at room temperature overnight; stop the reaction, filter with suction, collect the filter cake, and place it in a vacuum oven to dry to obtain the intermediate product N-(4-bromophenyl) maleamic acid.
[0038] b) Take 11.11 parts by mass of the dried product, appropriate amount of toluene and DMF, and 1.0 part by mass of p-toluenesulfonic acid into the reflux reaction device with a water trap, and raise the temperature to the reflux temperature of toluene; react for about 4h, The stoichiometric amo...
Embodiment 2
[0041] A preparation method of FR-4 copper clad laminate adapted to lead-free manufacturing process, the steps include:
[0042] materials
Solid content
Ratio
Low bromine
80%
75
High bromine
60%
16.7
Yellow material
70%
14.3
MPGE
100%
20
DICY
100%
2.5
2MI
100%
0.05
Silica
100%
30
KH560
--
0.8
[0043] Put the above-mentioned materials into the shearing kettle according to the ratio, and add the solvent DMF and acetone to adjust into a glue with a solid content of about 65%. The glue is formed at 283S / 171℃, and the viscosity is coated with four cups of 38S.
[0044] The cured sheet is made by impregnating the above glue with E-type glass fiber cloth, which is made into FR-4 copper clad sheet according to the common process in the industry. The main properties of the sheet are shown in Table 1.
Embodiment 3
1
[0047] Put the above-mentioned materials into the shearing kettle according to the proportion, and add the solvent DMF and methyl ethyl ketone to adjust into a glue with a solid content of about 63%. The glue is formed at 305S / 171℃, and the viscosity is coated with four cups of 33S.
[0048] The cured sheet is made by impregnating the above glue with E-type glass fiber cloth, which is made into FR-4 copper clad sheet according to the common process in the industry. The main properties of the sheet are shown in Table 1.
PUM
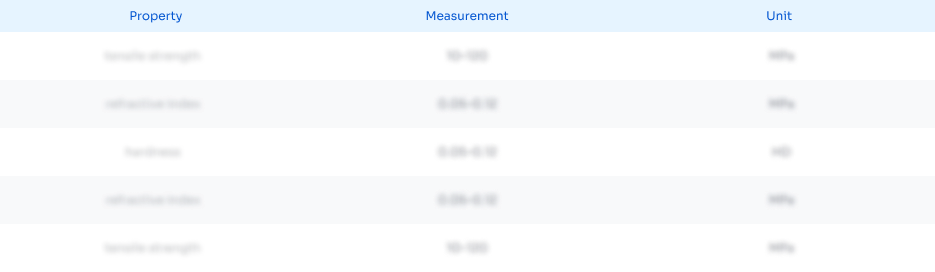
Abstract
Description
Claims
Application Information

- R&D
- Intellectual Property
- Life Sciences
- Materials
- Tech Scout
- Unparalleled Data Quality
- Higher Quality Content
- 60% Fewer Hallucinations
Browse by: Latest US Patents, China's latest patents, Technical Efficacy Thesaurus, Application Domain, Technology Topic, Popular Technical Reports.
© 2025 PatSnap. All rights reserved.Legal|Privacy policy|Modern Slavery Act Transparency Statement|Sitemap|About US| Contact US: help@patsnap.com