Preparation method of ceramic capacitor
A technology of ceramic capacitors and ceramics, applied in the field of electronic equipment, can solve problems such as inability to adapt to component miniaturization, poor capacitor stability, and general withstand voltage characteristics, and achieve low production costs, excellent withstand voltage characteristics, and low equipment requirements.
- Summary
- Abstract
- Description
- Claims
- Application Information
AI Technical Summary
Problems solved by technology
Method used
Examples
Embodiment 1
[0020] A method for preparing a ceramic capacitor, comprising the steps of:
[0021] 1) MnCO 3 : 3%, CuO: 5%, SiO 2 : 10%, and the balance is BaTiO 3 Wet grind evenly, grind finely and then dry;
[0022] 2) mixing the dried ceramic composition in step 1) with a ceramic molding binder at a mass ratio of 9:1, stirring evenly, and die-casting to obtain a green body;
[0023] Among them, the binder for ceramic molding is composed of the following components by mass percentage: diatomite: 9%, silane coupling agent: 3%, polyvinyl butyral: 9%, sodium aluminate: 5%, acetic acid Ethyl ester: 7%, isopropanol: 13%, the balance is epoxy resin,
[0024] 3) The green body is degummed, sintered, and ultrasonically cleaned in sequence;
[0025] 4) Sorting, printing, reducing, testing and encapsulating the green body;
[0026] The debinding temperature is 400°C, the sintering temperature is 1430°C, and the sintering time is 4 hours.
Embodiment 2
[0028] A method for preparing a ceramic capacitor, comprising the steps of:
[0029] 1) MnO 2 : 12.6%, CuO: 15.5%, SiO 2 : 14%, Al 2 o 3 : 12% and the balance BaTiO 3 Wet grind evenly, grind finely and then dry;
[0030] 2) mixing the dried ceramic composition in step 1) with a ceramic molding binder in a mass ratio of 9:3, stirring evenly, and die-casting to obtain a green body;
[0031] Among them, the binder for ceramic molding is composed of the following components by mass percentage: diatomite: 8%, silane coupling agent: 2%, polyvinyl butyral: 8%, sodium aluminate: 4%, acetic acid Ethyl ester: 6%, isopropanol: 13%, and the balance is epoxy resin.
[0032] 3) The green body is degummed, sintered, and ultrasonically cleaned in sequence;
[0033] 4) Sorting, printing, reducing, testing and encapsulating the green body;
[0034] The debinding temperature is 400°C, the sintering temperature is 1430°C, and the sintering time is 3 hours.
Embodiment 3
[0036] A method for preparing a ceramic capacitor, comprising the steps of:
[0037] 1) MnO 2 : 5%, CuO: 9%, SiO 2 : 11%, Al 2 o 3 : 4% and the balance BaTiO 3 Wet grind evenly, grind finely and then dry;
[0038] 2) mixing the dried ceramic composition in step 1) with a ceramic molding binder in a mass ratio of 9:2, stirring evenly, and die-casting to obtain a green body;
[0039] Among them, the binder for ceramic molding is composed of the following components by mass percentage: diatomite: 10%, silane coupling agent: 4%, polyvinyl butyral: 11%, sodium aluminate: 8%, acetic acid Ethyl ester: 8%, isopropanol: 19%, the balance is epoxy resin,
[0040] 3) The green body is degummed, sintered, and ultrasonically cleaned in sequence;
[0041] 4) Sorting, printing, reducing, testing and encapsulating the green body;
[0042] The debinding temperature is 280°C, the sintering temperature is 1350°C, and the sintering time is 3 hours.
PUM
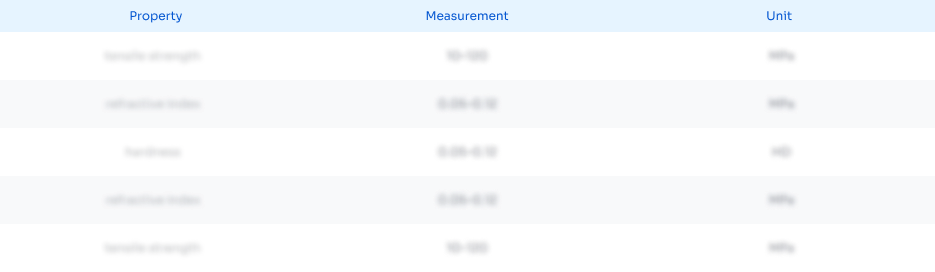
Abstract
Description
Claims
Application Information

- R&D
- Intellectual Property
- Life Sciences
- Materials
- Tech Scout
- Unparalleled Data Quality
- Higher Quality Content
- 60% Fewer Hallucinations
Browse by: Latest US Patents, China's latest patents, Technical Efficacy Thesaurus, Application Domain, Technology Topic, Popular Technical Reports.
© 2025 PatSnap. All rights reserved.Legal|Privacy policy|Modern Slavery Act Transparency Statement|Sitemap|About US| Contact US: help@patsnap.com