High-strength and high-toughness ceramic composite material and application thereof to manufacturing of cutter
A ceramic composite material, high-strength and high-toughness technology, applied in the field of composite materials, can solve the problems of high brittleness, poor self-lubrication, insufficient toughness, etc., achieve high hardness and wear resistance, simple and feasible preparation process, and not easy to break due to aging Effect
- Summary
- Abstract
- Description
- Claims
- Application Information
AI Technical Summary
Problems solved by technology
Method used
Examples
Embodiment 1
[0020] Embodiment 1: the preparation of ceramic composite material
[0021] Raw material weight ratio:
[0022] Zirconia, 60 parts; Aluminum oxide, 25 parts; Cerium oxide, 7 parts; Lanthanum oxide, 5 parts; Borax, 4 parts; Boron nitride, 2 parts; Zinc dialkyldithiophosphate, 3 parts; Alginic acid Sodium, 0.7 parts; Sodium lignosulfonate, 0.5 parts; Sodium hexametaphosphate, 1 part; Polyethylene glycol, 2 parts; Deionized water, 8 parts.
[0023] Preparation:
[0024] Step S1, mixing zirconia, aluminum oxide, cerium oxide, lanthanum oxide, borax and boron nitride, ball milling, and passing through a 200-mesh sieve;
[0025] Step S2, adding zinc dialkyldithiophosphate, sodium alginate, sodium lignosulfonate, sodium hexametaphosphate, polyethylene glycol and deionized water to the powder obtained in step S1, mixing into a mud, and ball milling 2 hour, sent to the calciner for calcination at 900°C for 1 hour;
[0026] Step S3, ball-milling the mixture calcined in step S2 again...
Embodiment 2
[0028] Embodiment 2: the preparation of ceramic composite material
[0029] Raw material weight ratio:
[0030] Zirconia, 55 parts; Aluminum oxide, 20 parts; Cerium oxide, 6 parts; Lanthanum oxide, 4 parts; Borax, 3 parts; Boron nitride, 1 part; Zinc dialkyldithiophosphate, 2 parts; Alginic acid Sodium, 0.6 parts; Sodium lignosulfonate, 0.4 parts; Sodium hexametaphosphate, 0.8 parts; Polyethylene glycol, 1 part; Deionized water, 7 parts.
[0031] Preparation:
[0032] Step S1, mixing zirconia, aluminum oxide, cerium oxide, lanthanum oxide, borax and boron nitride, ball milling, and passing through a 200-mesh sieve;
[0033] Step S2, adding zinc dialkyldithiophosphate, sodium alginate, sodium lignosulfonate, sodium hexametaphosphate, polyethylene glycol and deionized water to the powder obtained in step S1, mixing into a mud, and ball milling 2 hour, sent to the calciner for calcination at 900°C for 1 hour;
[0034] Step S3, ball-milling the mixture calcined in step S2 agai...
Embodiment 3
[0036] Embodiment 3: the preparation of ceramic composite material
[0037] Raw material weight ratio:
[0038] Zirconia, 65 parts; Aluminum oxide, 30 parts; Cerium oxide, 8 parts; Lanthanum oxide, 6 parts; Borax, 5 parts; Boron nitride, 3 parts; Zinc dialkyldithiophosphate, 4 parts; Alginic acid Sodium, 0.8 parts; Sodium lignosulfonate, 0.6 parts; Sodium hexametaphosphate, 1.2 parts; Polyethylene glycol, 3 parts; Deionized water, 9 parts.
[0039] Preparation:
[0040] Step S1, mixing zirconia, aluminum oxide, cerium oxide, lanthanum oxide, borax and boron nitride, ball milling, and passing through a 200-mesh sieve;
[0041] Step S2, adding zinc dialkyldithiophosphate, sodium alginate, sodium lignosulfonate, sodium hexametaphosphate, polyethylene glycol and deionized water to the powder obtained in step S1, mixing into a mud, and ball milling 2 hour, sent to the calciner for calcination at 900°C for 1 hour;
[0042] Step S3, ball-milling the mixture calcined in step S2 ag...
PUM
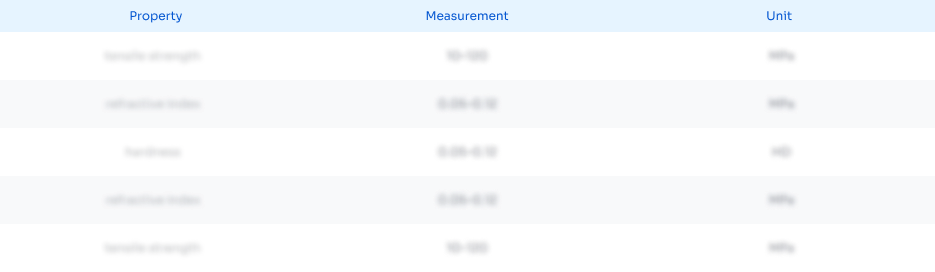
Abstract
Description
Claims
Application Information

- Generate Ideas
- Intellectual Property
- Life Sciences
- Materials
- Tech Scout
- Unparalleled Data Quality
- Higher Quality Content
- 60% Fewer Hallucinations
Browse by: Latest US Patents, China's latest patents, Technical Efficacy Thesaurus, Application Domain, Technology Topic, Popular Technical Reports.
© 2025 PatSnap. All rights reserved.Legal|Privacy policy|Modern Slavery Act Transparency Statement|Sitemap|About US| Contact US: help@patsnap.com