Method for manufacturing microtexture friction surface through photoetching
A friction surface and micro-texture technology, which is applied in the field of photolithography and etching to manufacture micro-texture friction surfaces, can solve the problems of different etching processes and no guiding specifications, etc., and achieve great application value, easy processing, and pattern resolution high rate effect
- Summary
- Abstract
- Description
- Claims
- Application Information
AI Technical Summary
Problems solved by technology
Method used
Image
Examples
Embodiment 1
[0024] Preheat the Q235 cast iron sheet at 100°C for 5 minutes; drop S1813 photoresist on the surface of the cast iron sheet material, then place the material in a spin coater, fix it on a vacuum chuck, and place it in a nitrogen protective atmosphere , rotate at 300rpm for 10s, 900rpm for 10s, and 4000rpm for 60s; pre-bake the obtained material at 110°C for 4min; cover the friction surface with a circular hole template with a diameter of 5mm, and the part that needs texture is a light-transmitting layer, and the rest It is a black light-absorbing layer; expose the friction surface covering the template to 365nm ultraviolet light for 10 minutes; then remove the template, and bake the obtained material at 120°C for 8 minutes; soak the material in a solution of tetramethylammonium hydroxide with a mass concentration of 2%. 2min, rinse in deionized water for 30s; then place it in an environment of 110°C for drying; put the material in a dilute nitric acid solution with a mass conc...
Embodiment 2
[0026] Preheat SAE1020 steel at 110°C for 3 minutes; drop S1813 photoresist on the surface of the cast iron sheet material, then place the material in a spin coater, fix it on a vacuum chuck, and in a nitrogen protective atmosphere, Rotate at 300rpm for 10s, 1000rpm for 10s, and 4000rpm for 60s; pre-bake the obtained material at 120°C for 3min; cover the elliptical (long axis 1.8mm, short axis 0.6mm) hole template on the friction surface, where texture is required Part of it is a light-transmitting layer, and the rest is a black light-absorbing layer; expose the friction surface covering the template to 365nm ultraviolet light for 20 minutes; then remove the template, and bake the obtained material at 125°C for 6 minutes; Soak in methyl ammonium hydroxide solution for 2min, rinse in deionized water for 40s; then place it in an environment of 110°C for drying; put the material in a dilute phosphoric acid solution with a mass concentration of 3% for 4min at 25°C, Take it out and...
Embodiment 3
[0028] Preheat 45 steel at 120°C for 6 minutes; drop S1813 photoresist on the surface of the cast iron sheet material, then place the material in a spin coater, fix it on a vacuum chuck, and in a nitrogen protective atmosphere, Rotate at 300rpm for 10s, 1100rpm for 10s, and 4000rpm for 60s; pre-bake the obtained material at 120°C for 2 minutes; cover the circular hole template with a diameter of 2 microns on the friction surface, and the part that needs texture is a light-transmitting layer, and the rest It is a black light-absorbing layer; expose the friction surface covering the template to 365nm ultraviolet light for 15 minutes; then remove the template, and bake the obtained material at 130°C for 6 minutes; soak the material in a solution of tetramethylammonium hydroxide with a mass concentration of 4%. 2min, rinse in deionized water for 60s; then put it into 120°C environment for drying; put the material into a dilute sulfuric acid solution with a mass concentration of 4% ...
PUM
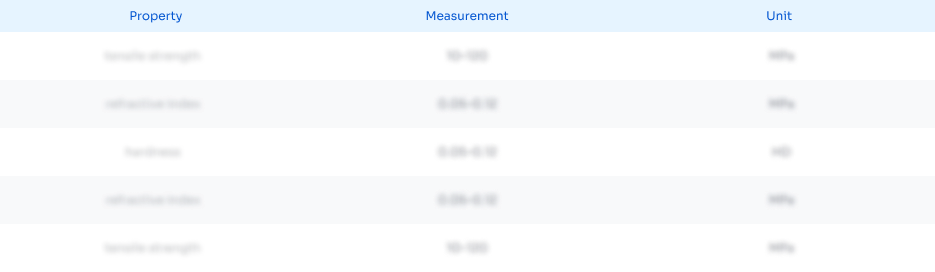
Abstract
Description
Claims
Application Information

- Generate Ideas
- Intellectual Property
- Life Sciences
- Materials
- Tech Scout
- Unparalleled Data Quality
- Higher Quality Content
- 60% Fewer Hallucinations
Browse by: Latest US Patents, China's latest patents, Technical Efficacy Thesaurus, Application Domain, Technology Topic, Popular Technical Reports.
© 2025 PatSnap. All rights reserved.Legal|Privacy policy|Modern Slavery Act Transparency Statement|Sitemap|About US| Contact US: help@patsnap.com