Method for improving high temperature oxidation resistance of titanium-based alloy on basis of halide effect and ceramic coating obtained through pretreatment
A technology for resisting high temperature oxidation and titanium-based alloys, applied in electrolytic inorganic material coating and other directions, can solve the problems of expensive equipment, low production efficiency, decreased mechanical properties of TiAl alloys, etc., and achieve the effects of simple preparation process, convenient operation and easy realization.
- Summary
- Abstract
- Description
- Claims
- Application Information
AI Technical Summary
Problems solved by technology
Method used
Image
Examples
Embodiment 1
[0031] First, polish the titanium-aluminum alloy sample (the atomic ratio of titanium to aluminum is 1:1) with sandpaper to remove surface oxides, and then ultrasonically clean it in acetone and ethanol for 10 minutes, and finally dry it with hot air for use. Add 1 mol of ammonia acetate, 0.1 mol of ammonium chloride, 0.2 mol of ammonium hexafluorosilicate, and 100 mL of water to the beaker in turn, and stir for 40 hours at room temperature for later use. The polished and cleaned titanium aluminum alloy sample (the atomic ratio of titanium to aluminum is 1:1) is used as the cathode, the graphite electrode is used as the counter electrode, the Ag / AgCl electrode is used as the reference electrode, the electrode spacing is controlled at 1cm, and the deposition potential is controlled at -1V , The deposition time is 1500s, after the deposition is completed, the working electrode is rinsed with deionized water and then dried at 40℃ to obtain F-containing micro-nano SiO 2 coating. Su...
Embodiment 2
[0035] First use sandpaper to polish the titanium-aluminum alloy sample (the atomic ratio of titanium to aluminum is 3:1) to remove surface oxides, and then ultrasonically clean it in acetone and ethanol for 10 minutes, and finally dry it with hot air for use. Add 2 mol of ammonia acetate, 0.15 mol of ammonium chloride, 0.2 mol of potassium hexafluorosilicate, and 100 mL of water to the beaker in turn, and stir at room temperature for 40 hours until use. The polished and cleaned titanium aluminum alloy sample (the atomic ratio of titanium to aluminum is 3:1) is used as the cathode, the graphite electrode is used as the counter electrode, the Ag / AgCl electrode is used as the reference electrode, the electrode spacing is controlled at 10cm, and the deposition voltage is controlled at -3.0 V, the deposition time is 500s. After the deposition is completed, the working electrode is rinsed with deionized water and dried at 150°C to obtain F-containing micro-nano SiO 2 coating. Subseq...
Embodiment 3
[0039] First use sandpaper to polish the titanium-aluminum alloy sample (the atomic ratio of titanium to aluminum is 3:1) to remove surface oxides, and then ultrasonically clean it in acetone and ethanol for 10 minutes, and finally dry it with hot air for use. Add 2 mol of ammonia acetate, 0.15 mol of ammonium chloride, 0.1 mol of ammonium hexafluorosilicate, 0.1 mol of potassium hexafluorosilicate, and 100 mL of water to the beaker in turn, and stir at room temperature for 20 hours until use. The polished and cleaned titanium-aluminum alloy sample (the atomic ratio of titanium to aluminum is 3:1) is used as the cathode, the graphite electrode is used as the counter electrode, the Ag / AgCl electrode is used as the reference electrode, the electrode spacing is controlled at 5cm, and the deposition potential is controlled at -3.0V , The deposition time is 500s, after the deposition is completed, the working electrode is rinsed with deionized water and dried at 150°C to obtain F-con...
PUM
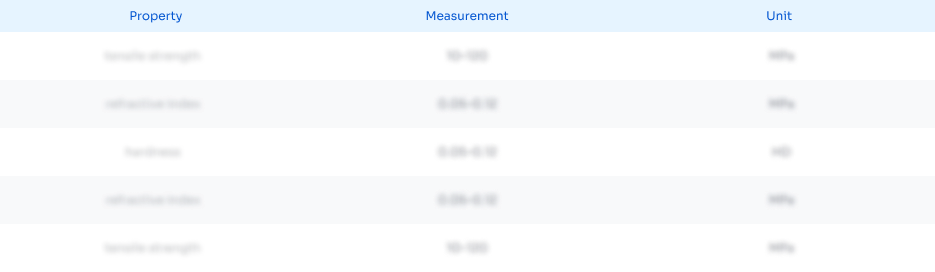
Abstract
Description
Claims
Application Information

- R&D
- Intellectual Property
- Life Sciences
- Materials
- Tech Scout
- Unparalleled Data Quality
- Higher Quality Content
- 60% Fewer Hallucinations
Browse by: Latest US Patents, China's latest patents, Technical Efficacy Thesaurus, Application Domain, Technology Topic, Popular Technical Reports.
© 2025 PatSnap. All rights reserved.Legal|Privacy policy|Modern Slavery Act Transparency Statement|Sitemap|About US| Contact US: help@patsnap.com