Heavy oil hydrogenation catalyst and application thereof
A heavy oil hydrogenation and catalyst technology, which is applied in the field of heavy oil hydrotreating and heavy oil hydrotreating catalysts, can solve the problem of reducing the active center of the catalyst surface and achieve a good effect of hydrodesulfurization
- Summary
- Abstract
- Description
- Claims
- Application Information
AI Technical Summary
Problems solved by technology
Method used
Image
Examples
Embodiment 1
[0046] The pseudo-boehmite dry rubber powder RPB90 produced by 1 kilogram of Changling Catalyst Factory and 30 grams of turnip powder and 25 grams of titanium dioxide are mixed uniformly, and at room temperature, the mixture is mixed with 20 milliliters of nitric acid (65% by mass fraction) 1.1 liters of the aqueous solution was mixed evenly, and after being kneaded into a plastic body on a twin-screw extruder, extruded into a trilobal strip of ф1.1 mm, the wet strip was dried at 120°C for 3 hours, and then roasted at 600°C for 3 hours to obtain Titanium shaped alumina support Z1. The physical and chemical results of the determination of Z1 are shown in Table 1.
Embodiment 2
[0048] The pseudo-boehmite dry rubber powder RPB100 produced by 1 kilogram of Changling Catalyst Factory is mixed with 30 grams of turnip powder and 40 grams of titanium dioxide. Mix 1.2 liters of aqueous solution evenly, continue kneading on a twin-screw extruder to form a plastic body, and then extrude it into a butterfly-shaped strip of ф1.1mm. After the wet strip is dried at 110°C for 2 hours, it is roasted at 700°C for 3 hours to obtain a titanium-containing molding. Alumina support Z2. The physical and chemical results of the determination of Z2 are shown in Table 1.
Embodiment 3
[0051] Weigh 150g of the Z1 carrier and place it in the hydration kettle, add 450g of deionized water, seal the hydration kettle and put it in the oven, heat it with a programmed temperature rise, and control the heating rate to 10°C·min -1 , the treatment temperature is 80° C., and the treatment time is 12 hours. After the completion of the hydrothermal treatment, the alumina was filtered, and then dried at 120° C. for 3 hours to obtain a hydrothermally treated alumina carrier.
[0052] Take 100 grams of carrier Z1 after heat treatment in water, and use 220 milliliters of MoO 3 170 g / L, NiO 30 g / L mixed solution of ammonium molybdate and nickel nitrate was impregnated for 1 hour, filtered, dried at 120°C for 2 hours, and calcined at 410°C for 4 hours to obtain catalyst C1. Calculated by oxide and based on the load on the surface of the unit carrier, the content of molybdenum oxide and nickel oxide in catalyst C1 is measured by X-ray fluorescence spectrometer, and whether mol...
PUM
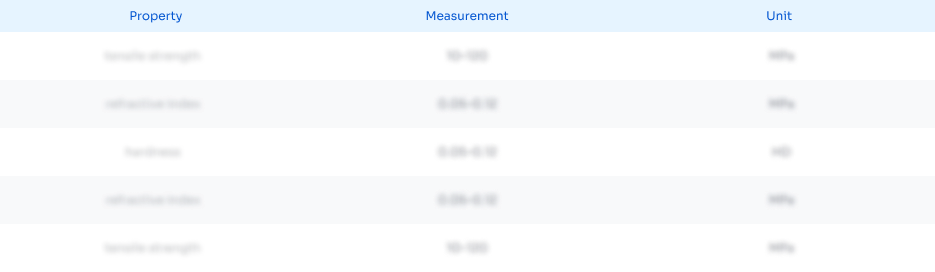
Abstract
Description
Claims
Application Information

- Generate Ideas
- Intellectual Property
- Life Sciences
- Materials
- Tech Scout
- Unparalleled Data Quality
- Higher Quality Content
- 60% Fewer Hallucinations
Browse by: Latest US Patents, China's latest patents, Technical Efficacy Thesaurus, Application Domain, Technology Topic, Popular Technical Reports.
© 2025 PatSnap. All rights reserved.Legal|Privacy policy|Modern Slavery Act Transparency Statement|Sitemap|About US| Contact US: help@patsnap.com