Method for preparing chromium iron black from electroplated chromium-containing waste water in recycling mode
A technology for chromium wastewater and ferrochromium black, which is applied in chemical instruments and methods, metallurgical wastewater treatment, iron oxide/iron hydroxide and other directions, can solve the problems of high operating costs, secondary pollutants, and large equipment, and achieves a solution to the treatment difficult, well-saturated effects
- Summary
- Abstract
- Description
- Claims
- Application Information
AI Technical Summary
Problems solved by technology
Method used
Examples
Embodiment 1
[0034] The electroplating chromium-containing wastewater of an electronics company was determined to be: total chromium 5.2g / L, chromium (Ⅵ) 4.6g / L, chromium (Ⅲ) 0.6g / L, SO 4 2- 4.6g / L, total iron 380mg / L, pH=1.
[0035] Step 1. Use liquid alkali to adjust the pH of the chromium-containing wastewater to 9, and add hydrogen peroxide to oxidize chromium (Ⅲ) to chromium (Ⅵ). The amount of hydrogen peroxide is 1.05 times the theoretical mass required by chemistry to ensure that chromium (Ⅲ) is completely oxidized , the reaction equation is as follows:
[0036] 2Cr[(OH) 4 ] - +3H 2o 2 +2OH - =2CrO 4 2- +8H 2 o
[0037] Step 2. For the oxidized electroplating chromium-containing wastewater, adjust the pH to 4 with sulfuric acid solution, and add ferrous sulfate, that is, total chromium and FeSO 4 ·7H 2 O mass ratio is 1:2.6, stirs 30min under normal temperature, obtains reaction solution;
[0038] Step 3. Add liquid caustic soda to the reaction solution obtained in step...
Embodiment 2
[0054] A company's electroplating chromium-containing wastewater, the water quality of the wastewater was determined to be: total chromium 2.9g / L, chromium (Ⅵ) 1.9g / L, chromium (Ⅲ) 1.0g / L, SO 4 2- 2.4g / L, total iron 203mg / L, pH=3.
[0055] Step 1. Adjust the pH of electroplating chromium-containing wastewater to 9 with liquid alkali, add sodium hypochlorite to oxidize chromium (Ⅲ) to chromium (Ⅵ), and the dosage is 1.05 times the theoretical mass required by chemistry to ensure that chromium (Ⅲ) is Complete oxidation, the reaction equation is as follows:
[0056] 2[Cr(OH) 4 ] - +3ClO - +2OH - = 3Cl - +2CrO 4 2- +5H 2 o
[0057] Step 2, adjust the pH of the oxidized electroplating chromium-containing wastewater to 4 with sulfuric acid, add iron powder at a ratio of 1:0.5 to the mass ratio of ferrochromium, and stir for 30 minutes at normal temperature to obtain a reaction solution;
[0058] Step 3, add liquid caustic soda to the reaction solution obtained in step 2, ...
PUM
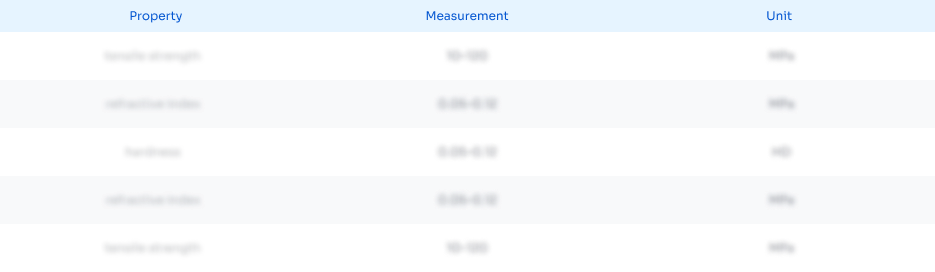
Abstract
Description
Claims
Application Information

- R&D
- Intellectual Property
- Life Sciences
- Materials
- Tech Scout
- Unparalleled Data Quality
- Higher Quality Content
- 60% Fewer Hallucinations
Browse by: Latest US Patents, China's latest patents, Technical Efficacy Thesaurus, Application Domain, Technology Topic, Popular Technical Reports.
© 2025 PatSnap. All rights reserved.Legal|Privacy policy|Modern Slavery Act Transparency Statement|Sitemap|About US| Contact US: help@patsnap.com