A method for smelting reduction recovery and quenching and tempering treatment of titanium-containing mixed slag
A technology of quenching and tempering treatment and slag, which is applied in the field of smelting reduction recovery and quenching and tempering treatment of titanium-containing mixed slag, which can solve the problems of hard-grinding ore, large amount of slag, and shortened service life, and achieve efficient recycling and efficient comprehensive utilization of resources Effect
- Summary
- Abstract
- Description
- Claims
- Application Information
AI Technical Summary
Problems solved by technology
Method used
Image
Examples
Embodiment 1
[0131] A method for smelting reduction recovery and quenching and tempering treatment of titanium-containing mixed slag, specifically comprising the following steps:
[0132] Step 1, slag mixing:
[0133] Pour 410kg of liquid molten titanium-containing blast furnace slag flowing out of the slag outlet and 40kg of converter vanadium-titanium-containing molten steel slag into a pourable thermal insulation slag tank with a graphite-dolomite composite thermal insulation and demoulding refractory material in the inner layer, and fully mix to form a titanium-containing slag tank. Mixing slag, smelting reduction reaction occurs;
[0134] The temperature of the slag after mixing is 1394°C, which is lower than the set temperature range of 1400-1600°C for the titanium-containing mixed slag; insert the refractory spray gun into the mixed slag and blow 2kg of coal powder to raise the temperature of the mixed slag to 1426 °C; where:
[0135] Titanium-containing blast furnace slag, contai...
Embodiment 2
[0151] A method for recycling and quenching and tempering treatment of titanium-containing mixed slag, specifically comprising the following steps:
[0152] Step 1, slag mixing:
[0153]Pour the molten 100kg titanium-containing blast furnace slag and 1000kg converter vanadium-titanium molten steel slag flowing out of the slag outlet into the insulation pit with carbon-magnesium composite thermal insulation and demoulding refractory material in the inner layer, and fully mix to form titanium-containing mixed slag. A smelting reduction reaction occurs; the temperature of the slag after mixing is 1570°C, and the temperature of the titanium-containing mixed slag is set within the range of 1400-1600°C; where:
[0154] Titanium-containing blast furnace slag, containing components and their mass percentages: 22.65wt% TiO 2 , 19.79wt% CaO, 9.31wt% MgO, 11.96wt% Al 2 o 3 , 3.26wt% FeO, and 19.48wt% SiO 2 , the balance is other impurities;
[0155] Composition and mass percentage o...
Embodiment 3
[0172] A method for recycling and quenching and tempering treatment of titanium-containing mixed slag, specifically comprising the following steps:
[0173] Step 1, slag mixing:
[0174] Pour 400kg of molten titanium-containing blast furnace slag and 45kg of vanadium-titanium-containing molten steel slag flowing out of the slag outlet into the heat preservation pit with metallurgical coke-high aluminum composite thermal insulation and demolding refractory material in the inner layer, and fully mix to form a titanium-containing mixed molten steel slag. Slag, smelting reduction reaction occurs; the temperature of the slag after mixing is 1420°C; the temperature control range of the titanium-containing mixed slag is 1400-1600°C; where:
[0175] Titanium-containing blast furnace slag, containing components and mass percentages: 21.96wt% TiO 2 , 20.37wt% CaO, 8.75wt% MgO, 11.62wt% Al 2 o 3 , 4.4.46wt% FeO, and 19.28wt% SiO 2 , the balance is other impurities;
[0176] Vanadium...
PUM
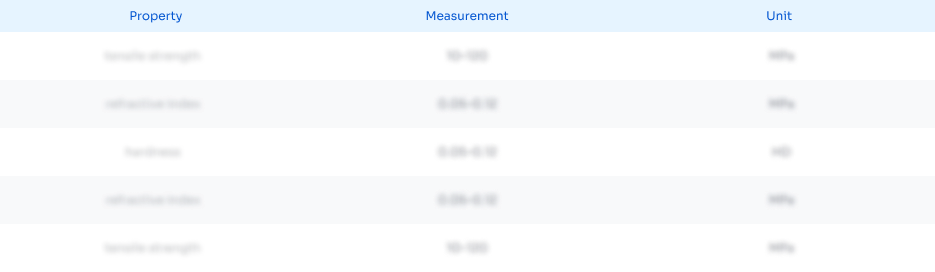
Abstract
Description
Claims
Application Information

- R&D Engineer
- R&D Manager
- IP Professional
- Industry Leading Data Capabilities
- Powerful AI technology
- Patent DNA Extraction
Browse by: Latest US Patents, China's latest patents, Technical Efficacy Thesaurus, Application Domain, Technology Topic, Popular Technical Reports.
© 2024 PatSnap. All rights reserved.Legal|Privacy policy|Modern Slavery Act Transparency Statement|Sitemap|About US| Contact US: help@patsnap.com