Preparation method of adsorption-type attapulgite-based flame-retardant material
A flame retardant material and attapulgite technology are applied in the field of preparation of adsorption-type attapulgite-based flame retardant materials, which can solve the problems of large filling amount, poor compatibility of polymer materials, smoke generation and the like, and reduce toxic gases , good flame retardant effect, the effect of reducing the burning temperature
- Summary
- Abstract
- Description
- Claims
- Application Information
AI Technical Summary
Problems solved by technology
Method used
Examples
Embodiment 1
[0015] Example 1: Prepare attapulgite-based flame retardant material according to the following steps
[0016] (1) Disperse 0.1 kg of adsorption-type attapulgite in 1.0 kg of formaldehyde solution with a mass fraction of 37% to obtain attapulgite suspension; add 1.56 kg of melamine to the suspension, and use hydrogen with a mass concentration of 10% Sodium oxide adjusts the pH of the system to 9, and continues stirring for 1 hour; raises the temperature of the system to 85°C, and stirs for 30 minutes; adjusts the pH of the system to 4.5 with formic acid with a mass concentration of 10%, and continues stirring for 20 minutes; adjusts the pH of the system The value is 9, cooled to room temperature;
[0017] (2) Dry the slurry obtained in step (1) at a temperature of 80° C., and pulverize to obtain an attapulgite-based flame-retardant material.
Embodiment 2
[0018] Example 2: Prepare attapulgite-based flame retardant material according to the following steps
[0019] (1) Disperse 0.3 kg of adsorption-type attapulgite in 1.0 kg of formaldehyde solution with a mass fraction of 37% to obtain a suspension of attapulgite; add 4.67 kg of melamine to the suspension, and use hydrogen with a mass concentration of 10% Sodium oxide adjusts the pH of the system to 8, and continues stirring for 3 hours; raises the temperature of the system to 70°C, and stirs for 45 minutes; adjusts the pH of the system to 5.5 with formic acid with a mass concentration of 10%, and continues stirring for 40 minutes; adjusts the pH of the system Value is 7.5, cooled to room temperature;
[0020] (2) Dry the slurry obtained in step (1) at a temperature of 90° C., and pulverize to obtain an attapulgite-based flame-retardant material.
Embodiment 3
[0021] Example 3: Prepare attapulgite-based flame retardant material according to the following steps
[0022] (1) Disperse 0.2 kg of adsorption-type attapulgite in 1.0 kg of formaldehyde solution with a mass fraction of 37% to obtain a suspension of attapulgite; add 3.10 kg of melamine to the suspension, and oxidize it with 10% hydrogen Adjust the pH value of the system to 8.5 with sodium, and continue stirring for 2 hours; raise the temperature of the system to 80°C, and stir for 40 minutes; adjust the pH of the system to 5.0 with formic acid with a mass concentration of 10%, and continue stirring for 30 minutes; adjust the pH of the system to 8.5, cooled to room temperature;
[0023] (2) Dry the slurry obtained in step (1) at a temperature of 85° C., and pulverize to obtain an attapulgite-based flame-retardant material.
PUM
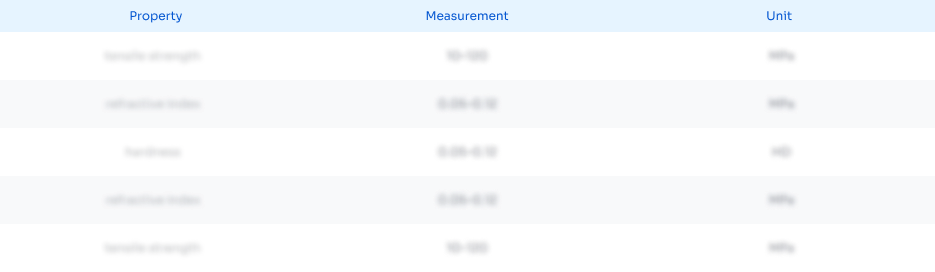
Abstract
Description
Claims
Application Information

- R&D
- Intellectual Property
- Life Sciences
- Materials
- Tech Scout
- Unparalleled Data Quality
- Higher Quality Content
- 60% Fewer Hallucinations
Browse by: Latest US Patents, China's latest patents, Technical Efficacy Thesaurus, Application Domain, Technology Topic, Popular Technical Reports.
© 2025 PatSnap. All rights reserved.Legal|Privacy policy|Modern Slavery Act Transparency Statement|Sitemap|About US| Contact US: help@patsnap.com