A permanent ferrite sintered magnet injection molding pellets and its preparation and application
A permanent magnet ferrite, sintered magnet technology, applied in the direction of inductor/transformer/magnet manufacturing, magnetic objects, magnetic materials, etc., to achieve the effect of improving dispersion uniformity, low viscosity, and improving bending deformation
- Summary
- Abstract
- Description
- Claims
- Application Information
AI Technical Summary
Problems solved by technology
Method used
Image
Examples
Embodiment 1
[0029] The components and volume fractions of the pellets are as follows:
[0030]
[0031] Wherein: the volume fraction of each component of the modified wax matrix is as follows:
[0032] Carnauba Wax 70%
[0034] Microcrystalline Wax 5%
[0035] According to the above formula, mix carnauba wax (8015-86-9), polyamide wax (NEW-0404) and microcrystalline wax (No. 80) at 100°C to obtain modified wax matrix particles; High-density polyethylene (8050), modified wax matrix, stearic acid (57-11-4) and strontium ferrite powder are mixed evenly, and then extruded and granulated in a twin-screw extruder to obtain mixed feed. The rotational speed is 20rad / s, the rotational speed of the feeder is 16rad / s, and the temperature of the extruder is 130, 130, 135, 140, 140°C from the feed port to the discharge port. Injection-molding the prepared pellets on an injection-molding machine to obtain an injection-molded green body of a sintered magnet. The inje...
Embodiment 2
[0037] The components and volume fractions of the pellets are as follows:
[0038]
[0039]
[0040] Wherein: the volume fraction of each component of the modified wax matrix is as follows:
[0041] Carnauba Wax 70%
[0043] Microcrystalline Wax 5%
[0044]According to the above formula, mix carnauba wax (8015-86-9), polyamide wax (NEW-0404) and microcrystalline wax (No. 80) at 100°C to obtain modified wax matrix particles; High-density polyethylene (8050), modified wax matrix, stearic acid (57-11-4) and strontium ferrite powder are mixed evenly, and then extruded and granulated in a twin-screw extruder to obtain mixed feed. The rotational speed is 20rad / s, the rotational speed of the feeder is 16rad / s, and the temperature of the extruder is 130, 130, 135, 140, 140°C from the feed port to the discharge port. Injection-molding the prepared pellets on an injection-molding machine to obtain an injection-molded green body of a sintered magnet...
Embodiment 3
[0046] The components and volume fractions of the pellets are as follows:
[0047]
[0048] Wherein: the volume fraction of each component of the modified wax matrix is as follows:
[0049] Carnauba Wax 70%
[0050] Polyamide Wax 25%
[0051] Microcrystalline Wax 5%
[0052] According to the above formula, mix carnauba wax (8015-86-9), polyamide wax (NEW-0404) and microcrystalline wax (No. 80) at 100°C to obtain modified wax matrix particles; High-density polyethylene (8050), modified wax matrix, stearic acid (57-11-4) and strontium ferrite powder are mixed evenly, and then extruded and granulated in a twin-screw extruder to obtain mixed feed. The rotational speed is 20rad / s, the rotational speed of the feeder is 16rad / s, and the temperature of the extruder is 130, 130, 135, 140, 140°C from the feed port to the discharge port. Injection-molding the prepared pellets on an injection-molding machine to obtain an injection-molded green body of a sintered magnet. The inje...
PUM
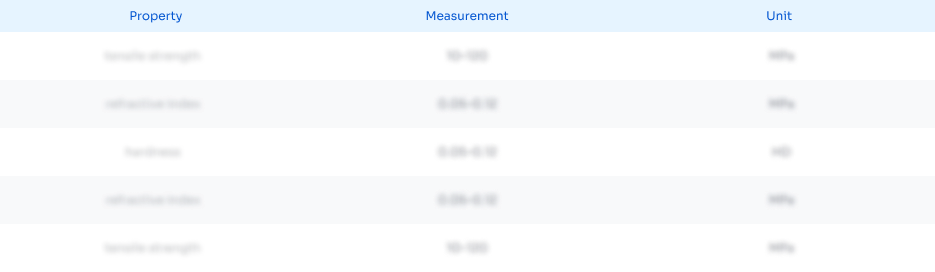
Abstract
Description
Claims
Application Information

- R&D
- Intellectual Property
- Life Sciences
- Materials
- Tech Scout
- Unparalleled Data Quality
- Higher Quality Content
- 60% Fewer Hallucinations
Browse by: Latest US Patents, China's latest patents, Technical Efficacy Thesaurus, Application Domain, Technology Topic, Popular Technical Reports.
© 2025 PatSnap. All rights reserved.Legal|Privacy policy|Modern Slavery Act Transparency Statement|Sitemap|About US| Contact US: help@patsnap.com