Method for producing flexible cable
A flexible cable and copper single technology, applied in the direction of insulated cables, cable/conductor manufacturing, heat treatment equipment, etc. , single sheath performance, performance needs to be improved, etc., to achieve excellent flame retardancy and good electrical performance
- Summary
- Abstract
- Description
- Claims
- Application Information
AI Technical Summary
Problems solved by technology
Method used
Examples
Embodiment 1
[0025] A method for producing a flexible cable, comprising the steps of:
[0026] 1) drawing and annealing the copper monofilament;
[0027] 2) twisting a plurality of copper monofilaments;
[0028] 3) 1 to 2 parts by weight of hydroxyl polyphosphate, 1.3 parts by weight of alkylphenol polyoxyethylene ether, 1.6 parts by weight of γ-(methacryloyloxy)propyl trimethoxysilane, 1.5 parts by weight of sorbitan Fatty acid esters, 0.6 parts by weight of limestone powder, 0.9 parts by weight of titanium oxide, 0.8 parts by weight of phenothiazine, 1.1 parts by weight of ammonium fluorotitanate, 2.5 parts by weight of diethylhexyl carbonate, and 16.6 parts by weight of polypropylene resin are put into extrusion Machine blending extrusion, coated conductor.
Embodiment 2
[0030] A method for producing a flexible cable, comprising the steps of:
[0031] 1) drawing and annealing the copper monofilament;
[0032] 2) twisting a plurality of copper monofilaments;
[0033] 3) 1 part by weight of hydroxyl polyphosphate, 1.3 parts by weight of alkylphenol polyoxyethylene ether, 1.6 parts by weight of γ-(methacryloyloxy)propyl trimethoxysilane, 1.5 parts by weight of sorbitan fatty acid Esters, 0.6 parts by weight of limestone powder, 0.9 parts by weight of titanium oxide, 0.8 parts by weight of phenothiazine, 1.1 parts by weight of ammonium fluorotitanate, 2.5 parts by weight of diethylhexyl carbonate, and 16.6 parts by weight of polypropylene resin were put into the extruder Mixed extrusion, coated conductor.
Embodiment 3
[0035] A method for producing a flexible cable, comprising the steps of:
[0036] 1) drawing and annealing the copper monofilament;
[0037] 2) twisting a plurality of copper monofilaments;
[0038] 3) 2 parts by weight of hydroxyl polyphosphate, 1.3 parts by weight of alkylphenol polyoxyethylene ether, 1.6 parts by weight of γ-(methacryloxy)propyltrimethoxysilane, 1.5 parts by weight of sorbitan fatty acid Esters, 0.6 parts by weight of limestone powder, 0.9 parts by weight of titanium oxide, 0.8 parts by weight of phenothiazine, 1.1 parts by weight of ammonium fluorotitanate, 2.5 parts by weight of diethylhexyl carbonate, and 16.6 parts by weight of polypropylene resin were put into the extruder Mixed extrusion, coated conductor.
PUM
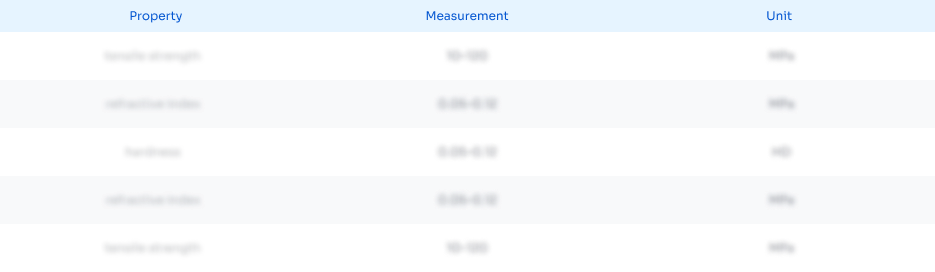
Abstract
Description
Claims
Application Information

- Generate Ideas
- Intellectual Property
- Life Sciences
- Materials
- Tech Scout
- Unparalleled Data Quality
- Higher Quality Content
- 60% Fewer Hallucinations
Browse by: Latest US Patents, China's latest patents, Technical Efficacy Thesaurus, Application Domain, Technology Topic, Popular Technical Reports.
© 2025 PatSnap. All rights reserved.Legal|Privacy policy|Modern Slavery Act Transparency Statement|Sitemap|About US| Contact US: help@patsnap.com