High linearity millimeter-wave device and manufacturing method thereof
A high-linearity, millimeter-wave technology, applied in the field of microelectronics, can solve the problems of increased influence of frequency characteristics of parasitic capacitor devices, decreased gate control ability, and poor gate support, so as to improve frequency characteristics, improve linearity, Effect of reducing square resistance and contact resistance
- Summary
- Abstract
- Description
- Claims
- Application Information
AI Technical Summary
Problems solved by technology
Method used
Image
Examples
Embodiment 1
[0037] Embodiment 1: On a sapphire substrate, the groove width is 0.2 μm, the groove etching depth is 35 nm, the barrier layer is an AlGaN layer with a thickness of 3 nm, the thickness of the enhanced channel region is 2 nm, and the thickness of the conductive cap layer is 10nm high linearity millimeter wave device.
[0038] In step 1, an AlN nucleation layer is grown on a sapphire substrate by MOCVD process.
[0039] First lower the temperature of the sapphire substrate to 500°C, keep the growth pressure at 40Torr, the flow rate of hydrogen gas at 1000sccm, the flow rate of ammonia gas at 600sccm, feed the aluminum source with a flow rate of 4sccm into the reaction chamber, and grow a sapphire substrate with a thickness of 5nm. Low temperature AlN layer;
[0040]Then increase the growth temperature to 940°C, keep the growth pressure at 40 Torr, the flow rate of hydrogen gas at 1000 sccm, the flow rate of ammonia gas at 1000 sccm, feed the aluminum source with a flow rate of ...
Embodiment 2
[0113] Embodiment 2, the groove width is 1 μm on the SiC substrate, the groove etching depth is 120nm, the barrier layer is an AlGaN layer with a thickness of 50nm, the thickness of the enhanced channel region is 10nm, and the thickness of the conductive cap layer is 30nm high linearity millimeter wave device.
[0114] In step 1, an AlN nucleation layer is grown on the SiC substrate by using the MOCVD process.
[0115] First lower the temperature of the SiC substrate to 650°C, keep the growth pressure at 100Torr, the flow rate of hydrogen gas at 5000 sccm, the flow rate of ammonia gas at 3000 sccm, and feed the aluminum source with a flow rate of 20 sccm into the reaction chamber to grow a 10nm-thick film on the SiC substrate. Low temperature AlN layer;
[0116] Then increase the growth temperature to 1050°C, keep the growth pressure at 100 Torr, the flow rate of hydrogen gas at 5000 sccm, the flow rate of ammonia gas at 3000 sccm, feed the aluminum source with a flow rate of...
Embodiment 3
[0160] Embodiment 3, on the sapphire substrate, the groove width is 0.2 μm, the groove etching depth is 35nm, the barrier layer is an InAlN layer, the thickness is 3nm, the thickness of the enhanced channel region is 2nm, and the thickness of the conductive cap layer is 10nm high linearity millimeter wave device.
[0161] In step A, an AlN nucleation layer is grown on the sapphire substrate by MOCVD process.
[0162] The specific implementation of this step is the same as step 1 in the first embodiment.
[0163] Step B, growing a GaN buffer layer on the AlN nucleation layer.
[0164] The specific implementation of this step is the same as step 2 in the first embodiment.
[0165] Step C, growing a second channel region on the buffer layer.
[0166] The specific implementation of this step is the same as step 3 in the first embodiment.
[0167] Step D, growing a back barrier layer on the second channel region.
[0168] The specific implementation of this step is the same as...
PUM
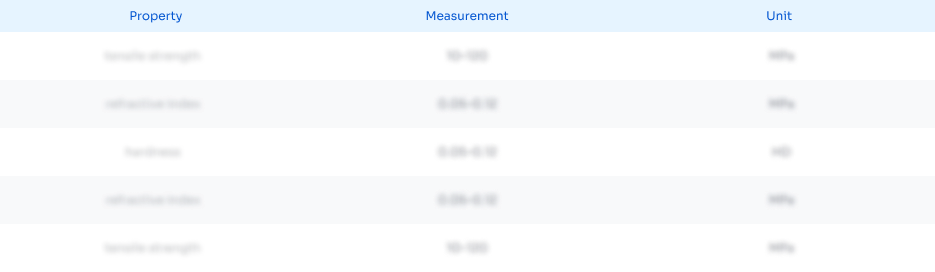
Abstract
Description
Claims
Application Information

- Generate Ideas
- Intellectual Property
- Life Sciences
- Materials
- Tech Scout
- Unparalleled Data Quality
- Higher Quality Content
- 60% Fewer Hallucinations
Browse by: Latest US Patents, China's latest patents, Technical Efficacy Thesaurus, Application Domain, Technology Topic, Popular Technical Reports.
© 2025 PatSnap. All rights reserved.Legal|Privacy policy|Modern Slavery Act Transparency Statement|Sitemap|About US| Contact US: help@patsnap.com