Al2O3-MgO-SiAlON common steel heat treatment anti-oxidation coating and use method thereof
A technology for anti-oxidation coatings and ordinary steel, applied in the direction of fire-proof coatings, coatings, etc., can solve the problems of poor chemical stability, easy cracking and falling off, etc., achieve low thermal expansion rate, not easy cracking and falling off, and reduce oxidation burning.
- Summary
- Abstract
- Description
- Claims
- Application Information
AI Technical Summary
Problems solved by technology
Method used
Examples
Embodiment 1
[0032] a kind of Al2 o 3 - MgO-SiAlON common steel heat treatment anti-oxidation coating, is made up of the raw material of following weight part: Al 2 o 3 -MgO-SiAlON powder 30 parts, Cr 2 o 3 3 parts, 20 parts of composite binder, 0.5 parts of potassium fluoroborate, 0.5 parts of boron carbide, and the particle size of the above components is 300 mesh.
[0033] where Al 2 o 3 -MgO-SiAlON powder is prepared by the following method:
[0034] (1) The weight parts are respectively 20 parts of corundum, 14 parts of MgO powder, 10 parts of pinnacle and 6 parts of β-SiAlON powder. The mass ratio of base material and dehydrated alcohol is 1.5: 1;
[0035] (2) Dry the mixture after ball milling in step (1) at 50°C, and then dry mix for 30 minutes;
[0036] (3) The dry-blended mixture was pressed into shape with a pressure of 50 MPa, firstly baked at 150°C for 4 hours, then placed in a microwave high-temperature atmosphere furnace, kept at 1400°C for 3 hours under the conditio...
Embodiment 2
[0045] a kind of Al 2 o 3 - MgO-SiAlON common steel heat treatment anti-oxidation coating, is made up of the raw material of following weight part: Al 2 o 3 -MgO-SiAlON powder 40 parts, Cr 2 o 3 4 parts, 25 parts of composite binder, 1 part of potassium fluoroborate, 1 part of boron carbide, the particle size of each of the above components is 400 mesh.
[0046] where Al 2 o 3 -MgO-SiAlON powder is prepared by the following method:
[0047] (1) The base material which is uniformly mixed with 25 parts of corundum, 17 parts of MgO powder, 15 parts of pinnacle and 10 parts of β-SiAlON powder in parts by weight is placed in a ball mill jar and ball milled for 4 hours with absolute ethanol as the medium, wherein The mass ratio of base material and dehydrated alcohol is 1.7: 1;
[0048] (2) Dry the mixture after ball milling in step (1) at 600°C, and then dry mix for 35 minutes;
[0049] (3) The dry-blended mixture was pressed into shape with a pressure of 50MPa, firstly ba...
Embodiment 3
[0058] a kind of Al 2 o 3 - MgO-SiAlON common steel heat treatment anti-oxidation coating, is made up of the raw material of following weight part: Al 2 o 3 -50 parts of MgO-SiAlON powder, Cr 2 o 3 5 parts, 30 parts of composite binder, 1.5 parts of potassium fluoroborate, 1.5 parts of boron carbide, and the particle size of the above components is 500 mesh.
[0059] where Al 2 o 3 -MgO-SiAlON powder is prepared by the following method:
[0060] (1) 30 parts by weight of corundum, 20 parts of MgO powder, 20 parts of pinnacle and 12 parts of β-SiAlON are mixed uniformly. The powder is placed in a ball mill jar and ball milled for 5 hours with absolute ethanol as the medium. The mass ratio of base material and dehydrated alcohol is 2: 1;
[0061] (2) Dry the mixture after ball milling in step (1) at 80°C, and then dry mix for 40 minutes;
[0062] (3) The dry-blended mixture was pressed into shape with a pressure of 60MPa, firstly baked at 180°C for 6h, then placed in a ...
PUM
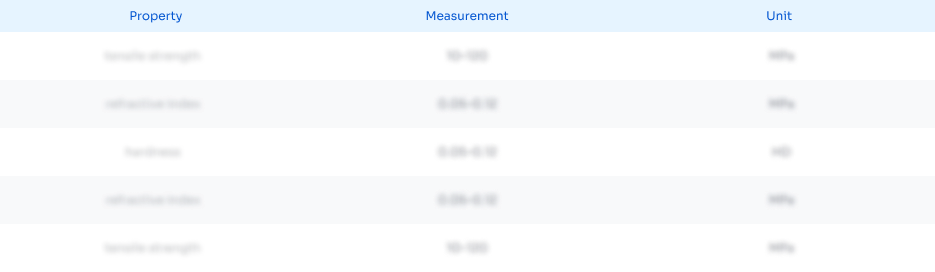
Abstract
Description
Claims
Application Information

- R&D
- Intellectual Property
- Life Sciences
- Materials
- Tech Scout
- Unparalleled Data Quality
- Higher Quality Content
- 60% Fewer Hallucinations
Browse by: Latest US Patents, China's latest patents, Technical Efficacy Thesaurus, Application Domain, Technology Topic, Popular Technical Reports.
© 2025 PatSnap. All rights reserved.Legal|Privacy policy|Modern Slavery Act Transparency Statement|Sitemap|About US| Contact US: help@patsnap.com