A kind of graphene composite cable material and preparation method thereof
A graphene composite and cable material technology, which is applied in the direction of insulating cables, cables, circuits, etc., can solve problems such as poor environmental protection performance, and achieve the effect of being suitable for large-scale industrial applications, good application prospects, and strong practicability
- Summary
- Abstract
- Description
- Claims
- Application Information
AI Technical Summary
Problems solved by technology
Method used
Image
Examples
Embodiment 1
[0024] (1) Weigh 30 parts of polyimide emulsion, 25 parts of modified montmorillonite, 20 parts of high-density polyethylene, 15 parts of polyethylene naphthalate, 10 parts of silane coupling agent KH-550, sulfur 10 parts of powder, 8 parts of titanium diboride, 8 parts of glass fiber, 7 parts of citrate, 5 parts of graphene, 5 parts of choline alfoscerate, di(3,4-dimethyl)benzyl sorbitol 2 parts, 3 parts of fatty alcohol polyoxyethylene ether, 3 parts of antioxidant MBZ;
[0025] (2) Add an appropriate amount of water to graphene, titanium diboride, and glass fiber, grind for 3 hours to obtain a 450-mesh slurry, and spray dry to obtain a powder. The air inlet temperature of the spray dryer is 250°C, and the air outlet temperature is 180°C;
[0026] (3) Add nitric acid to the powder, react for 5 minutes, dry it and send it to the mixer, then add polyimide emulsion, modified montmorillonite, high-density polyethylene, polyethylene naphthalate Alcohol esters were mixed for 25 m...
Embodiment 2
[0032] (1) Weigh 33 parts of polyimide emulsion, 30 parts of modified montmorillonite, 25 parts of high-density polyethylene, 20 parts of polyethylene naphthalate, 15 parts of silane coupling agent KH-550, sulfur 12 parts of powder, 10 parts of titanium diboride, 10 parts of glass fiber, 9 parts of citrate, 7 parts of graphene, 7 parts of choline alfoscerate, di(3,4-dimethyl) benzyl sorbitol 4 parts, 4 parts of dimethyl sulfoxide, 4 parts of antioxidant RD;
[0033] (2) Add an appropriate amount of water to graphene, titanium diboride, and glass fiber, grind for 4 hours to obtain a 500-mesh slurry, and spray dry to obtain a powder. The air inlet temperature of the spray dryer is 250°C, and the air outlet temperature is 180°C;
[0034] (3) Add nitric acid to the powder, react for 10 minutes, dry it and send it to the mixer, then add polyimide emulsion, modified montmorillonite, high-density polyethylene, polyethylene naphthalate Alcohol esters were mixed for 28 minutes at a te...
Embodiment 3
[0040](1) Weigh 35 parts of polyimide emulsion, 35 parts of modified montmorillonite, 30 parts of high-density polyethylene, 25 parts of polyethylene naphthalate, 20 parts of silane coupling agent KH-550, sulfur 15 parts of powder, 12 parts of titanium diboride, 12 parts of glass fiber, 10 parts of citrate, 8 parts of graphene, 8 parts of choline alfoscerate, di(3,4-dimethyl) benzyl sorbitol 5 parts, 5 parts of coconut acid diethanolamide, 5 parts of anti-aging agent NBC;
[0041] (2) Add an appropriate amount of water to graphene, titanium diboride, and glass fiber, grind for 5 hours to obtain a 550-mesh slurry, and spray dry to obtain a powder. The air inlet temperature of the spray dryer is 250°C, and the air outlet temperature is 180°C;
[0042] (3) Add nitric acid to the powder, react for 15 minutes, dry it and send it to the mixer, then add polyimide emulsion, modified montmorillonite, high-density polyethylene, polyethylene naphthalate Alcohol esters were mixed for 30 ...
PUM
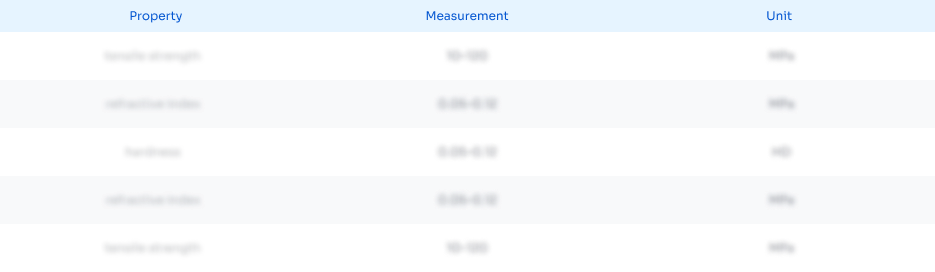
Abstract
Description
Claims
Application Information

- Generate Ideas
- Intellectual Property
- Life Sciences
- Materials
- Tech Scout
- Unparalleled Data Quality
- Higher Quality Content
- 60% Fewer Hallucinations
Browse by: Latest US Patents, China's latest patents, Technical Efficacy Thesaurus, Application Domain, Technology Topic, Popular Technical Reports.
© 2025 PatSnap. All rights reserved.Legal|Privacy policy|Modern Slavery Act Transparency Statement|Sitemap|About US| Contact US: help@patsnap.com